What is Total Quality Management?
Total Quality Management (TQM) is a management style that emphasizes:
- Commitment from everyone in the organization
- Dedication to high quality in every process
- A focus on customer satisfaction
Breaking it down:
- Total (T): Involves the entire organization and every aspect of its operations
- Quality (Q): Consistently meeting or exceeding customer needs and expectations
- Management (M): Empowering everyone to contribute to high-quality outcomes
TQM places a heavy emphasis on continual improvement. We don’t accept the status quo simply because “it’s always worked.” Instead, we actively work to refine and optimize processes.
TQM integrates all functions (planning, sales, marketing, production, technology, design, finance), so that every department contributes to meeting customer expectations and organizational goals.
Quality is everyone’s responsibility—not just the QA team’s.
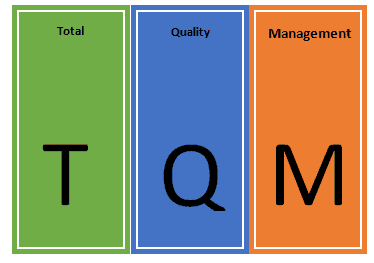
Everyone is responsible for quality control, not just the quality assurance team.
The 8 Principles of TQM
TQM is built around eight core principles that guide improvement efforts and ensure consistent, high-quality outcomes.
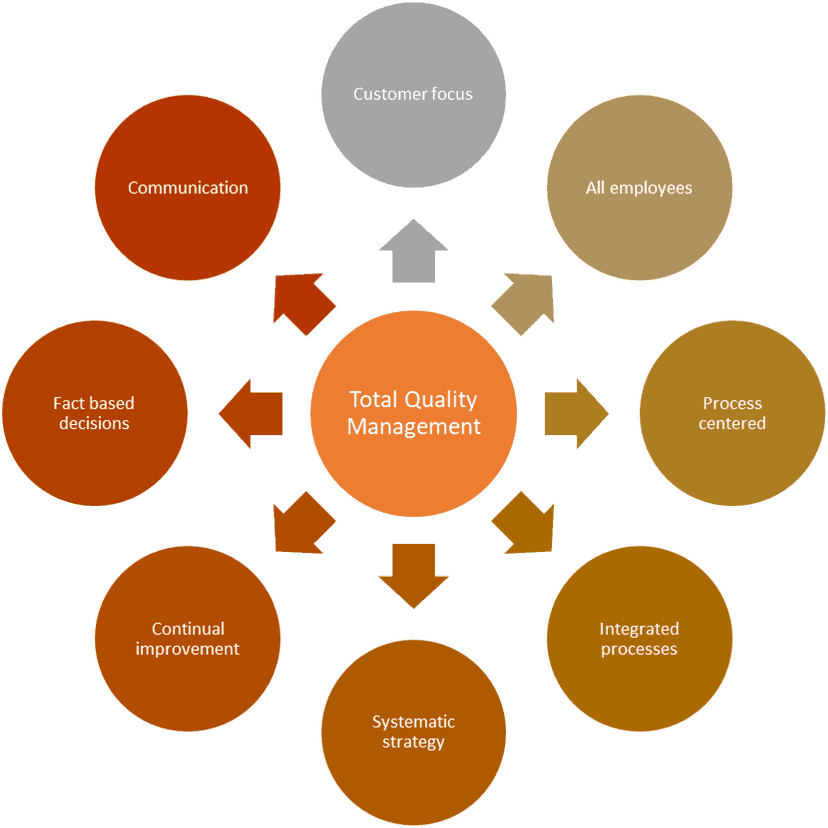
1. Customer Focus
The success of any organization depends on its ability to satisfy customers. Therefore, every improvement should prioritize customer needs and expectations.
2. Total Employee Involvement
Everyone, from senior executives to frontline workers, must be engaged in the quality effort. Full participation helps drive consistent improvement.
3. Process-Centered Thinking
Improving your processes leads to better outputs. Better outputs mean happier customers. That’s why defining, monitoring, and controlling key processes is at the heart of TQM.
4. Integrated System
As organizations grow, departments often develop isolated processes. TQM encourages a unified system of business processes across the company, enabling alignment and consistency.
5. Strategic and Systematic Approach
Implement strategy in a methodical way.
- Begin with a strategic plan focused on quality.
- Then, implement it using a structured system.
Many organizations miss one of these two steps. TQM insists on both.
6. Continual Improvement
Everyone should look for ways to do better. This mindset must be embedded across the organization. The goal? “How can we be better?” not “This is good enough.”
7. Fact-Based Decision Making
Decisions should be based on data not assumptions. Metrics provide measurable insights, allow progress tracking, and justify changes to strategy.
8. Effective Communication
TQM depends on two-way communication:
- Top-down: So employees understand goals, expectations, and strategy
- Bottom-up: So leadership stays informed about challenges, opportunities, and improvements
Don’t rely on chance. Set up clear channels to support consistent communication.
History of Total Quality Management
In the 1930s, Walter Shewhart developed two foundational concepts:
- Statistical analysis.
- Quality control.
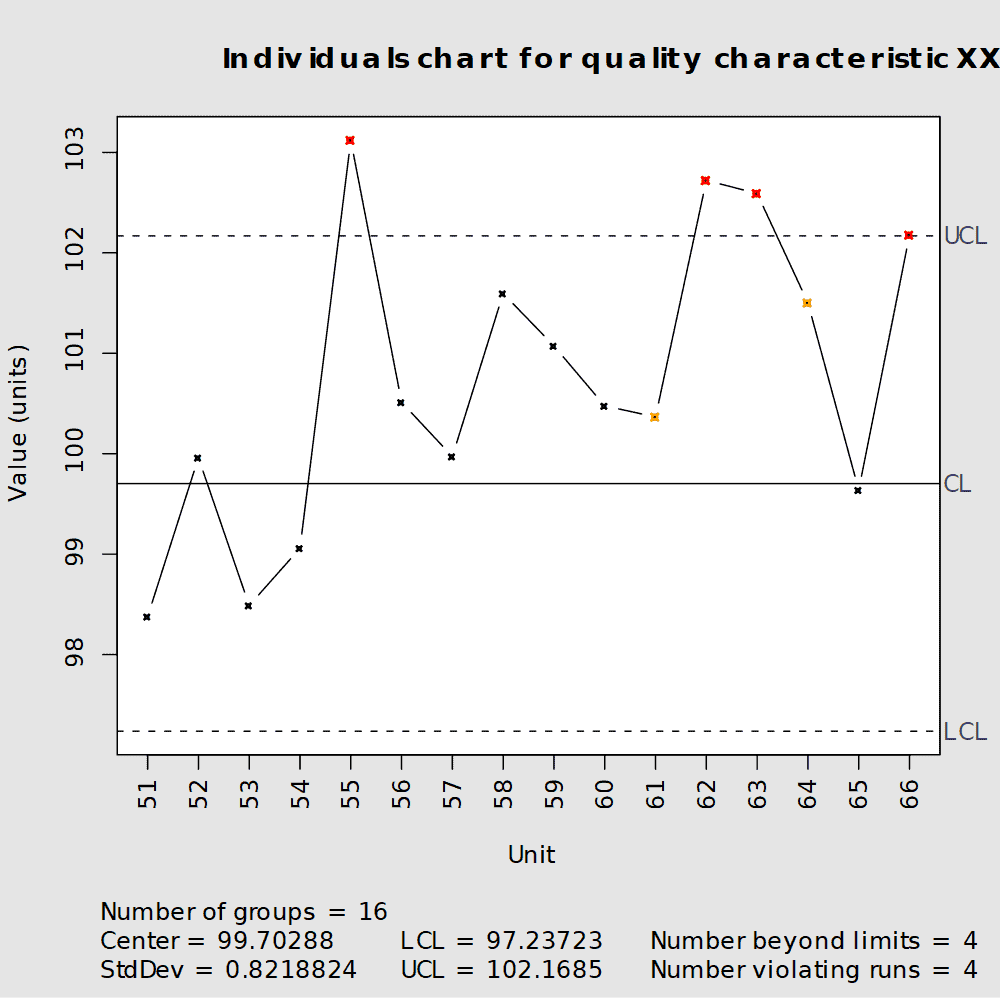
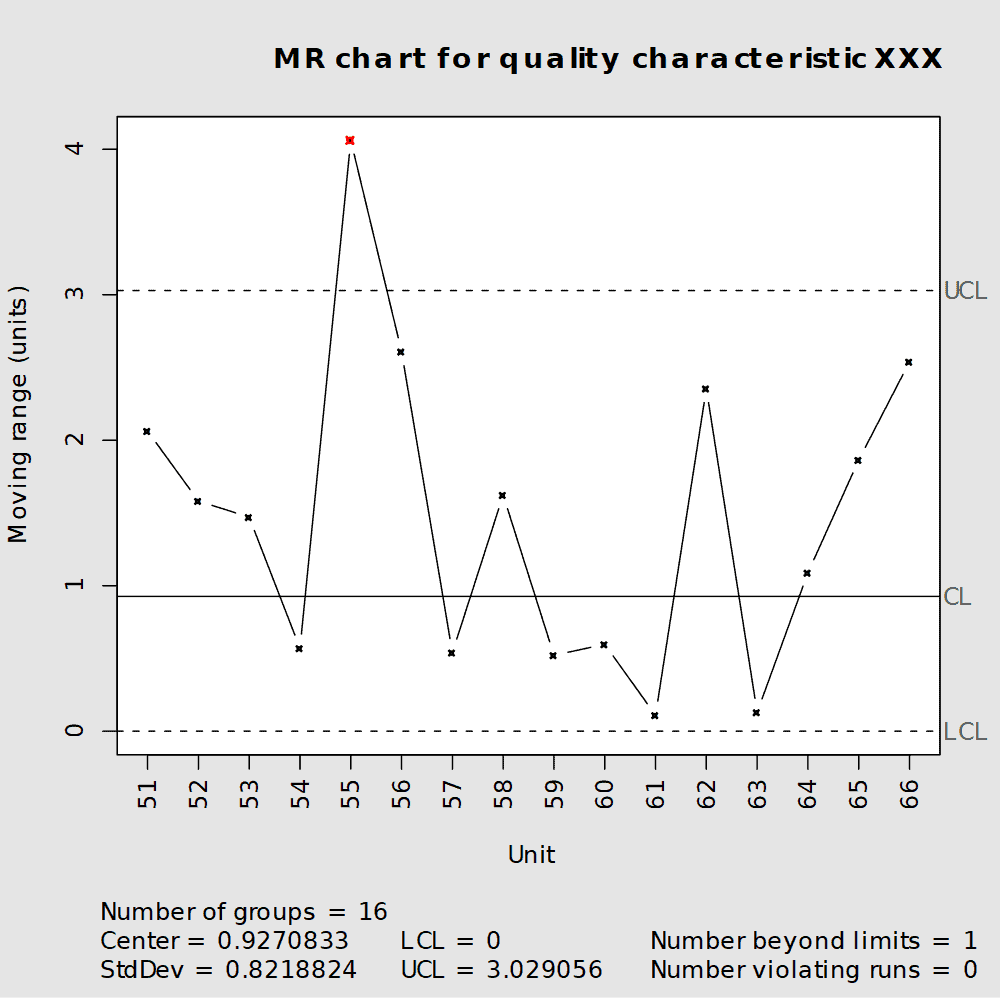
By DanielPenfield – Own work, CC BY-SA 3.0
Later, Joseph Juran applied these at Western Electric, and in the 1950s, W. Edwards Deming taught these methods to Japanese manufacturers. Deming’s work laid the groundwork for what became known as TQM.
What was the reception?
Japanese companies eagerly adopted Deming’s methods. Toyota was a standout early adopter, and by the 1970s–80s, Japanese products had gained a reputation for superior quality. Western companies were losing customers and market share.
This prompted a reckoning in the U.S., marked by the famous TV special: If Japan Can… Why Can’t We?
The principles of TQM took root, and by the late 1980s, it was widely adopted across American industries.
What’s the Minimum a Company Can Do to Practice TQM?
- Decide to implement TQM
- Gain top management support
- Communicate the decision to all stakeholders
- Set baselines for customer satisfaction and current quality levels
- Study and understand TQM principles
- Create a step-by-step implementation plan with deadlines
- Identify and prioritize customer needs
- Identify key processes that impact those needs
- Map and analyze those processes
- Roll out TQM activities
- Train staff in TQM methods
- Monitor progress
- Revise plans as needed
- Collect employee feedback regularly
- Recognize and reward quality efforts
Benefits of TQM
TQM offers significant benefits across industries. These include:
- Improved product and service quality
- Higher employee morale
- Increased productivity
- Lower production costs
- Greater profitability
- More efficient and reliable processes
- Greater employee engagement
- Enhanced workplace environment
Common TQM Tools
TQM uses a range of tools to help:
- Identify quality issues
- Analyze root causes
- Evaluate and visualize data
- Measure outcomes
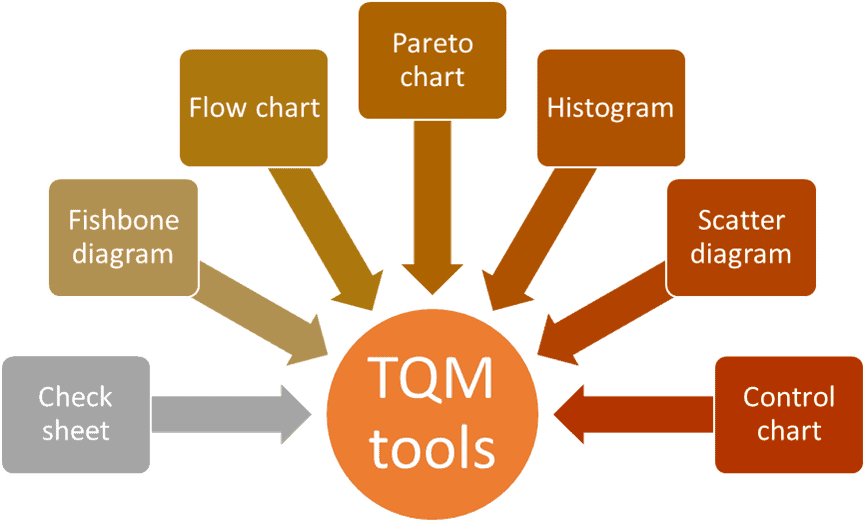
Let’s look at some of the standard TQM tools. You’ll use these to collect data, analyze results, and find problems.
Check Sheet
Used to collect data in real time and spot trends as they emerge.
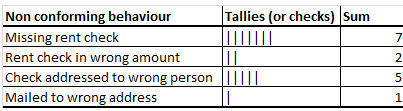
Collect data in real time.
Fishbone Diagram(Ishikawa)
Helps identify the root causes of defects by categorizing potential sources of variation.
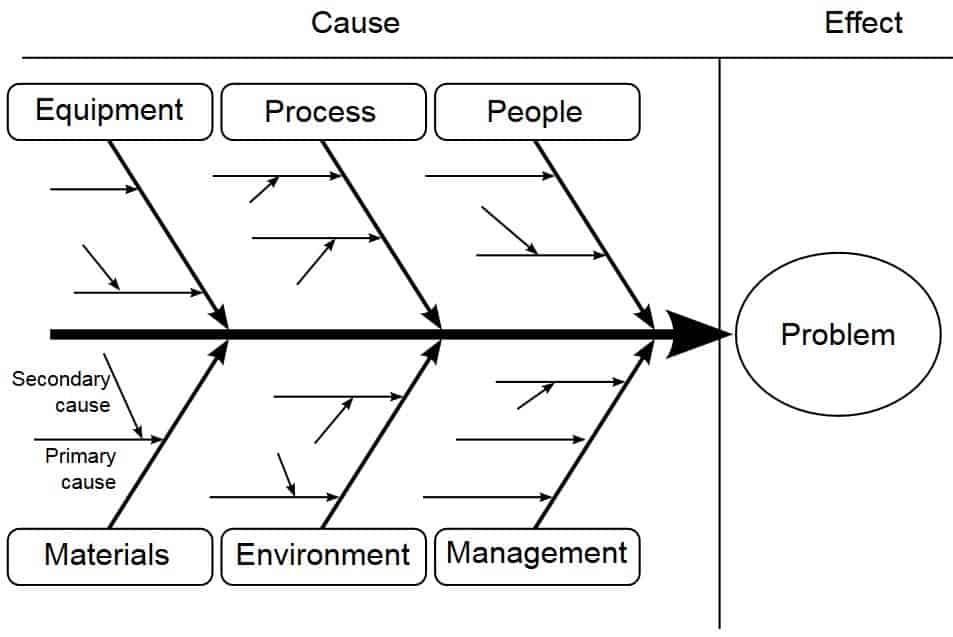
Flow Chart
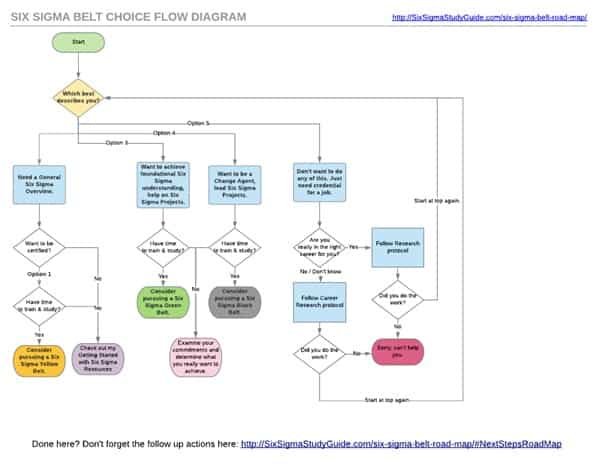
Maps processes to improve understanding and identify improvement opportunities.
Pareto Chart
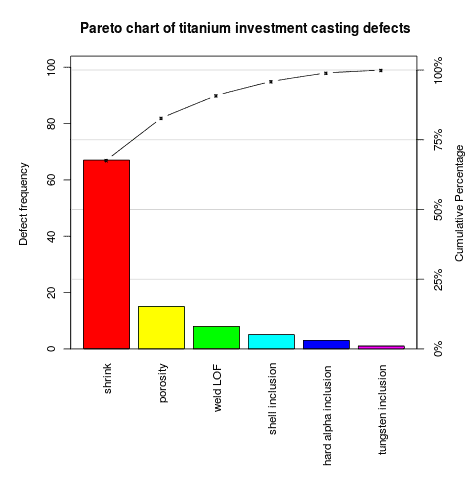
Ranks issues by frequency or impact to help prioritize efforts.
Histogram
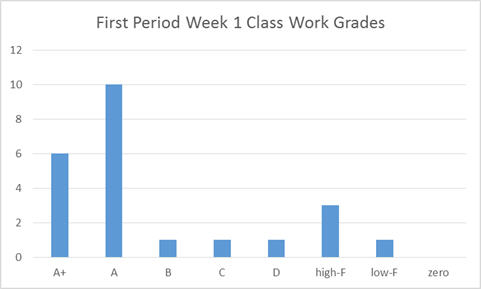
A visual representation of the frequency distribution of data.
Scatter Diagram
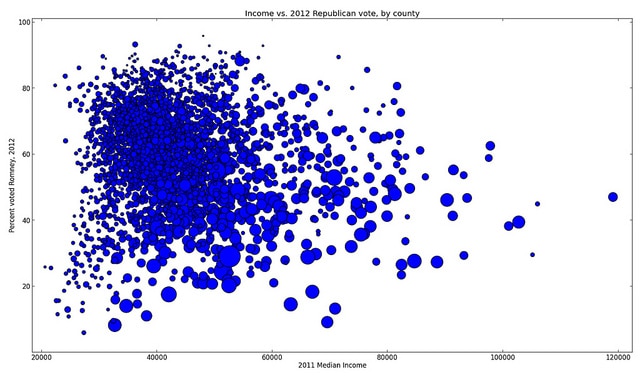
Shows the relationship between two variables, making it easier to spot correlations.
Control Chart
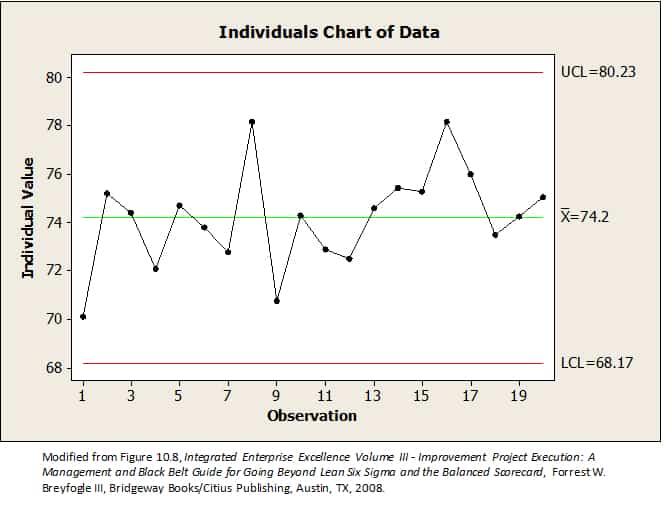
Tracks data over time to highlight trends and variations in a process..
Who Uses Total Quality Management?
Initially popularized in manufacturing (e.g., Toyota, Motorola, Ford), TQM is now used in:
- Banking
- Hospitality
- Education
- Healthcare
- Pharmaceuticals
- Finance
It’s no longer just for manufacturing, but remains essential there.
Is Total Quality Management Still Used?
GAbsolutely. In today’s global economy, the pressure for excellence has only intensified. TQM remains as relevant as ever.
It has also influenced major quality frameworks:
- ISO 9000
- Business Excellence Models
- Awards like the Malcolm Baldrige National Quality Award and Deming Prize
All of these trace their roots to TQM principles.
Six Sigma and Total Quality Management
Similarities
- Both monitor quality and improve output
- Both reduce defects and errors
- Both involve all levels of the organization
- Both are process-focused
Differences
- TQM focuses on process improvement
- Six Sigma focuses on reducing variation
Another distinction: certification.
- Six Sigma requires structured certification (e.g., Green Belt, Black Belt)
- TQM emphasizes training but does not rely on formal certification
Summary:
- Six Sigma: Defect-focused, data-intensive, structured certification
- TQM: Process-focused, continuous improvement, inclusive staff training
Are TQM and Six Sigma Mutually Exclusive?
Not at all.
While Six Sigma came later, it doesn’t replace TQM. In fact, many organizations combine them to great effect.
Each has a unique focus. When used together, they complement one another.
Just be clear about their roles and how they interact within your organization.
Additional Helpful TQM and Six Sigma Articles
- Differences between Six Sigma and TQM
- Similarities and differences between Six Sigma and TQM
- Full PDF
When you’re ready, there are a few ways I can help:
First, join 30,000+ other Six Sigma professionals by subscribing to my email newsletter. A short read every Monday to start your work week off correctly. Always free.
—
If you’re looking to pass your Six Sigma Green Belt or Black Belt exams, I’d recommend starting with my affordable study guide:
1)→ 🟢Pass Your Six Sigma Green Belt
2)→ ⚫Pass Your Six Sigma Black Belt
You’ve spent so much effort learning Lean Six Sigma. Why leave passing your certification exam up to chance? This comprehensive study guide offers 1,000+ exam-like questions for Green Belts (2,000+ for Black Belts) with full answer walkthroughs, access to instructors, detailed study material, and more.
Comments (6)
Below link doesn’t work. Can you please update.
Links updated, Venkatesh. Thanks for letting me know!
In my opinion Six Sigma is one model of TQM. We can say Six Sigma is Motorola’s or GE’s style of TQM.
In my opinion, it’s all the scientific method wrapped and rewrapped.
Thanks for the information. The TQM video shows unavailable. Is there a new link?
Thank you,
Tom
Thanks, Tom.
Looks like that video has been pulled down. I’ve removed it from the page.