Takt time is the rate at which an organization needs to complete the production process in order to meet customer demand. In other words, it is the frequency at which one part or product should be produced to meet the customer’s requirements.
Takt time is used to synchronize the pace of production with the pace of sales. A sort of just-in-time production measure that helps remove and avoid waste.
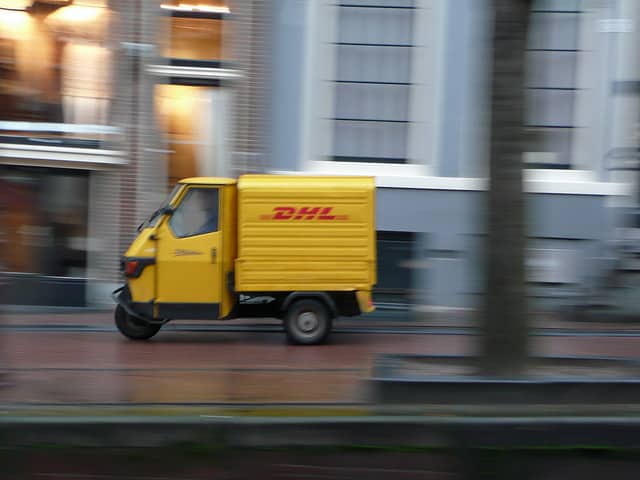
Takt is a German word for the baton that an orchestra conductor uses to regulate the tempo of the music. In 1830, it was first used in the German aircraft industry; later, the concept was widely applied in Toyota.
Why Takt time?
Defining Takt time is very critical to optimizing the process. It creates a constant pulse across the process. Takt time helps to highlight the capability issues and synchronize issues among the process. It ensures that all capacity in the manufacturing is planned and utilized and also meets customer demand. Nonetheless, Takt time helps to balance the customer demand and avoids overproduction.
Calculating Takt Time
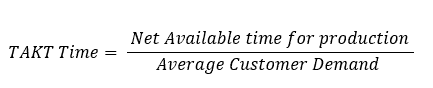
Step 1: Calculate the Net Available time
The net available time is the current production time after deducting unsupervised work time such as lunch, breaks, team meetings, or scheduled maintenance.
Note: If in case production is not stopping during lunch, breaks, and meetings, then we should not deduct those hours/minutes while calculating net working time.
Step 2: Calculate the Customer Demand
The customer demand is the average of sales by adding test parts, spare parts, and the percentage of rejects.
- The goal is to produce the demand
- Can only be changed if the available time or customer demand changes.
- Must be recalculated on a regular basis.
- Should drive staffing decisions and cell layout.
- Should NOT be adjusted to account for system problems.
- Pace the process to a planned cycle time to accommodate system problems.
Takt time Examples
Example 1:
Suppose your organization runs two shifts and the customer demand is 300 pieces; find the TAKT time.
- Number of shifts = 2
- Hours per shift =8 hours = 480 minutes
- Lunch time= 40 minutes
- Breaks =20 minutes
- Team meeting = 15 minutes
Net working time per shift = 480-40-20-15 = 405 minutes per shift = 810 minutes for two shifts
810 minutes / 300 pieces = 2.7 minutes per piece.
Example 2:
Customer demand = 30 units/hour.
The process can do the following: 1: 20/hr; 2: 40/hr; 3:12/hr; 16/hr.
Net operating time is 60 mins/hour. The process is irrelevant here. The customer requirements are 30 units per hour. 60 / 30 = 2 mins.
Example 3:
The output of a process has a Takt time of 60 seconds. Station 4 can only produce every 80 seconds. It exceeds the Takt time and is unable to keep pace.
Example 4:
A shop can work 430 mins a day.
The customer needs 300 units per day.
Takt time = 430 / 300 = 1.433 minutes per unit.
Example 5:
A manager wants to set up a Kanban system on an assembly process. The demand for the part produced in the target process is 75/units per hour, and the MLT of the process is 0.6 days. The factory operates two 8.5-hour shifts, with 30 minutes of break timer per shift. Assuming the safety stock should be set at 10% and container capacity is held at 10% of daily demand. How many Kanban card sets should be authorized?
Net available time = 8.5 + 8.5 = 17 hours per day (Note: Since it is a Kanban system, assuming that production did not stop during break time. Hence, we DO NOT subtract the 30-minute breaks.)
Customer demand = 75 units/hour * 24 hours per day = 1800 units per day.
Total demand = customer demand + safety stock + container capacity = 1800 + 0.1*1800 + 0.1*1800 = 2160
So, Takt time = Net Available time / Customer Demand = 17 / 2160 = 0.0079
Cycle time Vs. Takt time
Takt time is the maximum acceptable time that meets customer demand. In contrast, Cycle time is the amount of time taken to complete a specific task from start to finish. Cycle time is a work process based, whereas Takt time is based on customer demand.
- If Cycle time < Takt time – Producing more than customer demand. In other words, Overproduction.
- If Cycle time > Takt time – Not meeting the customer demand. In other words, Customer demand fails.
Workload Balancing
Workload compares Takt time (rate of customer demand) to cycle time (“touch time” – or process time). The workload chart plots the cycle time of each process step and the Takt time. If the cycle time of each process is less than the Takt time, then the process may be capable of meeting the customer demand. On the other hand, if any of the process Cycle time exceeds the Takt time, that particular step is incapable and we call it a bottleneck. In such instances, the team needs to distribute the work to the other steps or increase the manpower as necessary. Especially workload balancing helps to improve the productivity and efficiency of the process.
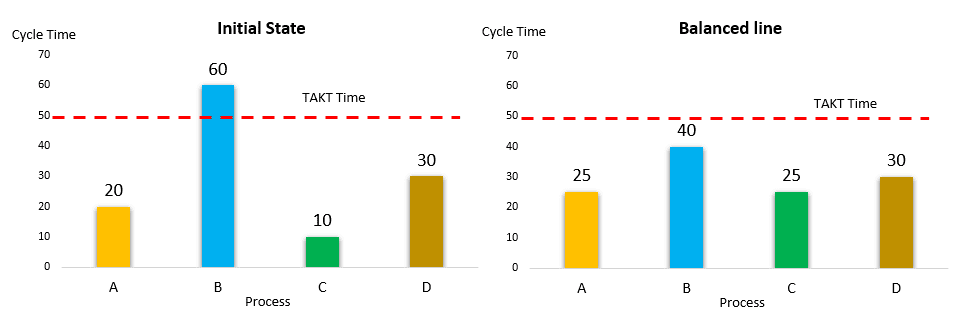
Benefits
- Easily managed production process
- Optimizing the workforce
- Maintaining a constant production workflow
- Optimizing machine utilization
- Eliminate waste and efficiently manage inventory
Helpful Videos
ASQ Black Belt Questions
Question: Which of the following is an element of standard work?
(A) Takt time
(B) Product cost
(C) Product Value
(D) Maximum inventory
Answer:
A: Takt time. By definition, it is an element of standard work. Cost, value, and inventory are all also byproducts of work.
Comments (14)
Wonderful clear easy explanations and examples. Thank you
Welcome, Reema!
You examples are complete shit!!
Well, Gary, tell me how you really feel! ;’)
What’s a benchmark of a great example?
The First Example:
810 minutes / 300 pieces = 2.7 pieces per minute.
I think it should be 2.7 mins per piece?
Good catch, Ali! Updated.
Hello,
In example 5: “The factory operates two 8.5 hour shifts, with 30 minutes of break timer per shift. ” When we calculate net available time, I think we need to deduct break time from each shift 8.5 hours, so:
Net available time = 8.5 + 8.5 – .5 – .5 = 16 hours per day
Is there anything wrong with my calculation?
Thanks in advance.
You’re correct, Quinn. The signs should be flipped for the half hour break times. And the entire equation changes as a result! Thank you for pointing this out!!
If you subtract out the break time, then you are going against the instructions for how to calculate Net Avail time, which says you do NOT deduct break time. This is stated at the beginning of this section and it says that NET AVAILABLE time includes planned downtime which are breaks but not changeovers. see above. thanks Ted.
Calculating Takt Time
Step 1: Calculate the Net Available time
Includes planned downtime
Ex. Breaks, lunches, clean-up time, teem meetings, TPM
Does not include
Material outages, breakdowns, member lateness, changeovers.
Great catch, Barbara. Thank you!
does the answer for takt time changes if there are say 15 workers available for the day? is takt time independent of operators or not?
Takt time is calculated off of net available time. If additional operators do increase your capacity but don’t end up giving your process more net available time. Takt time would NOT change.
@Gary, I think the frustration comes with the wording of example 5,
Initially the article is not clear on the relationship between Kanban cards and Takt rate, so an answer in Takt rate is a little confusing when asking for number of Kanban cards to issue.
There are also few comprehension assumptions made:
“container capacity” and safety stock need continual generation, and as such need to be included in the takt time , I am therefore assuming these form holistic look at efficiency loss in the conversion process. This isn’t crystal clear from the question wording, and with the un required info around MLT being included its easily overlooked.
Keen to understand if this is a direct exam question and will help build comprehension of the system summations used in the exam.
Hi Jonathan,
Thank you for the reply to Gary and for providing me actionable notes I can use to improve the article!
As to your question if this is an actual exam question, that’s been lost to time, I’m afraid. It is specific in it’s wording, so it’s likely one of the thousands of questions viewers of the website send me annually.
Best, Ted