A Root Cause Analysis (RCA) is a problem-solving method to identify the root causes of faults or problems. A factor is considered a root cause if removal from the problem-fault sequence prevents the final undesirable event from recurring. Short-term actions are not profitable for the organization; thus, RCA helps permanently eliminate the issues.
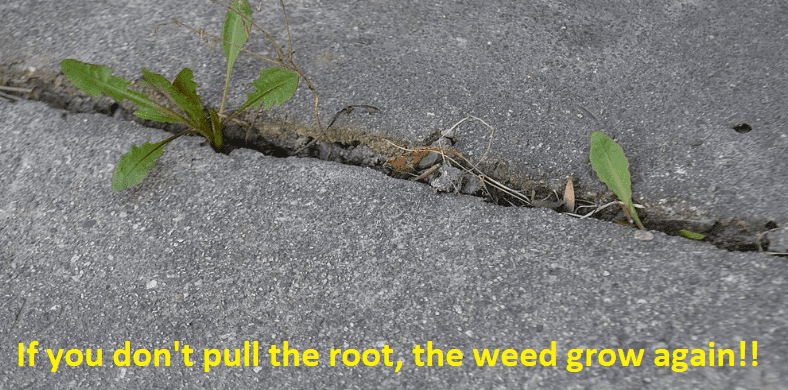
Root cause analysis is a collection of tools and processes we can use to determine the most critical causes for an issue we are trying to resolve. This is an essential function as one of the top 5 reasons for project failures is poor root causation / no root cause identified. If we can determine the root cause of an issue, we have a good chance of solving it.
“Take away the cause, and the effect ceases.” – Miguel De Cervantes in Don Quixote.
Why Root Cause Analysis?
In a process, unpredicted problems may occur at any time, which leads to machine downtime, rework, rejections, or customer dissatisfaction. Fixing a process quickly becomes a convenient solution. However, it does not prevent the problem’s re-emergence. Hence, teams should focus on finding the root cause using appropriate tools to develop a more effective strategy to overcome it.
When should we conduct Root Cause Analysis?
The RCA process involves data collection, analysis, root cause identification, initiating corrective actions, and implementation. You should perform a root cause analysis to determine what happened, why the issue occurred, and what action to implement to reduce or eliminate it. RCA is used to identify issues in the process and analyze customer complaints, reasons for high rework, machine downtime, etc. Moreover, it helps identify target opportunities for systemwide improvement.
Basics of Root Cause Analysis
Before using the aforementioned tools, it is good to start with Causal Theory. In other words, why does a specific problem exist?
To do this, we start with a basic equation: Y = f(x) ;
- Y is the output of a process.
- Xs are the process elements that influence Y.
Another way to state this is Y is the crime; Xs are the suspects that explain the crime of Y.
Data door & Process door
Some of my instructors refer to the data door and the process door. Both are good for root causation, but specific tools are better in certain circumstances.
- Effectiveness project – use data door.
- Efficiency project – use process door.
Root Cause Analysis: Open-Narrow-Close
To validate the root causes identified in the Open-Narrow-Close efforts, the team should employ three tools/techniques:
- Basic data collection: In the DMAIC methodology, a data collection plan is created during the Measure phase. It is a useful tool to focus your data collection efforts on.
- Scatter Analysis/Regression: Linear regression is a statistical technique to estimate the mathematical relationship between dependent and independent variables. In other words, predict the change in the dependent variable according to the change in the independent variable.
- Design of Experiments: The objective of Design of Experiments (DOE) is to Establish optimal process performance by finding the correct settings for key process input variables. Furthermore, the Design of Experiments is a way to intelligently form frameworks to decide which course of action you might take. This is helpful when trying to sort out what factors impact a process.
Open phase
You want to gather as many ideas as possible in the open phase. To do that, first, you use the Brainstorming method. This method generates a large number of creative ideas in a short period of time. Later in the project, you can boil or funnel these ideas to a smaller list of priority items.
The team then pairs the ideas with a Fishbone or cause-and-effect diagram. It is one of the seven basic quality tools identifying many possible causes for an effect or problem. Effective brainstorming can use a Fishbone diagram to achieve stellar results. It sorts ideas into useful categories.
Narrow Phase
After brainstorming, you can use the Fishbone or Cause and Effect Diagram or another expansion tool to generate many possibilities. Then, the group must decide how to narrow down the list.
Multivoting allows a group to narrow a list of choices down to a manageable few. While multi-voting is NOT a decision-making tool, it is a great way to achieve consensus on the option the group favors most.
Close Phase
Once the agreed actions are implemented, the team closes the process by validating using a hypothesis and convicting them or setting them free. During the IMPROVE phase, the team will work on the validated Xs.
Types of Root Cause Analysis Tools
You perform a Root Cause Analysis (RCA) using various statistical tools. However, no fixed rule exists for applying certain tools. Hence, subject matter experts like the Quality team or the Six Sigma champion determine the appropriate tool based on the scenario.
- Brainstorming: Brainstorming is a method for generating a large number of creative ideas in a short period of time. It is energetic, moves rapidly, and is synergistic. Brainstorming creates a large list of ideas that may eventually be converted into a smaller list of priority items later in the project.
- Fishbone Diagram: A Cause and Effect Diagram (aka Ishikawa, Fishbone) is a pictorial diagram showing possible causes (process inputs) for a given effect (process outputs). In other words, it is a visual representation to determine the cause(s) of a specific problem.
- 5 Whys: The 5 Whys is a basic root cause analysis technique; to solve a problem, we need to identify the root cause and then eliminate it. The 5 Whys method asks the question “Why” enough times–until all the problem symptoms have been narrowed down to the root cause (not just till 5 whys).
- Pareto and data analysis: The Pareto Chart is a graphical tool to map and grade business process problems from the most recurrent to the least frequent. In other words, this helps to identify the most frequently occurring problems or separate the vital few from the trivial many.
- FMEA: Failure Mode Effects Analysis (FMEA) is a tool for anticipating problems with a product or process and identifying possible causes and probabilities of failure.
Steps to Perform a Root Cause Analysis
- Form a small team (consisting of members from the process area, subject matter experts, and the Quality team) to perform a root cause analysis.
- Define the problem and describe it in clear and comprehensive language.
- Collect the data and create a timeline to visualize the events’ sequence.
- Differentiate causal factors or symptoms and the root cause of the problem.
- Use tools such as 5Why or Fishbone to systematically identify the root cause of the problem.
- Prioritize the root cause that needs to be addressed first, which greatly impacts the process.
- Implement appropriate corrective action(s) to prevent the recurrence of the same issue in the future.
- Monitor the progress and communicate with relevant stakeholders
Root Cause Example in DMAIC Project
Example 1: A female operator from XYZ organization fell in the assembly area and was injured during the second shift. Perform the root cause analysis to prevent the issue from recurring.
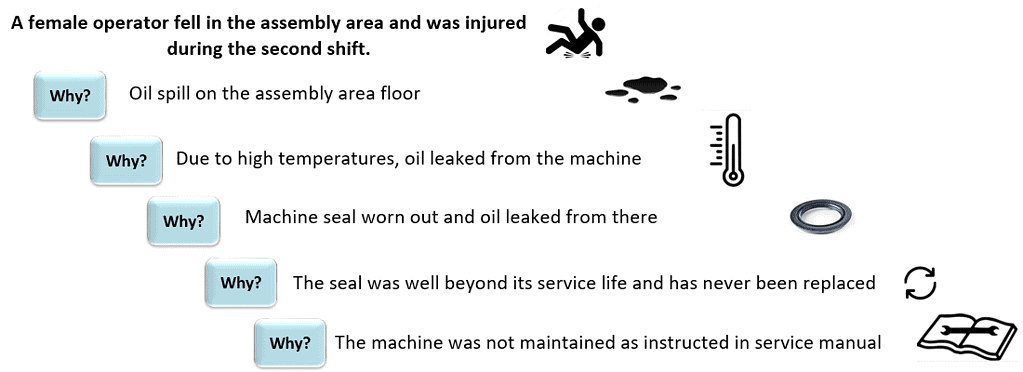
Example 2: XYZ organization reported most of the service complaints are due to inaccurate seal diameter (out of specification).
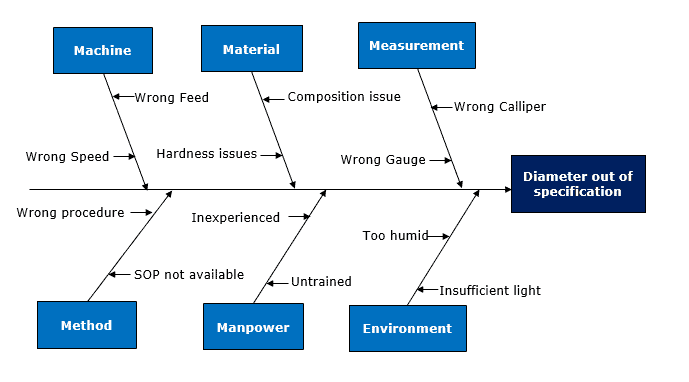
Benefits
- Root cause analysis helps to define the problem and identify the root cause(s) of the problem.
- Help to identify improvement opportunities in the organization.
- Provides confidence to the customers that organizations are valuing the feedback and analyzing systematically to identify root causes
- Root cause analysis helps to implement mistake-proofing solutions
- It helps to implement preventive actions across the organization.
Root Cause Analysis Videos
It’s a good video with awful sound. I muted it and just clicked through at a good pace. It gets the point across.
Other Helpful Notes
Also, see Linear Regression for Y = f(x)
When you’re ready, there are a few ways I can help:
First, join 30,000+ other Six Sigma professionals by subscribing to my email newsletter. A short read every Monday to start your work week off correctly. Always free.
—
If you’re looking to pass your Six Sigma Green Belt or Black Belt exams, I’d recommend starting with my affordable study guide:
1)→ 🟢Pass Your Six Sigma Green Belt
2)→ ⚫Pass Your Six Sigma Black Belt
You’ve spent so much effort learning Lean Six Sigma. Why leave passing your certification exam up to chance? This comprehensive study guide offers 1,000+ exam-like questions for Green Belts (2,000+ for Black Belts) with full answer walkthroughs, access to instructors, detailed study material, and more.
Comments (10)
Root cause can also be calculated from 4M aka Fishbone diagram
Absolutely right, Srijit. Thank you.
For a failure there may be so many causes -but the cause or causes identified for the current failure is called the root cause .
Corrective action to be taken in such a way that will not occurring again ie avoiding recurrence.
Preventive action is the one what we take before the occurrence of that event ie avoiding occurrence.
Great points, T. Thank you for contributing.
My Question is when to initiate a root cause analysis and when to find causes through application of six sigma ?
Hi Fahed,
In Six Sigma you generally follow the DMAIC paradigm – Define, Measure, Analyze, Improve, and Control.
You would do root cause analysis in the Analyze phase.
Does that help?
Best, Ted.
Great post! I completely agree with your points on the importance of identifying and addressing the root cause of problems in order to effectively resolve them. It’s so easy to jump to solutions without properly understanding the underlying issues, but doing so can often lead to inefficiencies and wasted resources. I’ve seen firsthand how a thorough root cause analysis can prevent similar problems from occurring in the future, saving time and money in the long run. Thank you for sharing your insights!
Thank you for the warm comments.
when was this published, i need to reference it
Hey, Sakshi – I first published this page on April 17th, 2014.