Causal theory, in Six Sigma terms, means that you create an output (y) from an input (x) and a function (f). Clear as mud so far? Don’t worry.
It’s made up of three components:
- y: What you get out of a process. In a manufacturing context, this is a physical product.
- x: What you put into a process. In the same manufacturing context, this is a material or part.
- f: What you do to turn x into y. In manufacturing, this is a machining or assembly procedure.
y = f(x) Output = method * input
Using Causal Theory in Six Sigma
When you have a problem with your output (y), causal theory tells you that there are two possible culprits:
- f: Your procedure for creating that output.
- x: The materials or information you’re adding to that procedure.
Using Causal Theory with Multi-Step Processes
Very few processes will be simple enough that you can pinpoint either your procedure or material as the issue and voila, solved! So you’ll often need to break down the causal theory equation:
ytotal = y1 + y2 + y3 + ... + yn
Translation: Your total output from a process is the sum of the output from each sub-process within it.
This means that if you have trouble with your output from a complex process, a good starting point is to break down that process into sub-processes. Then, look at the output from each sub-process. Where does the problem creep in? Once you find the problem sub-process, you can move to figuring out whether your input or procedure is the cause.
Correlation and Causation
It’s important to note that sometimes you’ll run into confusion choosing between correlation and causation. You need to understand the difference and know how to distinguish them.
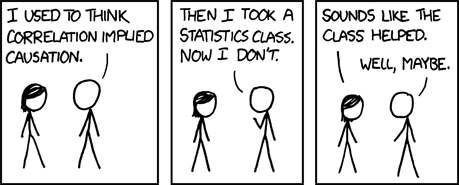
Correlation: A relationship between two events. They occurred at much the same time, in the same population, or in the same circumstances. For example, spilling a glass of milk and dropping an egg. They might occur at the same time, and they might have the same cause – clumsiness or a fright. But one would rarely cause the other to happen.
Causation: A causative relationship between two events; one caused the other to happen. For example, dropping an egg could cause it to land on the floor. These will also happen at almost the same time, by human observation. But unlike the milk-and-egg example, one – dropping an egg – can be shown to directly cause the other – it landing on the floor.
Separate correlation and causation by identifying variables in your procedure (f) or input (x) and, where possible, change only one variable at a time. When you find that changing a makes a difference to the output but changing b doesn’t, you’ve found that a has a causative effect.
Applying Causal Theory to DMAIC
In a practical sense, here’s how you can use causal theory in your DMAIC cycles:
- Define: Look at your outputs (y) and clearly distinguish the issue that you’re facing. For example, the end size of a product is not within acceptable levels of consistency.
- Measure: Measure your inputs (x) and outputs (y). For example, take measurements of product parts at each stage in the process, and check material strength, density, and composition.
- Analyze: Prioritize your outputs (y). Which ones are most contributing to the issue? Test whether issues in your highest-priority sub-processes are caused by the input (x) or the procedures (f). For example, vary material qualities in some tests and the manufacturing sub-procedure in others.
- Improve: Implement strategies to improve your input (x) or procedures (f) for high-priority sub-processes. Do these alleviate the problem? For example, if substandard materials have caused a lot of variation, switch suppliers and temporarily check quality rigorously. Then check that the change in materials has improved the end product.
- Control: Put measures in place to monitor the future inputs (x) and procedures (f). For example, run a weekly spot-check on the new inventory of materials.
Using an Input Map with Causal Theory
You can use an input map to show the inputs (x) and outputs (y) of each procedure (f) in your process. We’ll use a simple process that’s familiar to most of us – a morning breakfast routine. You can use a spreadsheet or a mind-map type diagram to give you a visual representation of your mapping.
1. List your procedures
Look at your process and determine the discrete procedures in place. For example, in a morning breakfast routine, you might have:
- Make a mug of coffee
- Make toast with jam
- Read the news on a tablet
- Have breakfast
- Wash breakfast dishes.
Each procedure will be in the middle of its own input map.
Inputs | Procedure | Outputs |
---|---|---|
Make a mug of coffee | ||
Make toast with jam | ||
Read news on tablet | ||
Have breakfast | ||
Wash breakfast dishes | ||
2. Find your inputs for each procedure
What do you need to complete the procedure? Think about everything that the operator needs to use. For example, ‘make a mug of coffee’ in our breakfast routine might require:
- Coffee machine
- Electricity supply
- Coffee pod
- Mug
- Sugar
- Milk or creamer
- Spoon
Inputs | Procedure | Outputs |
---|---|---|
Coffee machine | Make a mug of coffee | |
Electricity supply | ||
Coffee pod | ||
Mug | ||
Sugar | ||
Milk or creamer | ||
Spoon | ||
Toaster | Make toast with jam | |
Electricity supply | ||
Butter | ||
Jam | ||
Knife | ||
Plate | ||
Tablet with charged battery | Read news on tablet | |
News service | ||
Spectacles | ||
Coffee in mug | Have breakfast | |
Toast on plate | ||
Appetite | ||
Teeth | ||
Hot water | Wash breakfast dishes | |
Dishwashing liquid | ||
Dirty plate | ||
Used mug | ||
Dirty spoon | ||
Dishcloth |
3. Record your outputs for each procedure
Your outputs are what you get out of each procedure. You have two choices here:
- List every single output from the procedure
- List only the output that you’re interested in.
For this example, we’ll only list the output that feeds into other procedures and the end product.
Inputs | Procedure | Outputs |
---|---|---|
Coffee machine | Make a mug of coffee | Mug of hot coffee, to taste |
Electricity supply | ||
Coffee pod | ||
Mug | ||
Sugar | ||
Milk or creamer | ||
Spoon | ||
Toaster | Make toast with jam | Toast with jam on a plate |
Electricity supply | ||
Butter | ||
Jam | ||
Knife | ||
Plate | ||
Tablet with charged battery | Read news on tablet | Entertainment |
News service | ||
Spectacles | ||
Coffee in mug | Have breakfast | Dirty dishes |
Toast on plate | Full stomach | |
Appetite | Feeling of wakefulness | |
Teeth | ||
Hot water | Wash breakfast dishes | Clean plate |
Dishwashing liquid | Clean mug | |
Dirty plate | Clean spoon | |
Used mug | ||
Dirty spoon | ||
Dishcloth |
4. Link inputs to your output of interest
Next, follow the trail backward from your problem output to the input that might be affecting it.
For example, say I’m finding it hard to stay awake at work this morning. Weird – I had breakfast, which always includes coffee. I can follow my input back from the output and highlight the trail.
Inputs | Procedure | Outputs |
---|---|---|
Coffee machine | Make a mug of coffee | Mug of hot coffee, to taste |
Electricity supply | ||
Coffee pod | ||
Mug | ||
Sugar | ||
Milk or creamer | ||
Spoon | ||
Toaster | Make toast with jam | Toast with jam on a plate |
Electricity supply | ||
Butter | ||
Jam | ||
Knife | ||
Plate | ||
Tablet with charged battery | Read news on tablet | Entertainment |
News service | ||
Spectacles | ||
Coffee in mug | Have breakfast | Dirty dishes |
Toast on plate | Full stomach | |
Appetite | Feeling of wakefulness | |
Teeth | ||
Hot water | Wash breakfast dishes | Clean plate |
Dishwashing liquid | Clean mug | |
Dirty plate | Clean spoon | |
Used mug | ||
Dirty spoon | ||
Dishcloth |
Primary procedure
First, I check my main output. Is my stomach full? Yes. So I must have had breakfast. My memory of this morning agrees. Yes, I had breakfast; toast and coffee. That procedure (f) isn’t the problem.
Primary input
Second, I look at the input (x) for my breakfast procedure. The relevant item is the mug of coffee. If there isn’t a problem with f, causal theory tells me, there must be a problem with x.
Secondary procedure
Third, I look at the making coffee procedure. I remember making and drinking my coffee without issues, so procedure (f) would seem to be fine. What about the inputs (x)?
Secondary inputs
Fourth, I look at the coffee procedure inputs. If I made the coffee without issues and it was hot when I drank it, that would tend to rule out issues with the coffee machine or electricity. If I didn’t notice any issues with the taste, that would probably rule out problems with the milk or sugar inputs. I can’t imagine any scenario where the choice of mug or spoon would affect my wakefulness later on, so I rule out those inputs for now. What about the coffee pods? They seem the most likely candidate left.
Further investigation
Fifth, I check the coffee pod input in depth. I find the open box of pods – and ta-da! They’re labeled as decaf. I check the rubbish bin to confirm; the pod from this morning is lying on top, and it’s clearly marked as decaf. I’ve found the source of the problem: one of my inputs (coffee pod) was incorrect. This caused a flow-on issue with the output (mug of coffee) from a sub-process, which was the input in the breakfast procedure. This incorrect input (mug of decaf coffee) caused an issue with the output of the whole process (feeling of wakefulness).
Conclusion
While the above example is a bit farcical, it does give you a simple example of how using causal theory and an input map can help you to track issues in output back to their causes.
Things to remember
Keep these points in mind:
- A problem with your output (y) has two potential sources: your input (x) and your procedure (f).
- These two potential sources are not exclusive. You could have an issue with both your input (x) and your procedure (f).
- Most processes are complex enough that you’ll need to break them down into multiple sub-processes, each with its own input and procedure.
- Prioritize your problem outputs. In other words: focus on the larger problems first. You can fine-tune it later.
- Problems in a sub-process can be replicated and enlarged as its output moves through subsequent sub-processes. Ensure that you drill down to the ultimate source of the issue.
Comments (8)
Great post however I was wanting to know if you could write a
litte more on this subject? I’d be very thankful if you could elaborate a little bit further.
Thanks!
Will do, Santiago. I’ve put it on the queue.
Videos would also be helpful. Reading about functions can be a drag and we tend to zone out.
Yeah, I bet. On my to-improve list! If you find any that resonate with you, please let me know and I’ll embed them.
Looking at 2 factor analysis might give some examples of use?
Thanks, Micheal.
That is a good idea. We’ve started with a more basic treatment here to sink the concept in. What do you think?
THANKS
You’re welcome, Vinay Kumar!