Improve phase is the fourth phase of DMAIC. The main activity in the Improve phase is determining the solutions for the problems identified in the first three phases of DMAIC. In other words, during this phase, teams focus on eliminating the root causes and implementing the improvements. Additionally, the team designs the action plan to monitor continuous improvements.
Since Six Sigma teams armed with the data analysis completed in the Analysis Phase of DMAIC can now make informed decisions to develop a solution. Also, best practices include running a pilot to ensure success and validate the conclusions.
Six Sigma Phases
Six Sigma is a systematic problem-solving approach centered around defect elimination and variation reduction, which leads to process improvement.
One of the principal tools in Six Sigma is using the DMAIC methodology. (Also see DMAIC Overview). DMAIC is a logical framework that helps you think through a process and plan improvements to achieve a Six Sigma level of excellence.
There are five phases that are used in the DMAIC method.
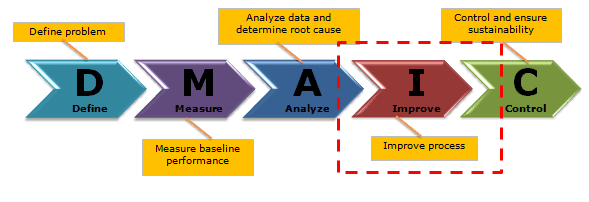
The main purpose of the Improve phase is to identify various solutions using brainstorming techniques and also to apply the affinity diagram to generate and select solutions. First, use clarification, duplication, categorization, and multi-voting to choose a set of solutions. Then, apply must and want criteria to prioritize the order of those solutions to be implemented.
Improve phase of DMAIC Goals.
- Identify the feasible solutions for the identified root cause(s)
- Select the best solution using statistical tools
- Perform cost-benefit analysis
- Test the solution
- Assess the effectiveness of the solution to ensure measurable improvements in the process.
Improve Phase of DMAIC Overview
The improvement phase is approximately an 8 to 10-week process based on resource availability for implementing the solution. In particular, top management support is vital in providing the budget and resources for implementing solutions.
The improvement phase is all about identifying and prioritizing the list of improvements. In other words, building an implementation plan, implementing a pilot project, and analyzing the effectiveness of the implemented solution. Multiple tools and concepts are available in the Improve phase of Six Sigma.
Identify Solutions
In general, the Improve phase focuses on solutions identified by Six Sigma teams to overcome the impact of the root cause(s) or through data analysis.
- Brainstorming: Brainstorming is a method for generating a large number of creative ideas in a short period of time. It is energetic, moves rapidly, and is synergistic. Brainstorming creates a large list of ideas that may eventually be boiled down or funneled down to a smaller list of priority items later in the project.
- Affinity Diagram: An Affinity Diagram is a good technique for identifying & displaying potential root causes for unfamiliar problems.
- Poka-Yoke: Poka-Yoke is the act of error-proofing a process through great design. Defining requirements or ensuring continuous flow are good things but not strictly part of error-proofing.
- 5S: 5S derives its name from five Japanese terms beginning with the “s” utilized to create a workplace suited for visual control and also lean production. 5S are
- Sort
- Straighten
- Shine
- Standardize
- Sustain
- Takt Time: Takt time is used to synchronize the pace of production with the pace of sales. In fact, it is a sort of just-in-time production measure that helps remove and avoid waste.
- TRIZ: TRIZ helps Six Sigma practitioners innovate by exploring solutions outside the boundaries of the process itself. Use this when typical Six Sigma practices don’t adequately address the problem.
Lean
- Lean: The goal of a lean organization is to create and continuously enhance customer value, especially by mitigating waste from its processes and procedures.
- Kanban: Kanban is a popular method for managing tasks in Lean and Agile environments. It can be used at all levels, from individuals to teams and entire companies.
- Cellular Manufacturing: Cellular Systems is a kind of Lean approach that seeks to achieve efficiencies by leveraging the similarities between production units.
- Quick Changeover: Single Minute Exchange of Die (SMED) is a process used to reduce waste.
- Visual Workplace: The visual factory is a Lean concept that offers many benefits to Six Sigma. We especially use it to communicate information quickly and easily.
- Kaizen: Kaizen means continuous improvement. In fact, this concept originated in Japan. Kai means change, and zen means for good.
Proposed Solution
Once the team identifies various solutions, it’s time to finalize the best feasible solution. So, identify potential solution relationships concerning cost, resource availability, and implementation time.
- Failure Mode and Effects Analysis (FMEA): Failure Mode Effects Analysis (FMEA) is a tool that helps us anticipate what might go wrong with a product or process. We can also use it to identify the possible causes and probabilities of failures.
- Cost-benefit analysis involves examining a project’s projected costs and returns. It also provides the data needed to decide whether a project is worth pursuing.
- Matrix Diagram: A matrix diagram is a project management tool that assists in investigating relationships. Further, these are the different types of Matrix diagrams:
- L-Shaped
- X-Shaped
- Y-Shaped
Organizing the Project / Process Completion
- Process Decision Program Charts (PDPC): A Process Decision Program Chart (PDPC) has two main uses: document steps to complete a process and impact analysis.
- Tree Diagram: A tree diagram helps you break down big concepts into progressively greater details. Furthermore, the idea here is to break down a concept into its constituent pieces systematically.
- Activity Network Diagram: The primary intent of creating an Activity Network Diagram is to create a flow chart showing the necessary tasks for a project in sequence order (Both parallel and serial paths).
- Prioritization Matrix: A prioritization matrix can help you determine and negotiate project priorities. It can also be used to prioritize projects themselves, although opinions are mixed on whether this is a good idea.
Pilot plan
A Pilot plan is an experimental or preliminary trial or test of your solution on a limited scale. In fact, a pilot plan is the best way to make sure your pilot run is successful.
Documentation & results
- Collect and Evaluate Pilot Results.
- Analyze the gaps between the predicted performance and the actual performance.
- Use a Root Cause Analysis to find the gaps and to determine why and if solution changes are needed.
- Analyze the pilot plan. What worked? What didn’t?
- Communicate Pilot Results
- Create a summary of the strategy used to pilot the solution and communicate the results to the stakeholders.
- Change management is a key part of project success. Soliciting feedback during stakeholder interviews gives you access to thoughts from those impacted by the project.
- Finally, review the original stakeholder analysis to determine how/if anything has changed and what you may want to do to address those results.
Implementation Plan
Implementation Plan: Successful implementation of a Six Sigma initiative requires thorough planning to ensure success. There are five categories the project owner needs to consider to achieve a fool-proof plan.
- The Work Plan
- Resource Plan
- Stakeholder Management Plan
- Risk Assessment Plan
- Quality Control Plan
Improve Phase of DMAIC Deliverables
- Identify potential solutions
- Finalize the preferred solution
- Pilot test the solution
- Implement the solution
- Ensure the implemented solution results in eliminating the root cause(s)
Improve Phase of DMAIC Videos
When you’re ready, there are a few ways I can help:
First, join 30,000+ other Six Sigma professionals by subscribing to my email newsletter. A short read every Monday to start your work week off correctly. Always free.
—
If you’re looking to pass your Six Sigma Green Belt or Black Belt exams, I’d recommend starting with my affordable study guide:
1)→ 🟢Pass Your Six Sigma Green Belt
2)→ ⚫Pass Your Six Sigma Black Belt
You’ve spent so much effort learning Lean Six Sigma. Why leave passing your certification exam up to chance? This comprehensive study guide offers 1,000+ exam-like questions for Green Belts (2,000+ for Black Belts) with full answer walkthroughs, access to instructors, detailed study material, and more.
Comments (2)
Do you have other resource/outline or cheat sheet that answers this question?
Thanks
Hi Cheryl,
I moved this comment to the member’s forum area. Please see the ticket here: https://sixsigmastudyguide.com/forums/topic/do-you-have-other-resource-outline-or-cheat-sheet-that-answers-this-question/
Best, Ted.