Six Sigma documentation refers to documents that contain details about the project. Documentation is a tool that helps the team to gather facts and thoughts in a formal way. An effective control system will be placed with formal documentation.
Six Sigma projects bring knowledge and benefits. The knowledge needs to be clearly documented, communicated, and stored in the knowledge repository. Six Sigma documentation is a set of documents reported on paper, digital, or online systems. For example, work instructions, online SOPs, reference guides, audio, or video tapes, etc.
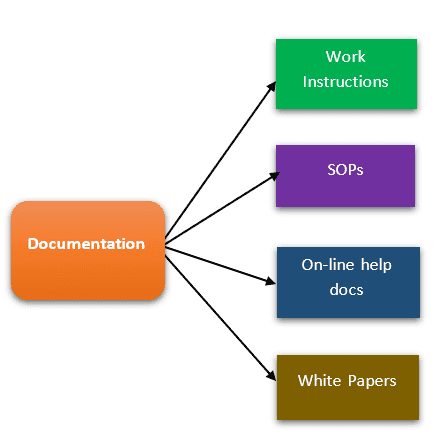
Documentation of a Six Sigma project is critical throughout the project. The Six Sigma project team updates documentation throughout the project which includes flow maps, checklists, project charter, minutes of the meeting, statistical analysis summaries, test results, etc.
Why Documentation
The main objective of documentation is to maintain the documents that are up to date, so they act as a reference for any documentary requirements. After the completion of process improvements, the documentation is to be updated to the new methods. Also, train the users on new documentation.
Documentation gains a better understating of the project and also helps to share the thoughts and status of the project with the stakeholders. Hence, it should be written to a level that is understood by all the users.
Importance of Documentation in a Six Sigma Project
Depending on the nature of the project, each project produces a number of different documents. Project documentation includes project status reports, a project charter, a project plan, risk registers, and project action items.
The frequency of the documentation depends on the need and complexity of the project. Share all the necessary documents with stakeholders to keep them abreast of the status of the project.
Another example of project documentation is the final project report. Usually, Black belts prepare the final project report at end of the project and include a summary of the complete project. The final six sigma project report submit to all the stakeholders for review and approval.
Types of documents
Most organizations manage the documentation in a hierarchy. Various types of documents including:
- Quality Manual: The Quality Manual is the highest-level document that describes the organization’s QMS (Quality Management System). In other words, it outlines the operation and processes in an organization.
- Procedures: Procedures are at the second level and specify the activities to be performed. Furthermore, it clearly states the roles and responsibilities of various personnel to accomplish the task.
- Work Instructions/SOPs: Work instructions basically contain step-by-step descriptions of how to perform a task.
- Records: Records provide objective evidence that the data collected of the product and processes. It gives confidence that the QMS is effective in the organization.
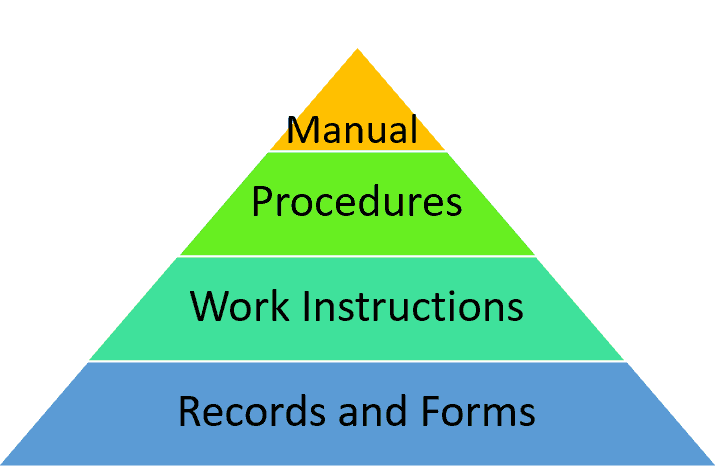
Six Sigma Documentation Guidelines
- Documents shall be clear, easy to understand, legible, and free from ambiguity
- Document every activity and maintain data integrity
- Does not document the activities before the activities are performed
- Train users before implementing new documentation methods
- Perform audits to ensure compliance and performance
Benefits of Six Sigma Documentation
- Documentation serves as written proof for the execution of the project
- Helps the team to achieve a common understating of requirements and status of the project
- Since decisions and outputs are documented, it removes personal bias.
- Better, faster decision making
- Increases productivity, as teams quickly refer to the previous six sigma project documents to gain the knowledge
- Decreases time spent on training
- Documentation helps to debrief the management team about the project.
Project Documentation
Project documentation means recording regular and major events and activities and properly communicating with the relevant stakeholders. The methods of project documentation for planning, monitoring, and controlling projects range from manual techniques (for example graphs, grease boards, and colored magnetic markets) to computer software. The main objective of project documentation either with manual or software tools is to organize and summarise the data in a meaningful way.
Milestones are significant points in the project which are planned to be completed at a specific point in time. In addition, Black belts or project leads typically create project documentation or presentation tools (storyboards, spreadsheet summary of results) for management review at each major milestone, this will help to identify the roadblocks to the completion of the project.
Document Control
Document control is the framework for deciding how Six sigma project information is created and managed. It ensures that document information has an appropriate description, format, and media. Furthermore, document control ensures appropriate review and approval for suitability and adequacy.
Document control helps in sustaining Six Sigma improvements when the documentation information is available and suitable for use where and when it is needed and protected.
Team dynamics
Team dynamics refers to the force that inspires or drives a group of people to work collectively for a common cause or objective. A good team is a team with different personalities and also a common identity.
Team mechanics refers to conducting meetings with the proper agendas, times, and locations, and also distributing the meeting minutes to all stakeholders. In fact, meetings are an essential part of sharing information and making decisions that help to capitalize on the strengths and experiences of a group of people with common goals.
Communication plan
A communications plan can be as simple as a spreadsheet. It contains all the communications that you’re planning to make about a project.
It includes the following information:
- Medium: The medium that you’ll be using to communicate. This might be an email, a face-to-face meeting, a video, or a written report.
- Audience: Who needs the information? For example, you might present the results of a project to the company’s upper management, but give weekly updates to the project manager only.
- Reason: What you’re trying to achieve. For instance, a kick-off meeting typically introduces the key aims of a project to stakeholders and sets expectations. On the other hand, the aim of a ‘lessons learned’ meeting is to codify information obtained during a project, for later action.
- Timing: When the communication will be made. This might be a specific date, a milestone, or a contingency. For example, “If a project is running late by more than one week” could be a contingency timing option.
- Method: Go into more detail about the type of communication. For example, you might require a presentation, a time-boxed stand-up, or a visual dashboard.
- Responsible party: The person ultimately responsible for organizing and/or presenting the information.
Control Plan
A control plan is an example of a quality control (QC) strategy. Put one in place after you create a new process or change an existing one. It helps you to ensure that staff monitors new and modified processes correctly.
Typically, you’ll have one plan per process. Alternatively, it could be one per product or service that you offer. What’s the difference? Some products and services will involve more than one process. In this situation, you’ll usually perform QC per process.
A control plan for a process typically contains:
- Specifications and measuring guide. This includes measurements, how to make them, and the tolerance allowable.
- Inputs and outputs. What should go into the process (materials)? What should come out?
- Performance criteria for the process. How do you know when the process is working well? This might include QA figures or a production rate.
- Sampling and reporting frequency. How often will you perform quality control checks? Then, how often will you create QC reports for the process?
- How to record information about the plan. What sort of charts should you use?
- Contingency measures. What should you do if X goes wrong?
- The owner of the process. Who is responsible for reporting and oversight?
Six Sigma Tollgate Reviews
DMAIC Tollgate Reviews, also called milestone meetings or phase gates, are one of the most important skills a practicing six sigma professional needs for success. Tollgates are an analogy to places on the highway where you need to slow down and pay a toll before proceeding. In Six Sigma practice, there’s no need for a project team to pay a toll, but it’s rather a mechanism to review progress with sponsors and stakeholders and ensure the project is on course. A natural way to do this would be at the end of each phase of a DMAIC project.
Every tollgate may include:
- Project Charter
- Performance-based goal statement
- High-level process maps such as a SIPOC diagram
- Financial measures (eg Cost Benefit Analysis, Cost of Quality)
- Critical to Quality measures.
- Graphs and data related to the current phase
Lessons Learned
Lessons learned are the documented information that includes both positive and negative experiences of a six sigma project. A Six Sigma project often explains many lessons to project teams and stakeholders over the time needed for a Six Sigma team to document the key elements in the lessons learned database.
In an organization, there is always an opportunity to apply the lessons learned from one six sigma project to various areas of the business. By replicating the changes done during a project, the benefits of Six Sigma can be multiplied manyfold, often at a very minimal cost. Hence, a robust knowledge management approach may help to document the lessons learned.
Also, the lessons learned process includes identifying, documenting, analyzing, storing, and retrieving to capture, record, and use the collected data.
The process to capture Lessons Learned
- Capture both positive and negative experiences
- Conduct lessons learned periodically to capture all the key elements without fail
- Maintain lessons learned database to capture all the key information throughout the project
- Ensure the lessons learned database accessible to all project members within the organization
- Involve subject matter experts and other relevant stakeholders to gain feedback while preparing lessons learned database
Project Closure
A Project Closure document summarizes the project activities, results, financial benefits, tasks status, and project approvals (for example, the business owner, finance, QA, and other stakeholders) to formally approve that the project is complete. Generally, a Six Sigma black belt or project leader creates the project closure document. Moreover, the project closure document is often considered the formal hand-off of the project to the respective process owner which contains the status of the improved process and the documentation of the completion of the project.
Black belts or project leaders to audit the closure report periodically to check the:
- Status of control plan
- Financial benefits validation
- Status of open action items
- Performance metrics data
- Project technical support
- Document control and implementation of Quality systems
- Management approval or feedback