What is a SIPOC?
A SIPOC is a high-level process mapping tool that helps visualize a process and its influences. In other words, it is a useful tool that depicts how a process serves the customer and shows the inputs and outputs of a process in a visual format.
The acronym for SIPOC stands for Supplier, Input, Process, Output, and Customer. However, the construction of SIPOC has always involved identifying the process, determining the output of the process, recognizing the customer receiving the outputs, finding the inputs, and then finding suppliers of the inputs. So, often, it is called a POCIS diagram.
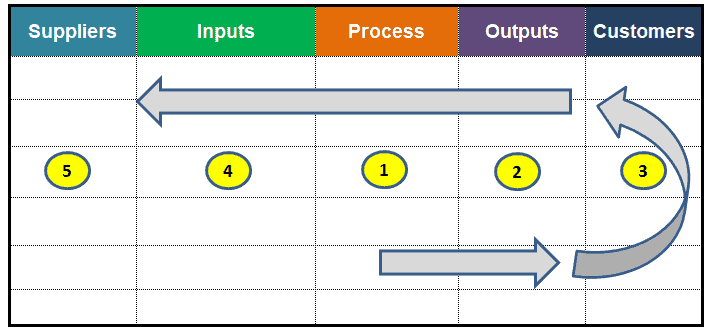
When Do You Use It?
Creating SIPOC is very helpful to continuous improvement projects like Six Sigma. Moreover, internal inputs and processes are usually accessible for a DMAIC team to access in the define phase. Hence, SIPOC is often used in the Define phase of DMAIC.
Additionally, SIPOC is very useful when part of the process is unclear. SIPOC helps teams, top management, and stakeholders resolve process-related issues and plan appropriate improvement strategies.
Why Use a SIPOC?
SIPOC is one of the primary factors for process improvement. Moreover, the diagram helps the team and the sponsor agree on the project boundary and scope. SIPOCs also help determine the variation in Key Process Input Variables (KVIPs) and Key Process Output Variables (KPOVs), which can significantly impact manufacturability and serviceability reliability, and product efficiency.
How to create a SIPOC?
SIPOC is a table that documents the process, output, customer, input, and supplier in a table format with the help of the following steps
- Identify the process: Identify the process for which SIPOC will be created. Identify the process as a team.
- Define the process steps: A process is a defined sequence of activities that usually adds value to inputs to produce customer outputs. High-level process flow covers a maximum of 7 steps; otherwise, it is hard to follow. Use an Affinity Diagram to reduce larger processes to a few key steps.
- List the Outputs: Outputs are the products, services, and/or information that are valuable to the customers. This includes products, materials, or services delivered to the customer.
- Identify the Customers: Customers are the users of the outputs produced by the process. Moreover, customers are not always outside the organization; they may also be internal stakeholders.
- Determine the Inputs required for the process: Inputs define the material, service, and/or information used to produce the outputs. An input plays a vital role, as input variation impacts the output.
- Identify the Suppliers: Suppliers provide inputs to the process. Not only external suppliers. You should also cover internal suppliers.
- Validate the diagram: Once completed, share it with all relevant stakeholders and validate it before moving to the process improvement stage.
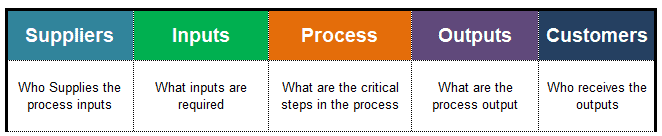
Benefits
- It helps to define the new process.
- Provides a project overview for all the stakeholders.
- Provides a high-level project overview to the top management.
- Problem-solving initiative.
- Provides input and output information for critical processes.
- Ensures all the stakeholders are on the same page.
Example SIPOC in a DMAIC Project
Example: The ABC chocolate factory in Houston is working to improve its operating processes using Six Sigma. During the Define phase, the team attempts to develop a SIPOC to understand how the chocolate manufacturing process serves the customer. They want to summarize this information and present the inputs and outputs of a process in a visual format.
- Identify the process: The chocolate manufacturing process.
- Define the process steps: The following is the high-level process
- Input goods inspection
- Meltdown chocolate blocks in warmers
- Add ingredients to the chocolate paste
- Temper verification
- Chocolate line production and packing
- List down the Outputs: The following are the outputs at various stages
- Approved batches of chocolate blocks and Ingredients
- Chocolate paste
- Chocolate chips
- Acceptable chocolate chips
- Packaged chocolate chips
- Identify the Customers: Wholesalers and Retailers.
- Determine the Inputs required for the process: The following are the inputs required at various stages of operations.
- Potato chips and raw chocolate blocks
- Coating ingredients
- Blocks
- Chocolate Paste & Ingredients
- Chocolate Chips
- Properly tempered chocolate chips
- Identify the Suppliers: The following are the suppliers – Draino Inc and Coco Ingredients Inc provide inputs for the manufacturing unit.
- Validate diagram: Finally, Validate it with relevant stakeholders within the organization.
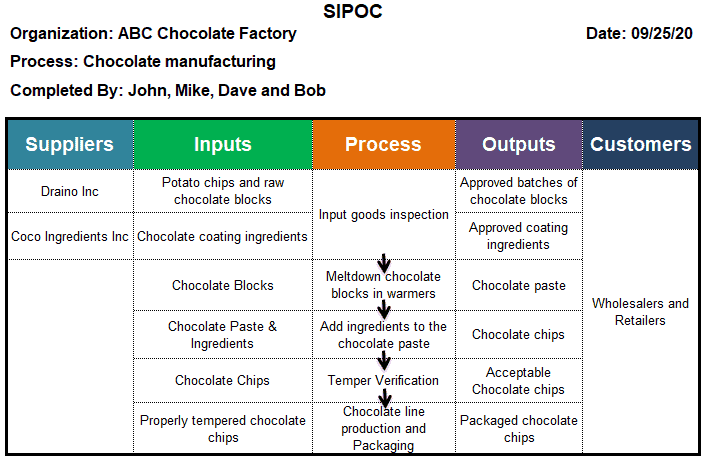
Important Videos
SIPOC Important Links
https://asq.org/quality-resources/sipoc
SIPOC Excel Template Download
When you’re ready, there are a few ways I can help:
First, join 30,000+ other Six Sigma professionals by subscribing to my email newsletter. A short read every Monday to start your work week off correctly. Always free.
—
If you’re looking to pass your Six Sigma Green Belt or Black Belt exams, I’d recommend starting with my affordable study guide:
1)โ ๐ขPass Your Six Sigma Green Beltโโ
2)โ โซPass Your Six Sigma Black Belt โโโ
You’ve spent so much effort learning Lean Six Sigma. Why leave passing your certification exam up to chance? This comprehensive study guide offers 1,000+ exam-like questions for Green Belts (2,000+ for Black Belts) with full answer walkthroughs, access to instructors, detailed study material, and more.
Comments (8)
What is the SIPOC study for ABSENTEEISM
Really don’t know what you’re talking about Dhurkadaas. Can you elaborate?
The ASQ link is not specific to SIPOC, can you clarify what we should be seeing?
Hi Karen,
Thanks! Looks like they changed the location of the page. Updated to here: http://asqservicequality.org/glossary/sipoc-suppliers-inputs-process-outputs-customers-diagram/
Hi Ted, the SIPOC (Suppliers, Inputs, Process, Outputs, Customers) Diagram link doesn’t appear to be working. Has the location of the file changed?
Hi Matt,
Yes, looks like that location changed. I had previously linked to an ASQ resource that they have now put in their members-only section.
I’ll replace that link with one to the visuals here. And I’ll add a note to make my own downloadable template for members in the near future.
Thanks for the head’s up!
Best, Ted.
Hey Ted,
In Process Modeling & Process Mapping for Black Belts Quiz, one of the questions mentions work-flow diagrams. I do not see an article that explains Work-Flow Diagrams. Where you do recommend I go for more information?
Sure! Here’s a brief primer on workflow diagrams tailored for Six Sigma Black Belts:
A workflow diagram is a visual representation of a process, showing how tasks, information, or decisions flow from one step to another. It helps identify inefficiencies, redundancies, or delays within a process. Common elements include:
Workflow diagrams are foundational in process mapping and are key tools in DMAIC to visualize current states and design improved future states.
For a deeper look, see this guide on Process Map & Flowchart Symbols.
Hope this helps clarify things!
Best regards,
Ted