Western telecom manufacturing has significantly changed since the dot-com bubble burst, leading to global competition. As a result, success now requires more effort, and the joint strategy of Lean Six Sigma is one way to survive. Here’s a Telecom Lean Six Sigma Case Study to bring this story to life.
Researchers from Jönköping University in Sweden studied the Swedish telecom manufacturing industry. They wanted to see if using Lean Six Sigma together could make the industry more flexible, robust, and cost-efficient.
The research analyzed a Six Sigma project in 2002 and followed its outcome longitudinally until 2014. The study focuses only on large companies with large resources and controls over supply chain operations.
This article explains how to use Six Sigma for a project in a Lean environment. The authors describe their implementation of this method in the following sections.
The Application of Lean Six Sigma In Telecom Manufacturing Case Study
The phone company works on a quality improvement project to make their products better and cheaper to meet customers’ wants.
Ericsson Group carried out the project in a production facility in Borås, Sweden. The researchers examined the assembly and testing procedures of the MINI-LINK manufacturing line. The push system is focused on senior management collaborating with researchers to meet objectives.
The researchers talked to staff, observed, and reviewed documents to get information about their study processes. Finally, the team initiated and implemented the Lean Six Sigma methodology to achieve the project’s goal.
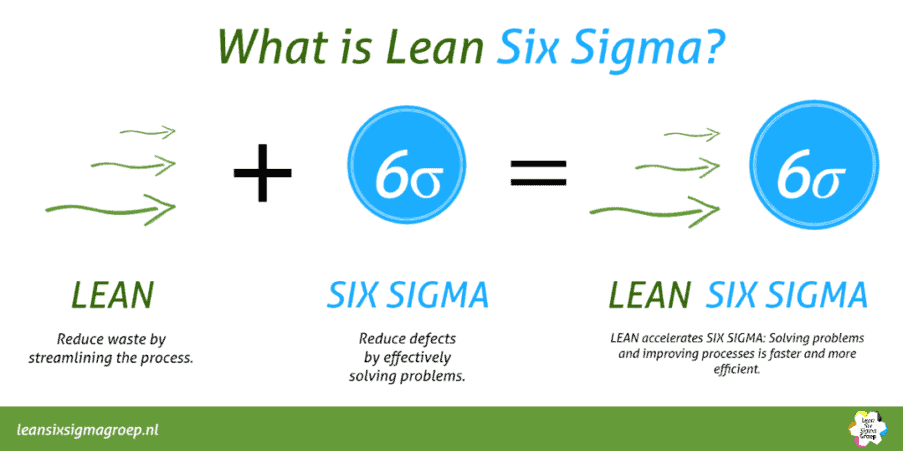
Lean focuses on improving customer value and achieving continuous improvement by taking small steps. This approach is suitable for a variety of manufacturing and distribution scenarios. Lean focuses on critical concepts like understanding customer value, value stream analysis, flow, pull, and perfection.
The researchers used a process improvement method called DMAIC from Six Sigma, which has five phases to reach their goal.
The DMAIC cycle involves:
- Defining the problem
- Measuring the current performance
- Analyzing the process
- Improving the process
- Controlling the new process
Telecom Lean Six Sigma Case Study by DMAIC Phase
Here is how this implementation of the DMAIC cycle focused on saving money variability and achieving the telecom manufacturing company objectives.
Define Phase
The first step is identifying the area that requires improvement and the most suitable team members to execute the project. Defining problems is best achieved with a well-defined vision and a strategic approach to enhance service quality.
During the define phase, the team tried to:
- Identify the project’s area for improvement
- Select the right team.
- Understand customer needs
- Sets SMART goals
- Design a communication strategy,
- Conducts risk analysis
- Create a project chart (This record includes the fundamental aspects of the project and responds to essential queries.)
Each of these is a crucial step in any successful project.
Additionally, researchers identify the stakeholders and capture the voice of customers (VOCs). Customer requirements are divided into Critical to Quality CTQ parameters to focus on key aspects for the team. The team conducted a SIPOC and SWOT analysis to ease project success and break down customer requirements into CTQ parameters.
Measure Phase
During the measure phase, the researchers identified defects in exceptional service. The CTQ chart is a useful Six Sigma tool used at this stage, revealing crucial processes necessary for success. In this phase, team members assess the current processes and avoid making changes.
The team established the baseline performance for the production facility process and collected all data during this phase. Collecting enough data for a reliable project outcome is important while avoiding spending time on unnecessary data.
Analyze Phase
To find the root causes, the researchers analyzed the data measured. They then prioritize the sources to determine which ones require the most urgent action. For example, the assembly analysis revealed only one accurate MINI-LINK assembly out of five with the correct index pair.
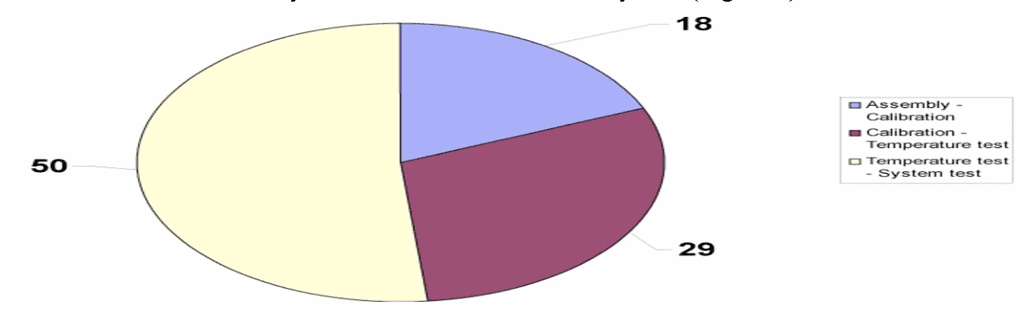
They also perform calibration consistency analysis. The study found that broken parts cause problems and make things less reliable, which means more stuff needs to be stored before they can be fixed.
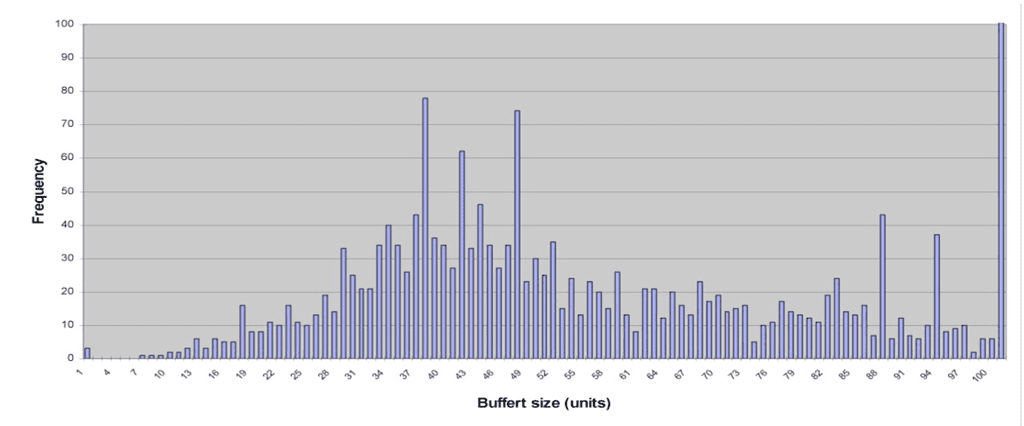
Successive processes increase the disorder further. Cause and Effect Diagrams, frequency plots and graphs, and scatter plots and diagrams are helpful Six Sigma tools.
Improve Phase
After identifying the root cause of the problem, the Improve phase of DMAIC aims to discover a lasting solution. It involves reducing the number of products in the process to expose system problems and lead to further improvement. Besides, implementing specific measures can make the process more robust and flexible. These measures include ceasing picking when the buffer stock exceeds 12 units and requesting assistance when the buffer stock falls below six teams. These steps can lead to additional improvements.
The implementation of these changes resulted in a system that was more reliable, robust, and aligned with an agile approach. In addition, the team made some changes to MINI-LINK’s transportation and staff walking distances. As a result, they could assign some staff to other tasks based on calculated Takt time.
The researchers made some changes that made the system better. It’s now more dependable and strong and can adapt easily using agile principles. Furthermore, there were notable quantitative improvements. Significant reductions were made to refinement time while ensuring delivery precision. The lead time was reduced from 80 to 48 hours or less for 98% of the products. This reduction in lead time was one of the critical objectives of the changes.
Before these changes, the repair process was a critical issue, but waiting time decreased after modifying the routine and flow. In addition, the research showed that values improved over time with the introduction of the last phase of the Lean concept.
Control Phase
This phase is the final step of the DMAIC process. The Control phase involves monitoring things and taking action for any problems.
After finishing the “Improve” step and doing everything the team planned, they saved more than 1 million euros annually. This shows that Six Sigma helps us improve our work, making it more adaptable, tougher, and cheaper.
Ericsson Group worked on building a stronger team by having group activities that helped everyone share the same values. They also had training sessions twice a year and quick meetings between shifts to make the team feel more connected. Additionally, they incorporated the Lean philosophy to achieve sustained improvement. This included implementing a PDCA cycle for continuous improvement, TPM, VMS application thrice daily, visualization routines, and waste reduction.
Telecom companies can save money, make employees happier, and plan better by using these tools. For example, VMS can turn boring data into pictures that are easy to understand, changing the way the company works.
Telecom Lean Six Sigma Case Study Conclusion
Combining Six Sigma and Lean are practical manufacturing tools that complement each other. Lean helps to make work smoother by eliminating things that don’t help. Six Sigma makes sure everything is consistent by finding the cause of problems. This helps to make work better, faster, and cheaper.
To improve things, Lean adds important things like eliminating waste, using visual aids, keeping things in good shape, always trying to get better, and letting people work together. Using Lean Six Sigma, we can ensure work is done well, can change when needed, is strong, and doesn’t cost too much. But, we also need to train people, make sure everyone in the company is working together, and partner with others to make it work even better. These measures will help functions remain agile in changing environments.
When you’re ready, there are a few ways I can help:
First, join 30,000+ other Six Sigma professionals by subscribing to my email newsletter. A short read every Monday to start your work week off correctly. Always free.
—
If you’re looking to pass your Six Sigma Green Belt or Black Belt exams, I’d recommend starting with my affordable study guide:
1)→ 🟢Pass Your Six Sigma Green Belt
2)→ ⚫Pass Your Six Sigma Black Belt
You’ve spent so much effort learning Lean Six Sigma. Why leave passing your certification exam up to chance? This comprehensive study guide offers 1,000+ exam-like questions for Green Belts (2,000+ for Black Belts) with full answer walkthroughs, access to instructors, detailed study material, and more.