How is Lean Different from Six Sigma? Lean is the elimination of waste. Six Sigma is about the elimination of variation. Pick the right tool for the right purpose.
The Goals of Lean and Six Sigma
The goal of Six Sigma is to produce output that is consistent and free of defects. Defective output requires re-work, and re-work is waste. Inconsistent output is the result of a flawed process. Six Sigma seeks to identify the flaws, determine their cause, and eliminate them.
Six Sigma DMAIC starts with the view that waste includes defective products. To remove waste, you find the root cause of defects (using statistical methods), then design an improvement (Design for Six Sigma) or replace a fault so that the defects no longer occur.
Using a manufacturing example again, let’s say you have a factory that produces widgets. The widgets should all be a certain size, shape, and weight. In your sample output, you discover that fifty out of 1,000 widgets are flawed (e.g., wrong size, shape, or weight). To correct this, you could use Six Sigma to determine what’s causing the variation/defects. Then, you could work to reduce them to a Six Sigma level.
The goal of Lean, on the other hand, must begin with the view that the product and process that creates it must add value to the customer. Anything that does not directly add value to the customer is a waste. It further defines the common wastes and how to eliminate them.
Lean vs. Six Sigma
While it may be desirable to use both Lean and Six Sigma, they are separate issues. An operation can be Lean and still have an unacceptable level of variation in the output. It can also have the variation under control and not be Lean. The two are complimentary, but neither is dependent on the other.
Important Videos
How Lean, Six Sigma, and Design Can All Coexist
The Difference Between Lean and Six Sigma
While Lean encourages daily, general improvements, Six Sigma demands data-based, specific improvements for specific projects.
Lean doesn’t require a hierarchical structure of qualified “masters” to implement the changes. Every individual employee, regardless of their roles in the business, is encouraged to participate in actively improving the manufacturing process.
Six Sigma requires a hierarchical structure of various experts with various belts. These belts signify their level of experience and knowledge in the Six Sigma way.
With the Lean approach, you can walk into your factory today, instruct everyone on what to look for, and give them methods for applying changes they see fit.
With Six Sigma, you’ll have to hire a certified expert to assemble a team, identify a problem, and direct that team until the problem is solved.
In Lean, you let everyone test and experiment to see what works and what doesn’t – a bottom-up approach.
In Six Sigma, you let the qualified professional leading the team decide when you’ve completed the project – a top-down approach.
Which to do first? Lean or Six Sigma?
Undoubtedly, you should do Six Sigma before Lean.
Why, you ask? Because Lean is about creating an efficient process, and Six Sigma is about making the process deliver what the customer wants with little variation. You don’t want to do Lean first because you could make a perfectly-efficient process that delivers something that the customer doesn’t want. If something doesn’t need to be done in the first place, there is no point in doing it well.
If you do Six Sigma first, you’ll have a process that can reliably produce the output that the client wants. Then, use Lean to make that process very efficient and productive.
In other words, use Six Sigma when your process has a lot of variation or doesn’t always perform how the client wants it to. Use Lean when your process already delivers what the customer wants, but the process itself needs to be more efficient or more productive.
Both are tools, philosophies, and management systems, but they are geared toward different ends.
It is possible that both processes could use the same or similar tools and end up with the same improvements.
Note that in the real world, some management teams are more focused on efficiency and productivity than customer satisfaction, and in those cases, Lean is the best choice. Also, it is sometimes helpful to do quick Lean activities, so you can show improvements quickly (whether or not the customer cares about them) to build credibility to do the longer Six Sigma projects.
Integration of Design, Lean and Six Sigma
Six Sigma: Six Sigma is a data-driven approach for reducing process variation and defects. It uses the DMAIC (Define, Measure, Analyze, Improve, Control) methodology to identify, measure, analyze, improve, and control processes. Six Sigma reduces the variation in the process and builds repeatability by following a problem-solving approach using statistical tools. Reduction in variation increases quality, throughput, and overall outcome while cutting costs.
Lean: Lean eliminates waste, decreases wait time and creates value across all areas of business. It uses tools like Value Stream Mapping, 5S, and Just-In-Time to identify and eliminate non-value-added activities.
DFSS: Design for Six Sigma (DFSS) is a proactive approach that prioritizes the creation of products, processes, and services that align with customer needs and minimize defects. DFSS eliminates the need for costly trial and error in the design process, as it incorporates customer requirements directly into the initial product design phase.
Lean-Six Sigma Integration
Often organizations practice Lean Six Sigma, which combines Lean’s focus on efficiency with Six Sigma’s emphasis on quality. This integration aims to reduce waste while also improving process quality by using the DMAIC methodology.
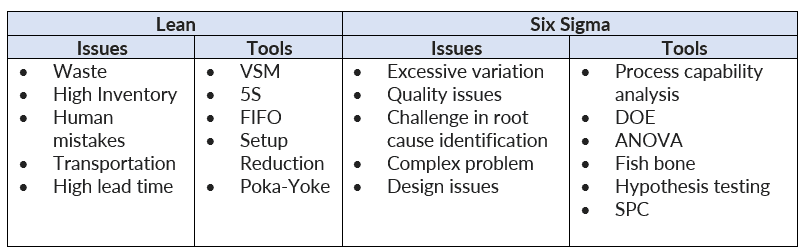
Many organizations recognize that they have a combination of both sets of issues. The two methods complement each other working together to identify errors and waste more efficiently than using just one method. Lean Six Sigma helps organizations in any industry increase revenue, reduce cost, and improve collaboration in today’s competitive world.
Both Six Sigma and Lean coexist in any organization. Lean accelerates Six Sigma. Lean provides stability and repeatability, which helps Six Sigma collect the data more accurately. Therefore, many organizations implement both methodologies into an integrated system or improvement roadmap.
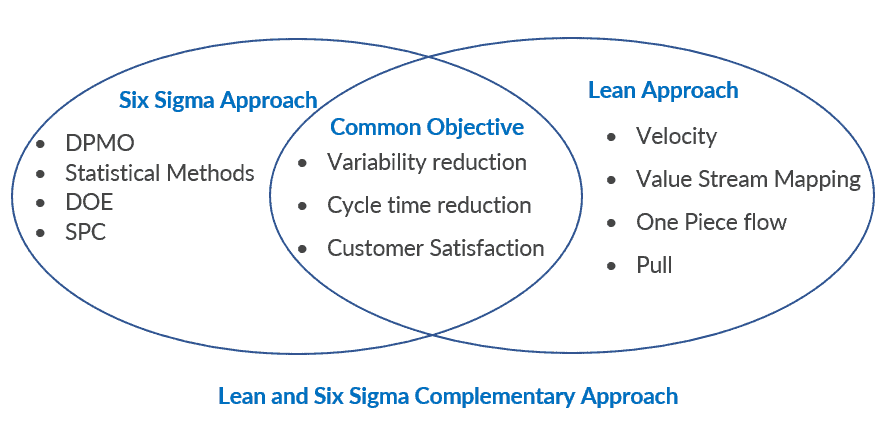
Problem identification, problem-solving tools, and techniques are common in both Six Sigma and Lean methodologies. Such as the Pareto chart, FMEA, Why-Why, Fishbone diagram, etc. The extensive set of these tools increases the speed and effectiveness of the process.
Although both Six Sigma and lean management are cutting-edge methodologies, each system places emphasis on specific aspects of organizational performance. Consequently, in a highly competitive environment, implementing either program in isolation may lead to diminishing returns.
Design Integration with Lean and Six Sigma
When designing new processes or products, organizations can integrate DFSS principles with Lean and Six Sigma. This ensures that from the outset, the process or product is designed to meet customer needs, minimize waste, and reduce defects. Tools like QFD and FMEA can be used to identify critical customer requirements and potential failure modes, while Lean principles can be employed to eliminate waste and streamline processes.
Tools Used by Both Six Sigma and Lean
In both cases, process mapping and value stream mapping are essential. If you cannot define your process, how can you possibly know what is wasteful or what is variation? Once you have defined your process via a process map you can use value stream analysis to determine where the waste is.
When you’re ready, there are a few ways I can help:
First, join 30,000+ other Six Sigma professionals by subscribing to my email newsletter. A short read every Monday to start your work week off correctly. Always free.
—
If you’re looking to pass your Six Sigma Green Belt or Black Belt exams, I’d recommend starting with my affordable study guide:
1)→ 🟢Pass Your Six Sigma Green Belt
2)→ ⚫Pass Your Six Sigma Black Belt
You’ve spent so much effort learning Lean Six Sigma. Why leave passing your certification exam up to chance? This comprehensive study guide offers 1,000+ exam-like questions for Green Belts (2,000+ for Black Belts) with full answer walkthroughs, access to instructors, detailed study material, and more.
Comments (15)
Author does not understand lean. Beginning with 6sigma regularly creates an enormous amout of waste, frustrates employees….especially those who know the customer best.
If this was part of 6Sigma for Dummies it explains a lot. Thoroughly understand lean….read ‘The Goal’ and Six Sigma before moving forward with your six sigma squads. Terrible, terrible advice you’re giving.
Interesting opinion, Bernard. Do you have any data to back up your thoughts? A case study, perhaps?
When I read the article above, I also disagreed with the comment do 6sigma before lean. This was because I recalled a situation where we flow-charted a process, and ended up removing a whole sub-process that was being delivered due to historical inertia. – we have always done that because that is what they need!
Had we spent time controlling the sub-process first, that would have been wasted effort. I would have thought that the first step should always be to determine what the customer supplier chain should be delivering, and then ensure that it is being controlled.
This was under TQM though, and i have just started to look at Lean and 6sigma, so i may be missing the actual application here.
Great site though.
Hi Ian, Good points. I think you and I are coming from a similar perspective.
Let’s assume the process is delivering something that is wanted by the customer. And beyond that, there are quality standards meaning that something could be wanted and created badly.
If you have poor quality (or a lot of variation in quality), my logic is that you want to get that under control first. If you speed up the cycle time using lean, you just get even more defects – just quicker.
Writing this reply, I could envision scenarios where you might do lean first or even in conjunction with Six Sigma – so my article above may come across more absolute than I had meant it to be.
I think it all comes down to a cost of poor quality analysis at the start of the project. If your process has stability and great quality, then go ahead and lean it out – the ROI will likely justify it. However, if you have poor quality, the ROI of Lean is likely less than stabilizing the process and improving the quality.
And again, I mention ideal scenario. Any practitioner of any quality system (Lean, Six Sigma, TQM, etc) has been exposed to the reality of needing to achieve a “win” quickly in order to keep the program going.
I agree with Ted. A business’ sole purpose is to create value for an end user. The Six Sigma approach emphasizes the need to create and build value for the customer, thus maintaining and growing the business.
Lean is still very important, but if you implement Lean without fully recognizing what is creating value for the customer, the profits gained from Lean will only last as long as value is provided to the customer.
Sometimes people have different understanding about lean as lean is actually an explanation of Toyota Production System, so discussion related to lean might not be easy.
I think lean (or Toyota Production System) can be worked alone very well without six sigma, actually both methodology emphasis customer value, so there is no answer for which one should go first, it actually depends on what kind of problem that your company is facing.
You’re absolutely right that Lean and the Toyota Production System (TPS) are closely intertwined. Lean, after all, is essentially the Western interpretation of TPS, focused on eliminating waste, improving flow, and maximizing customer value. Because of its roots, Lean carries a strong cultural and operational legacy from Toyota, and that can lead to differing interpretations and implementations across industries and geographies.
It’s also insightful to note that Lean can operate effectively as a standalone methodology. Many organizations have adopted Lean to streamline processes and reduce waste, achieving remarkable gains in efficiency and responsiveness without initially incorporating Six Sigma. Likewise, Six Sigma can function independently to reduce variation and improve quality through data-driven decision-making.
As you pointed out, the choice between Lean and Six Sigma often depends on the nature of the problems a company is facing. If the issue is process waste and inefficiency, Lean might be the better starting point. If the challenge is process variability or defect reduction, Six Sigma may offer more powerful tools. Many companies, however, find that combining the strengths of both—into Lean Six Sigma—offers a more comprehensive and effective improvement strategy.
If you’re interested in exploring how Lean and Six Sigma can complement each other, or in building a robust understanding of Six Sigma fundamentals, you might find our courses useful:
Thanks again for sharing your thoughts—these kinds of discussions are vital for deepening our collective understanding of continuous improvement methodologies.
Hi! A few questions:
– Is it necessary to implement the six sigma methodology if a company is already fully-optimized as a lean organization?
– Is it necessary to implement the lean methodology if a company is already fully-optimized as a six sigma organization?
Thanks
Hi Jack,
I don’t see lean and six sigma as mutally exclusive. In other words, you want to choose the right tool for the job.
First question: “s it necessary to implement the six sigma methodology if a company is already fully-optimized as a lean organization?”
Well, nothing is necessary. But if you want to compete, I would think you should. Six Sigma is about executing flawlessly (or as close to it as possible). Lean is about removing waste. If you focus on lean first you run the risk of optimizing processes that shouldn’t even exist in the first place – or that should exist in a fundamentally different way.
Second question: “Is it necessary to implement the lean methodology if a company is already fully-optimized as a six sigma organization?”
This comes back to your KPIs, countermetrics, and goals of your organization. Let’s say you used Six Sigma to reduce error rates in a process. You were also responsible so you made sure the project aligned with company goals on the outset. Also, you established countermetrics to ensure that your changes never made a negative impact to another part of the company. But now that you have a very accurate process you’d like to scale and increase output. One way to do that would be to lean out the process to remove as much waste as possible and increase resource utilization WHILE maintaining the gains Six Sigma gave you.
this makes a lot of sense. I just hope it worded where I can understand what’s being asked during the exam.
Yellow is for existing processes 1,2,3 lead with lean
Blue is new processes 3,2,1 lead with VOC
Moving on…
Understanding test questions is a skill. It’s a specific type of reading comprehension.
Fortunately, this is a skill that can be sharpened by practice!
I got confused between these 2 lines
1=”Lean must begin with the view that the product and process that creates it must add value to the customer”
2=”some management teams are more focused on efficiency and productivity than customer satisfaction, and in those cases Lean is the best choice”
Hi Nabeel,
Thanks for asking. The distinction is really a case of Ideal vs Reality.
In the Ideal state, you would evaluate a tool before using it. Lean requires a focus on the value to the customer and the discipline to trace that value backwards through all process that deliver that value and increasing it. In that case, you would choose lean to eliminate all items that get in the way of value delivery.
However, some management teams pre-select the symptoms they want to address rather than focusing on true end-to-end value. In those cases you’ll hear phrases like “we need to reduce cost” or “we need to improve cycle time” – but without any answers to the why that kind of project is selected ahead / instead of something else. In those cases, use Lean.
All of this is in opposed as to the question of ‘When do you use Six Sigma?” My practical answer to that is “Use Six Sigma when you have a defined process that delivers value to the client which you wish to maximize AND you have no good idea how to accomplish that.”
great information
Glad you found it helpful, Toufic!