Six Sigma is a framework designed to make an organization more competitive by focusing on being effective and efficient. It is a systematic problem-solving approach centered around defect elimination and variation reduction, leading to process improvement.
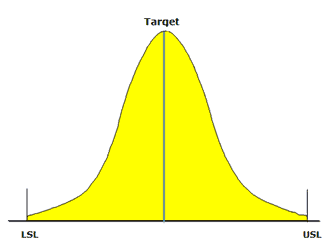
Specifically, Six Sigma is a continuous improvement process with a focus on the following:
- Change empowerment
- Seamless training of resources
- Consistent top management support

Six Sigma refers to the practice of delivering products and services that perform at high standards. It is a Quality Philosophy and a management technique. However, it is not a standard, certification, or metric like a percentage.
Six Sigma’s Basic Premises
The purpose of Six Sigma is to satisfy customers by producing quality products. Hence, it focuses on variation reduction and waste elimination. This leads to increased efficiency.
Variation is the range of difference between the statistical mean and all data points that are used to calculate the mean. In other words, the extent to which process performance varies around the mean.
Waste or defects are measurable product characteristics that do not meet the requirements of the customer (i.e. defective products). In other words, any process performance outside of the defined specification is considered waste or a defect.
Six Sigma methodologies are used to identify and remove the root cause of defects or reduce the process variation (using statistical or process analysis methods) and also the costs that are associated with it.
For example, let’s say XYZ factory produces widgets. The widgets are all supposed to be a certain size, shape, and weight. Now, randomly sampled output discovers that out of every 1,000 widgets, fifty are flawed (e.g. wrong size, shape, or weight). To correct this, the factory uses Six Sigma to determine what’s causing the variation/defects and works to reduce them to a six-sigma level.
Six Sigma’s Approach to Problem Solving
The term Six Sigma was first coined by American engineer Bill Smith, who is known as the father of Six Sigma. While working at Motorola in the year 1986, Smith created Six Sigma as a general approach to measuring quality in business performance terms. Later, it became a popular management approach at GE with Jack Welch in the early 1990s.
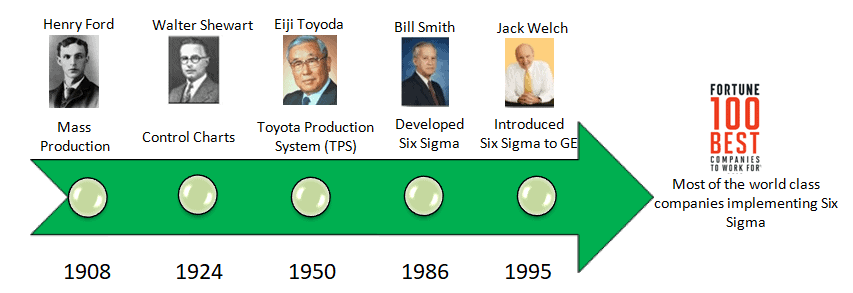
General Electric recognized benefits of $2.5 billion per year due to Six Sigma policies and made it a company-wide strategy. Now, it has become a project-driven approach for process improvements that follows the five-step process, also called the DMAIC cycle. (Also see: History of Continuous Improvement).
Overview Video
What is a Six Sigma Level?
Six Sigma derives from the normal or bell curve in statistics, where each interval indicates one sigma or one standard deviation. Moreover, sigma is a statistical term that refers to the standard deviation of a process around its mean. In a normally distributed process, 99.73% of measurement will fall within ±3σ, and 99.99932% will fall within ±4.5σ.
For a process, the sigma capability is a metric that shows how well that process is performing. Hence the higher the sigma value, the better the process.
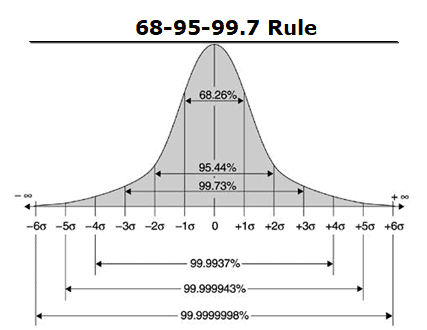
The 68-95-99.7 rule, also known as an empirical rule, is used to remember the percentage of values that lie within a band around the mean in a normal distribution with a width of one, two, and three standard deviations.
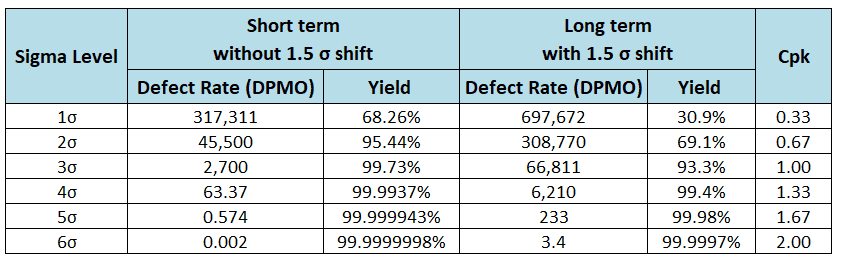
A six sigma capable process will have Cp >= 2.0, Cpk >= 2.0 and DPMO = 3.4
Where Does the 6 and Sigma come from?
Let’s cover Sigma first. Sigma, denoted by the symbol σ (a Greek letter), represents the standard deviation of a population. Primarily, it represents the dispersion (or ‘spread’) of a set of data values with respect to mean. A standard deviation is a value you have to calculate and is dependent on the data your process generates.
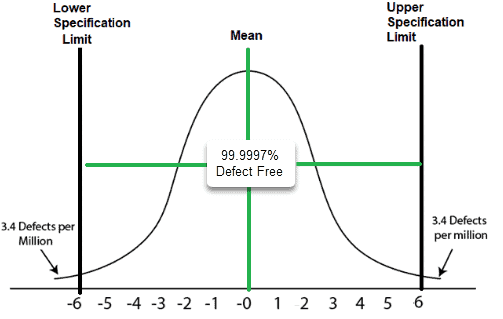
Now let’s cover the 6. The six refers to how many standard deviations away from the mean we set the specification limits in a 6 sigma process.
Now let’s put them together for 6 Sigma: A Six Sigma process has a specification limit that is 6 times its sigma (standard deviation) away from its mean. The 6 refers to the ability to fit the good outputs of the process to fit within 6 standard deviations (or sigmas). Another way to say it is that only 3.4 defects per every million products fall outside the limits we’ve set at 6 sigmas away from the center.
Additionally, you can also think of it as a level of excellence that can be quantified and easily compared against other processes. If you only get 3.4 defects per million out of your process, i.e. a 99.9999998% success rate, you have a 6 sigma process.
Other Sigma Levels
For each standard deviation away from the mean (0 in the graphic above), your process gets more and more defect-free. Let’s look at a 3 Sigma process, for example. In a normally distributed process, if the mean ±3σ range of output is between USL and LSL, then around 99.73% of the points of the output will be non-defective.
Is Six Sigma ONLY for Reducing Defects?
Absolutely no! While Six Sigma is primarily known for its focus on reducing defects, it is actually a comprehensive approach to quality improvement that can be applied to a wide range of business processes. In addition to reducing defects, Six Sigma can also be used to improve process efficiency, reduce waste, improve customer satisfaction, and increase profitability.
The core philosophy of Six Sigma is to focus on meeting or exceeding customer expectations by reducing variation and improving process performance. By using statistical tools and data analysis, Six Sigma practitioners can identify the root causes of problems and develop solutions to improve process performance and meet customer needs.
While reducing defects is certainly an important goal in many industries, the broader focus of Six Sigma is to improve overall business performance by reducing variation and improving quality. By improving processes and reducing waste, organizations can increase efficiency, reduce costs, and ultimately deliver greater value to their customers.
The Primary Goals are to Improve
Six Sigma is a data-driven methodology that uses statistical tools and techniques to define the problem and evaluate each process step. In addition, it provides ways to create an efficient business structure, improve the quality of the operations in an organization, and increase the bottom-line profit.
Three Key Elements of Six Sigma
- Customers: Customers are the key to business, and they are the top priority. Customers define the quality requirements and expect on-time delivery, high performance, great service, and many more. However, meeting customer requirements is not enough in the business world.
- Process: Defining the process and important metrics is the key aspect of Six Sigma. Since the customer is key for any business, quality needs to be looked at from the customer’s perspective. This helps to identify the gaps in processes and the work necessary to improve them.
- Employee: Without leadership commitment, using Six Sigma in any organization is difficult. The organization must involve all employees with well-defined roles and clear objectives. Furthermore, organizations must provide required resources like people, training, budget, and more.
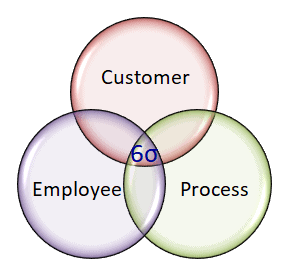
Philosophy & Methodology
Six Sigma is a result-oriented, continuous improvement process that includes active involvement from senior management.
Continuous improvement activities in an organization help ensure that problems are identified and solved when they occur. Most of the modern quality improvement models, such as sampling techniques, control charts, process capability, and DOE have been influenced by the theory of continuous improvement.
Why Use Six Sigma?
Organizations face new challenges every day, like rising costs, customer issues, an increase in defect rate, etc. In fact, global competition has made it critical to provide perfect quality at a low cost to keep customers happy and to make organizations viable in the marketplace. Some of the key benefits of using Six Sigma include the following:
- Creates robust products and services
- Ensures customer satisfaction
- Reduces process variation and eliminates waste
- Eliminates the root causes of problems and defects in a process
- Reduces rework by getting it right the first time
- Addresses key organization business requirements
- Competitive advantage
Six Sigma Methodologies
Six Sigma provides better value to customers, employees, and all the stakeholders in an organization. Additionally, it is a business initiative that improves quality and productivity and reduces costs.
DMAIC
One of the basic tools in Six Sigma is the use of the DMAIC methodology. (Also see DMAIC Overview). Particularly, DMAIC is a logical framework that helps you think through a process, plan improvements, and achieve a Six Sigma level of quality. In other words, it is a data-driven quality strategy for a better process.
There are five phases in the DMAIC method. They are as follows:
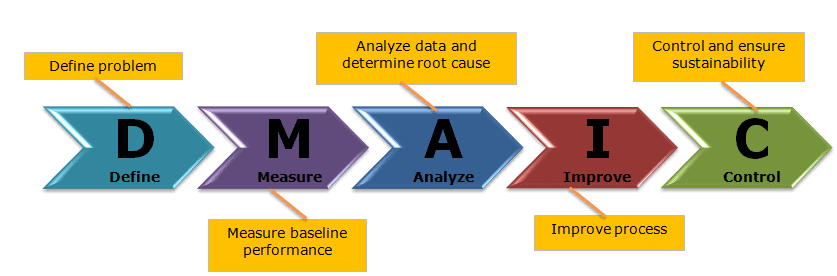
- Define: Define the problem and also project goals that need to be addressed.
- Measure: Measure the baseline performance and confirm the practical problem by collecting data
- Analyze: Analyze the data to determine the root causes of the problems and then identify opportunities for improvements.
- Improve: Improve the process and test the statistical solution.
- Control: Start using a new process for production. Implement, control, and ensure sustainability. Finally, measure the new process based on customer reactions.
Six Sigma teams define the problem, work with sponsors and stakeholders, and deliver results that will be reviewed at phase-gate meetings called DMAIC Tollgate Reviews.
DMADV
DMADV is one aspect of Design for Six Sigma (DFSS). In fact, this evolved from the continuous quality improvement and Six Sigma approach to reduce variation. However, DMADV aims to create new processes and new products or services.
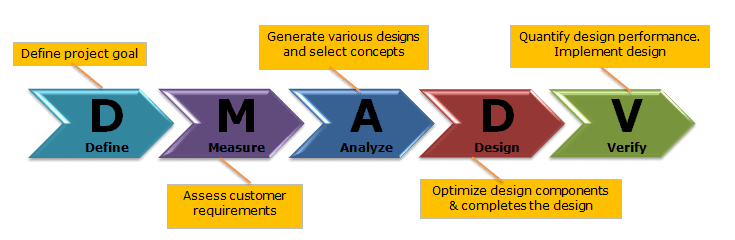
- Define: Determine the project need and also identify the goals
- Measure: Assess customer needs and prioritize requirements
- Analyze: Analyze data, generate various designs, and select concepts
- Design: Optimize design components and completes the design
- Verify: Validate and quantify the design performance.
Six Sigma Frequently Asked Questions
What is the concept of Six Sigma?
Six Sigma refers to the methodology and practice of focusing on developing and delivering products/services that perform at high standards. It is a Quality Philosophy and a management technique. It is a systematic problem-solving approach centered around defect elimination and variation reduction, leading to process improvement.
What are the Five steps of six sigma?
- Define: Define the problem and also project goals that need to be addressed
- Measure: Measure the baseline performance and validate the practical problem by collecting data
- Analyze: Analyze the data to determine the root causes of the problems and opportunities for improvement
- Improve: Improve the process and test the statistical solution
- Control: Start using a new process for production. Implement, control, and ensure sustainability. Finally, measure the new process based on customer reactions.
Why is it called six sigma?
Sigma, denoted by the symbol σ (a Greek letter), represents the standard deviation of a population. Particularly, it characterizes the dispersion (or ‘spread’) of a set of data values with respect to mean.
A Six Sigma process has a specification limit that is 6 times its sigma (standard deviation) away from its mean. In other words, the 6 refers to the ability to fit the good outputs of the process to fit within 6 standard deviations (or sigmas). Another way to say it is that only 3.4 defects per every million opportunities fall outside the specification limits that we’ve set at 6 sigmas away from the center.
What is an example of Six Sigma?
Six Sigma means producing a defect-free product 99.9996% of the time, allowing only 3.4 defects per million opportunities.
Also, refer to a few examples of Six sigma implementation:
- https://smallbusiness.chron.com/six-sigma-implementation-examples-13441.html
- https://www.invensislearning.com/blog/six-sigma-examples/
What are 6 Sigma tools?
- DMAIC: DMAIC is Six Sigma’s signature framework for process improvement. It provides a structured way of improving a process.
- 5S: 5S Workplace Organization is A visual system. Also, a Kaizen event. 5S derives its name from five Japanese terms beginning with the “s” to create a workplace suited for visual control and lean production.
- Seven Wastes: Seven Wastes are looked at as challenges to productivity. In a highly competitive world, it is not possible to enhance the top line by increasing the prices, hence, it is necessary to build effective systems, and one of the ways is to understand the ‘wastages’ and eliminate them.
- VSM: Value stream mapping provides a visual representation of the flow of materials and information throughout the organization. It helps to identify, demonstrate, reduce waste and finally create effective flow through all the processes in the manufacturing organization.
- Process Map: A process map is a tool that shows the inputs, actions, and outputs of a process in a clear, step-by-step map of the process.
- Voice Of Customer (VOC): Organizations to understand the needs and expectations of the customer to design the product and services well. Moreover, customers will weigh the value of a product based on the cost, quality, availability, and features.
- Kaizen: Kaizen means an improvement on a continuous basis. Originating in Japan, Kai means change and zen means for good.
Which companies are using Six Sigma?
Six Sigma was coined by Bill Smith, an American engineer who is known as the father of Six Sigma. At the same time, he first implemented Six Sigma at Motorola in the year 1986 as a general approach to measuring quality in business performance terms.
Also, see the companies that have embraced Six Sigma: Motorola, General Electric, Dupont, Sony, Kodak, Boeing, Johnson & Johnson, 3M, Amazon, Atos, Autoliv, BAE Systems, Bank of America, Becton Dickinson, Bechtel, etc.,
Amusing: How this conversation usually goes:
The Basics Videos
Additional Articles
Six Sigma Black Belt Certification Questions:
Question: The primary reason that most companies implement Six Sigma is to: (Taken from ASQ sample Black Belt exam.)
(A) reduce defects
(B) improve processes
(C) improve profit
(D) increase customer satisfaction
Answer:
C: The primary reason companies implement Six Sigma is to improve profit. Obviously, a non-profit might have other goals (like being a better custodian of their source funds in pursuit of their mission. However, when looking at the other options listed, each of them would be done in service of the improved profit answer.
Comments (76)
Great web page!
Thanks, Dennis. Let me know if there is anything else I can add to make the site more helpful.
Greetings,
Is there any pre-requisites for enrolling for LSS? I have 13 yeasr of experience in BPO’s and Call Centers and thinking of movie to some other verticals but for that I need to go for certain certifications then I came across your site. So thought to better consult so that you can guide me in the better direction.
Hi Raj,
There are no prerequisites for enrolling in Six Sigma training other than a will to learn!
Different certifying organizations do have different requirements on what they require to let you be certified though.
Best, Ted.
How do I take six sigma exam from Villanova university?can you comment on Moresteam and Villanova university exam.can we take the the exam in parts or at the sam grime.thankig you.Regrds.Dr.K.Kumar
Hi Dr. Kumar,
You can take the Villanova exam by registering for their Six Sigma Black Belt course. The exam comes after 6-8 weeks of training (if memory serves) and after you complete the example project.
I ma not personally familiar with Moresteam but some colleagues have recently used their training to prepare – and pass – the ASQ Six Sigma Black Belt exam.
Hope that helps!
hello,
i am interested in pursuing lean six sigma black belt. After some research I ended up with ASQ , LSSA (APMG), IASSC.
appreciate if you could guide me on selecting one of them. I am struggling to select one of them or understand the differences between them .
regards,
Mo
Mo – thanks for coming to the site. Here’s an article on how to choose a certification.
There is an error in the diagram of six sigmas, it only shows three sigmas. (99.5%) Six sigmas is six standard deviations on a single side of the mean.
No, that is incorrect. The diagram is accurate.
I was under the same impression, Six Sigmas on either side, otherwise you end up with 5 bad parts in 1000, not the 3.4 DPMO. I have a hard time finding this information elsewhere on the internet.
Can you elaborate on why it is 3 sigmas on either side and not 6?
Hi Michael,
I’ll look for a concise way to demonstrate this. In the meantime, please refer to these articles (and videos and images therein.)
Z Scores and Process Sigma.
How to determine baseline sigma.
Short answer is that the center of curve is the mean of the process. 6 sigmas represent nearly all of the possible outcomes. If the center is the mean, you’d expect half of the possibilities to fall on either side (in a normal distribution.) Half of 6 is 3, thus 3 sigmas on each side of the center.
That’s not true…A six sigma process operates with Cp=2
Cp=USL-LSL/6s
USL-LSL=12s
So the natural tolerance needs to be 6 sigma on either side of the mean.
Hi, I am new to Six Sigma but have lots of experience in working on lean projects. How do i start with six sigma . Is yellow belt certification from ASQ is the right way to start. Is there any study materials you suggest.
Thanks
Hi Steven,
I’ve really seen no use in pursuing yellow belts. Perhaps it’s a good way to quickly get recognized for knowledge you already have and add a resume item, but even then I’ve not seen employers value them. Perhaps other people’s experiences are different.
I think the right way to address your question is to begin with the end in mind. What is it that you want to accomplish. If you want to be able to effectively participate in lean six sigma projects and begin to get an understanding of the whole, I’d pursue the green belt. If you are looking to be a change agent and lead six sigma projects, I’d pursue Black Belt training and certification.
Either way, I think this website has the best available (and free!) study guides. Start by answering the survey here – it will help me provide exactly what you are looking for and will sign you up for our free email series that will logically lay out a course of action.
Remember, you can always see what the ASQ Green Belt exam or the ASQ Black Belt exam entails by clicking those links.
Quite Informative, thanks for all your help
Thanks, Steven.
I would like to obtain study material for Black Belt training and certification
Hi Corwin. I think this website has the best available (and free!) study guides. Start by answering the survey here – it will help me provide exactly what you are looking for and will sign you up for our free email series that will logically lay out a course of action.
Remember, you can always see what the ASQ Green Belt exam or the ASQ Black Belt exam entails by clicking those links.
Hi! Dan,
I am little bit confuse about this answer which says that improve profit would be the primary goal to adopt six sigma. We know sigma is directly related to DPMO ( it talks about defect which due to process variation ) so in this sense ans should be A.
Hi Ajay, we’re talking about 2 different things here. For a company or an enterprise to adopt the philosophy of Six Sigma the biggest driver is improving the bottom line. If you want to calculate the Sigma of a process, you would calculate DPMO. Make sense?
I seem to agree with Ajay on the aspect of confusion,but on my part “philosophically” I see as if part D, customer Satisfaction. In this sense,I’m looking at a customer not only from buying and selling perspective but also for non profit entities.
Try thinking about profit in terms of it being the single biggest driver of being able to keep a company afloat.
If that’s not the case, say for a non-profit, I’d substitute it for something that is. To my mind non-profits cannot work without funding. So in that case replace with whatever can secure that non-profit funding.
Also, there are many, many non-profits that make tremendous amounts of money. That money allows them to serve their mission. However, without the money there is no serving a mission.
I would look at the profit being the dependent variable and the rest independent variables.
I would look at it as the direction of the Cause and Effect diagram
If profit option is not given in choices then what would be the second best answer?
Hi Goheer,
The next best choice would be something that directly relates to improving profit.
There is an error in the last diagram. 6 sigma means +/- 6 sigma which means 6 deviations on either side.
We re-worked this article for clarity and added more graphics. Can you give a read through now and see if it’s clear?
I have to agree with the other posters and say that the graph is incorrect. Please do us a favor and correct this page, as I’m afraid it will be misleading to people who are using it as a study guide. See below website for a correct illustration of a six sigma graph:
http://leansixsigmadefinition.com/glossary/six-sigma/
We re-worked this article for clarity and added more graphics. Can you give a read through now and see if it’s clear?
The six sigma diagram has an 2 arrows indicating 3.4 defects on either side of the specification limits…wouldn’t it be 1.7 on either side for a total of 3.4 defects per million opportunities?
Hello Edward King-Kovach,
Six Sigma means producing a defect-free product 99.9997% of the time, allowing only 3.4 defects/million opportunities. If you only get 3.4 defects per million out of your process, i.e. a 99.999999% success rate, you have a 6 sigma process.
A Six Sigma process has a specification limit that is 6 times its sigma (standard deviation) away from its mean. The 6 refers to the ability to fit the good outputs of the process to fit within 6 standard deviations (or sigmas). Another way to say it is that only 3.4 defects per every million products fall outside the specification limits (either side of specification limits not 1.7 on each side) we’ve set at 6 sigmas away from the center.
Thanks
Two of the videos are “not available” can you please check them?
Seems that the creators on Youtube took them down. I’ll see what i can do to find or create a replacement.
I am benefiting from it. Thanks Ted.
I’m very happy to hear that, Christian!
A couple of the videos are not available for viewing.
Thanks, Ashley. It seems that people have taken down their YouTube videos. Time for me to get off the fence and make my own!
Hi Ted, Two videos are not accessible in this page
Thanks, Sandaru. Looks like the authors removed them from youtube. I’ll look for others to add.
That is fantastic, thanks
Glad it helps, Alicia! Thank you for the comment.
Hi Ted
Glad to see you chose a video by Beth Cudney. She facilitated the SSGB course at the University of Syracuse with IVMF. Ok, pushing forward…
Hi Sharon,
I had the chance to see Beth at the 2017 ASQ World Conference. She was presenting her method of teaching if I remember correctly. Sounded like her approach would be effective!
Hi,
There is a lot of back and forth with the above question regarding how many sigmas to the right and left of the center point.
“There is an error in the last diagram. 6 sigma means +/- 6 sigma which means 6 deviations on either side.”
Is it + or – 3 or + or – 6?
Jennifer, we re-worked this article for clarity and added more graphics. Can you give a read through now and see if it’s clear?
Best, Ted
Is that really a question from ASQ exam? because it seems so dark and inadequate… there is obviously no right answer to the question. How can i verify it is indeed a real question? because without verification it makes me feel all this page has fake information. Thank you!
Hi Ignacio,
That question is indeed from ASQ’s published practice exam. It is not mine.
You can verify by getting the published practice exam from ASQ.
Hi Ted,
I am an electrical engineer and i have done my PMP. I have seen the project requirements for ASQ and they lean more towards quality /accounting and production. I am into construction and we still apply Six Sigma but not to that extent as we would in manufacturing. I still want to get my black belt. I dont have manufacturing or production projects but do have construction projects. in my case which one do you recommend IASSC or ASQ.
Thanks for your help.
Hi Zoya,
I think that Six Sigma is appropriate to many, many industries, not just manufacturing. For example, I was able to earn black belt from two different organizations while working in financial software – ostensibly a service-based industry.
I think the choice between IASSC and ASQ comes down to what you want out of your certification, the kind of test-taker you are, and, at the black belt level, if you have a portfolio of accomplished projects or not. I have more on this topic here.
Best, Ted
Based on the Table (which can be confusing), 3.4 defects per million opportunities is actually 4.5 sigma. This is considering all “6 sigma” process over time would exhibit a drift (of 1.5 sigma) over a period of time (Long Term).
Hi Derek,
Thanks for your comment. Can you clarify? The table I have above has one section with a 1.5 shift and another without.
If you can tell me where it is confusing, I can make another that is less.
Best, Ted.
I don’t understand if 6Sigma aims to improve the mean or just reduce the variation.
Hi David,
It’s project-specific. But there’s some vocabulary to unpack here, too.
Sigma is a measure of variation, true. As you reduce variation of your process your Sigma level increases. If you get to a 6 Sigma level, you have very low variation in your process.
The 6 Sigma process is generally referred to as DMAIC, which is a structured problem solving framework where you solve a business issue. Solving that business issue might be changing the mean, median, mode of a process. It might be reducing variation and increasing your sigma level (possibly even to a 6 sigma level). It could be used to do many things. The guiding principal is solving the business problem you are chartered with solving.
Best, Ted
IS: The 68-95-99.7 rule also known as empirical rule used to remember the percentage of values that lie within a band around mean in a normal distribution with a width of two, four and six standard deviation respectively.
S/B: The 68-95-99.7 rule also known as empirical rule used to remember the percentage of values that lie within a band around mean in a normal distribution with a width of one, two and three standard deviation respectively.
Updated.
IS: A six sigma capable process will have Cp = 2.0, Cpk = 1.5 and DPMO = 3.4
The table directly above indicates Cpk = 2.0 at 6 sigma
Good catch. Updated.
In the graph under the heading: “Where Does the 6 and Sigma come from?”
at the text “99.997% Defect Free” The text should read: “99.9997% Defect Free”
Updated
IS: “Another way to say it is that only 3.4 defects occur per every million opportunities fall outside the control limits.”
S/B: “Another way to say it is that only 3.4 defects occur per every million opportunities fall outside the specification limits.”
The graph above the text does not show control limits.
Good catch, Greg. Thank you. I’ve also updated the entire section for more clarity.
Dear sir
Dear sir
Good wishes to you
I would request you to kindly permit me to use the six sigma table and graph from this article for using it in the book chapter to be published in book tentatively titled: Food Safety and Standards” edited by Dr. Vijayalakshmi D. and Dr. Barbhai Mrunal D. and to be published by NEW INDIA PUBLISHING AGENCY (NIPA), New Delhi.
Thanking you
Awaiting for your reply
Regards
Dr. Asha G
Sure, please just reference this website and link and authors.
Hi Ted,
where does the CSSC accreditation stand in relation to ASQ and IAASC accreditations?
Thanks,
Daragh
Hi Daragh,
I do not have first hand experience with CSSC so take my thoughts with a grain of salt. I have not seen employers specify that certification nearly as often as ASQ, which remains the gold standard in my opinion. I urge you to go to your favorite job board and verify / invalidate this for yourself, though.
Many people who visit this site do ask me about them. From what I can see in their BOK I like the use of the electronic toolsets (Minitab, Excel, etc). However, much like the IASSC there’s no experiential component. I have more thoughts on the most recognized Six Sigma certifications here.
Best, Ted.
Hi Ted,
I understand different people may require different study times however, I’m currently on a career break and have just passed Professional Scrum Master 1 to boost my knowledge on agile project management frameworks.
I’m interested to take the Lean Six Sigma certification and would like to have a go at Black belt instead of Green from IASSC due to lack of budget (so I don’t have to pay for Green and then Black) and actual project management experience.
In your opinion, how long would a person require to be prepared for the black belt if I can commit 35 hours a week. Also, would you be able to advise on green belt’s preparation time too.
Lastly, I understand good Mathematics is required but it’s been a while since I have actually used/ remember what was taught in school due to the lack of use. Would this greatly hinder me from passing the exam?
Thanks in advance.
Hi Alex,
Generically, I think it wouldn’t take long to be able to prepare for a passing grade. Depending on the student, I think the black belt could be done in as little as a month and unlikely longer than 3 months. I would guess that the green belt would take half of the time. An excellent way to ballpark this for yourself is to look at the IASSC BOKs and see how well you know the material. You can find my IASSC Green Belt and IASSC Black Belt BOKs here on these respective links. On each page, I have a link to each topic that the IASSC will test you on. Most IASSC candidates find it very helpful to review each article I have linked from the BOK.
On the math side, if you are comfortable with algebra, that handles most of the problems. After that, reviewing basic probability concepts and getting experience with the more robust statistical hypothesis equations is key.
Part of the equation to how long it will take you to pass is the organization you are certifying with. IASSC isn’t that demanding. It does require a lot of memorization. I would suggest downloading a copy of their exam day reference sheet and getting comfortable with it. This is the only reference material you are allowed to have beside you during the exam.
One other recommendation I have would be to get a baseline of your understanding by taking a practice test once you feel close to ready.
Thanks a lot for the information and really appreciate the guidance too, Tim.
I’ll get started working on the math side first as I’m not very confident with my algebra level now. Then I’ll sign up shortly for your black belt programme after reviewing your links on the Black Belt BOKs.
Once again, thanks for the great website and taking the time out in providing guidance.
You’re welcome, Alex!
Very welcome! Since you’re a member of our free program, I would suggest taking both of the sample exams provided there. You should get a good feel for the kind of algebra required. If you’d prefer a direct example, try out some of the questions and answers on our Takt time page.
Oh thanks but I haven’t really studied much so far so will take them when I’m better equipped. But thanks again! Will try them out in a week or two before upgrading the membership level.
Happy to help, Alex!
Is the site still active and updated?
Hi Marco – yes, this site is still active.