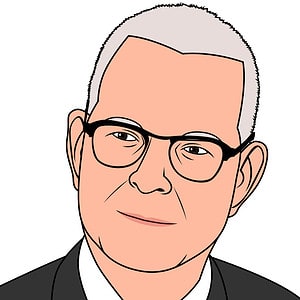
William Edwards Deming was an American management consultant and educator who greatly impacted the process management and control fields in Japan and the United States.
Deming’s Education
William Edwards Deming received an engineering degree from the University of Wyoming. Later, he received a master’s degree in physics and mathematics from the University of Colorado. He completed his studies at Yale University and was awarded a doctorate in mathematical physics. This engineering, math, and physics combination was essential in his later career.
William Edwards Deming and Walter A. Shewhart
Deming was an intern at Western Electric when he met Walter A. Shewhart. Shewhart would later become known as the father of quality control, but he had already developed a number of his core concepts. Deming became a disciple of Shewhart’s ideas.
Shewhart developed methods of statistical control of manufacturing processes. He also came up with the concept of common and special causes of variation in manufacturing. Deming was inspired to devise his methods based on Shewhart’s work. Later, he would take Shewhart’s concepts out of manufacturing and expand them into all enterprise management processes. This would change management methods across the world…eventually.
Deming developed several sampling techniques, some of which he used in the United States 1940 census. He also taught US laborers techniques for statistical process control in World War II. These were effective then but were ineffective in America’s post-war boom.
Deming in Japan
In 1947, US forces, among others, occupied Japan. General Douglas MacArthur wanted to hold a census of the country – and who better to help than the statistics professor who’d developed techniques for the last US census? So, his team invited Deming to Japan. While working on this project, Deming caught the eye of the Union of Japanese Scientists and Engineers (JUSE).
The JUSE was familiar with Shewhart’s work and had adopted many of his techniques. However, it wanted an expert to teach statistical control methods to its members – and Deming was a good fit. In 1950, he delivered dozens of lectures and trained thousands of managers and engineers in quality control.
In 1951, the Japanese government established the Deming Prize, which awarded individual contributions to statistical theory and companies that applied statistical theory.
Japanese manufacturing companies applied the new quality control measures they’d learned from Deming. These companies improved their quality and productivity in the next few years while decreasing costs. Very soon, Japanese goods were in demand around the world.
Back in the US
Deming was ‘discovered’ in the US on an NBC television program in 1980 entitled, “If Japan Can …Why Can’t We?” The US followed suit three decades after Japanese companies embraced Deming’s management theories.
He published several books, including Quality, Productivity, and Competitive Position, in 1982 and, in 1986, Out of the Crisis.
At the invitation of Professor John Whitney, Deming joined the Graduate School of Business at Columbia University in 1988.
Deming wasn’t only interested in management and quality control, though. He was also a skilled organist and composer of music. Accordingly, he brought his love of quality and organization even to this. He wrote a variation of the US national anthem, and many people felt that his version was more accessible to sing. And interestingly, it serves as a metaphor for one of his crucial management theory points. Deming firmly believed that blaming employees for failing to address quality issues was pointless. He reasoned that if there was an issue, it was most commonly due to the system rather than the individual. To fix the problem, go to the source and fix the broken system. Deming’s variation on the national anthem didn’t blame people for being unable to sing a complex tune. Instead, it fixed the problem at its source by simplifying the music.
Deming simply wanted to make it easier for people to sing in life and art.
14 Points for Management
Deming wrote about his fourteen key points in Out of the Crisis. These are principles that he claimed could transform a company. Summarized, they are:
- Keep your vision clear. You should always have an aim, i.e., to become competitive, stay in business, and provide jobs.
- Adopt new philosophies from time to time. Western managers must awaken to the challenge, learn their responsibilities, and take on leadership for change.
- Stop depending on mass inspection. Build quality in the product from the start. Stop awarding business based on price tag alone.
- Instead, minimize total costs. Move toward a single supplier for any item based on a long-term relationship of loyalty and trust.
- Constantly improve your system of production and service to increase quality and reduce waste.
- Institute training and retraining.
- Institute leadership. The aim of supervision should be to lead and help people do a better job.
- Drive out fear so that everyone may work effectively for the company.
- Break down barriers between departments. People in research, design, sales, and production must work as a team to foresee and solve production and supply problems.
- Eliminate slogans, exhortations, and targets for the workforce and focus on building culture and morale.
- Eliminate numerical quotas. Pay attention to quality and methods rather than just numbers.
- Remove barriers to your workers feeling pride in their work.
- Institute a vigorous education and re-training program for management and the workforce.
- Take action to accomplish the transformation. Management and the workforce must work together.
The Seven Deadly Diseases of Management
William Edwards Deming also described the main barriers faced by management when they tried to implement his principles:
- Lack of purpose to plan products and services that will have a market and keep the company afloat.
- An emphasis on short-term profits and short-term thinking (just the opposite of constancy of purpose), fed by fear of unfriendly takeover and demand from bankers and shareholders for dividends.
- Evaluation of performance and annual reviews.
- Mobility of managers and job hopping.
- Using only available data.
- High medical costs.
- High liability costs.
According to Deming, you need effective management and a commitment to quality to combat these seven deadly diseases. He emphasized the importance of communicating quality messages to all staff members and building a belief in total quality management.
Deming’s Chain Reaction
- Improve quality
- Decrease costs
- Improve productivity
- Capture market share with better quality and lower costs
- Stay in business
- Provide jobs.
Deming Wheel or the PDCA Cycle
Walter Shewart created the PDCA cycle. He introduced it to Deming, who was so taken with the concept that he promoted it widely in the 1950s. It came to be known as the Deming Wheel or the Deming Cycle.
To get from a ‘problem faced’ phase to the ‘problem solved’ phase, you can use the PDCA (Plan-Do-Check-Act) cycle. The cycle consists of four stages that you go through iteratively. Continually moving through these stages creates a cycle of continual improvement:
- Plan: Create a strategy to improve a situation.
- Do: Carry out those plans on a small scale first.
- Check: Look at the objective results to see if your changes are working.
- Act: Expand successful strategies to a larger scale.
Note: This is often also known as the Plan-Do-Check-Adjust cycle, where the last step involves modifying the strategy with lessons learned from the Check phase.
Famous books by William Edwards Deming
Out of Crisis (1986): The principles of management transformation, and how you can apply them.
The New Economics for Industry, Government, and Education (1993): The system of profound knowledge that underpins successful use of the principles of management transformation.
Quality, Productivity, and Competitive Position (1982): The faulty practices used in management, and why they’re unhelpful.
Other famous books by him and about him are:
- The Essential Deming: Leadership Principles from the Father of Quality
- Win-Win: W. Edwards Deming, the System of Profound Knowledge, and the Science of Improving Schools
- Sample Design in Business Research
- Some Theory of Sampling
- Statistical Adjustment of Data
William Edwards Deming’s Personal Life
Deming was born in Sioux City, Iowa. He was raised in Polk City, Iowa, on his grandfather’s, Henry Coffin Edwards, chicken farm, and then later on a 40-acre (16 ha) farm purchased by his father in Powell, Wyoming. His father’s name was William Albert Deming, and his mother’s was Pluma Irene Edwards. Both of them were well-educated; hence, they emphasized the importance of education to their children. Pluma was educated in San Francisco and was a musician. William Albert studied mathematics and law.
Deming married Agnes Bell in 1922. She died in 1930, eight years later. A year before Agnes’s death, they had adopted a daughter, Dorothy. Deming raised the infant with the help of various private homes. After his marriage in 1932 to Lola Elizabeth Shupe, he brought Dorothy back home to stay with them. He and Lola had two more children, Diana and Linda. Diana and Linda together have seven grandchildren and three great-grandchildren. Lola and Dorothy died in 1984 and 1986, respectively. William Edwards Deming co-authored several papers with his second wife, Lola Elizabeth Shupe.
Awards and Honors:
Acting on behalf of Emperor Hirohito, the Prime Minister of Japan, Nobusuke Kishi, awarded Deming Japan’s Order of the Sacred Treasure, Second Class in 1960. The medal has a citation that recognizes Deming’s contributions to Japan’s industrial rebirth and its worldwide success.
Deming’s famous Red Bead Experiment is on display outside the American Society for Quality board room, one of his famous exhibits.
In 1947, he was a member of the Rice Statistics Mission. In 1950, he was the assistant to the supreme commander of the Allied Powers and an instructor in sample survey methods for government statistics.
Critiques of William Edwards Deming’s work
There have been a number of criticisms of Deming’s work over the decades. The main ones are:
- His approach doesn’t inspire creativity and innovation in the workplace.
- It is ineffective for generating new products or invading and penetrating new markets.
- A famous quality expert, Joseph Juran, commented that Deming overused statistical methods.
Summary
William Edwards Deming was an eminent scholar and teacher. He is often called ‘the father of management’ due to his famous fourteen principles. They have been the guiding force behind the success of many engineers and managers. He receives much credit for Japan’s emerging economy after the Second World War. Throughout his life, he published many original papers, articles, and books on interrelated subjects like system and system thinking, statistics, and human psychology. He received many honors from the Japanese and American governments and was a trusted consultant to many business leaders worldwide. Many have also referred to him as the father of the third phase of the industrial revolution.
When you’re ready, there are a few ways I can help:
First, join 30,000+ other Six Sigma professionals by subscribing to my email newsletter. A short read every Monday to start your work week off correctly. Always free.
—
If you’re looking to pass your Six Sigma Green Belt or Black Belt exams, I’d recommend starting with my affordable study guide:
1)→ 🟢Pass Your Six Sigma Green Belt
2)→ ⚫Pass Your Six Sigma Black Belt
You’ve spent so much effort learning Lean Six Sigma. Why leave passing your certification exam up to chance? This comprehensive study guide offers 1,000+ exam-like questions for Green Belts (2,000+ for Black Belts) with full answer walkthroughs, access to instructors, detailed study material, and more.
Comments (6)
DR DEMING IS MY MOTIVATION, HE IS MY ROLE MODEL AND TO ME HE STILL LIVES.
That’s powerfu, thank you for sharing! Dr. W. Edwards Deming’s legacy continues to inspire generations of quality professionals, and it’s amazing to hear how deeply his philosophy resonates with you.
His teachings on continuous improvement, systems thinking, and the importance of leadership in quality still form the backbone of modern Lean and Six Sigma practices. If you’re pursuing a certification or career in quality, channeling his principles will serve you well every step of the way.
Truly, his influence lives on through passionate professionals like you!
This is a very poorly written article.
Hi Dillon,
Thank you for letting me know. I’ll take a look. What specific suggestions do you have for improvement?
Best, Ted.
This is an informative summary of Demming and easy to read & follow. Thank you.
You’re welcome, Angela. Thank you for the kind comments.