A manufacturing company utilized Six Sigma and DMEDI to improve the manual handling of materials in the production area. The case study followed the Six Sigma DMEDI methodology to investigate root causes and provide solutions to reduce defects. Before the project, the company had concerns about incidents and learning events related to the ergonomics, health, and safety of operators involved in manual material handling.
The project’s goal was to improve the process and design new processes for material handling, ultimately leading to financial contributions. The study was presented at the MOTSP 2020 conference by Atanas Kochov, PhD., and Aleksandar Argilovski from the Faculty of Mechanical Engineering in North Macedonia.
The proposed process improvement approach involves several steps. These steps include selecting an appropriate Six Sigma framework, mapping the current process, establishing key performance indicators, and using various design tools and techniques. The proposed approach aims to address the existing problem, enhance ergonomics and safety, and increase process efficiency while reducing the cost of manually handling spilled materials.
Company A implemented the DMEDI approach of Six Sigma, which stands for Define, Measure, Explore, Develop, Implement.
The Application of Six Sigma DMEDI Methodology In the Manufacturing Industry
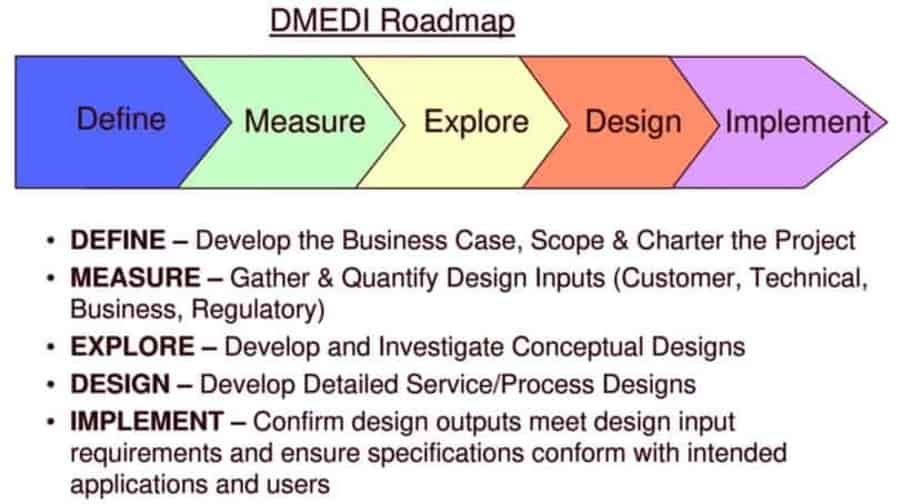
Six Sigma is a popular problem-solving method widely used in manufacturing. In this study, the researchers discuss the minimum number of tools needed for a Six Sigma project and share the results of a project initiated by Company A’s Continuous Improvement department.
The management tasked the department to improve the process of handing powder materials on an elevated platform in the production area. The team used the Six Sigma framework to address these issues to generate statistically supported solutions.
The Six Sigma framework comprises five phases: define, measure, analyze, improve, and control (DMAIC). This framework is most suitable for improving existing processes or products. However, when there is no existing process to improve or a new process is needed, the Six Sigma DMEDI framework (define, measure, explore, design, and implement) is preferred.
The Six Sigma DMEDI framework is commonly used during feasibility studies or in the detailed design phase of more extensive projects. In this instance, the team employed the framework to gather all necessary information regarding the proposed project and determine the best conceptual design to address the current issue.
The main objective of this Six Sigma project is to find a practical solution for reducing manual handling in real manufacturing companies. Furthermore, this Six Sigma project aims to deliver a statistically-based engineering solution quickly. So, they selected a minimum number of tools to achieve the desired outcome while minimizing the required time.
DMEDI Phase: Manufacturing Industry Sigma Six Case Study
Define Phase
The team did a few things in this phase to start a project successfully. First, they gather information from the end user, create a basic plan, identify problems and goals, and figure out what resources they need (like time, people, and money). They used project management tools to help with this.
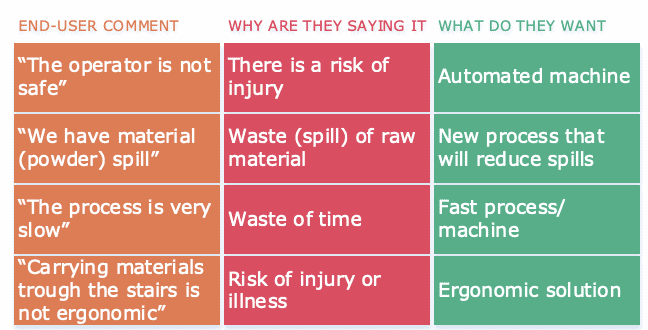
Regarding resources, they listed all the things they needed to make, like documents or physical objects. They used a Product Breakdown Structure to help with this. Then, they find people with the skills to make those things and determine how much it will cost. When planning the project’s length, the team also considers company procedures, customer requirements, and delivery schedules.
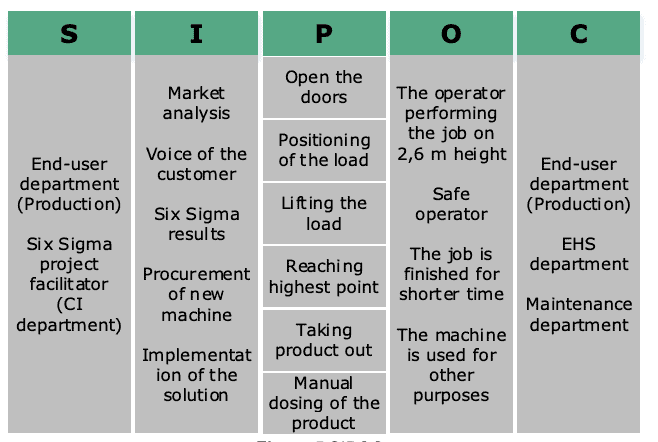
Researchers use tools like a Network Diagram and a Gantt chart to keep track of everything in the manufacturing company. This helps show the flow of activities and the timeline of the project. In addition, the project charter incorporates specified resources, Voice of the Customer (VOC), and SIPOC as its inputs. The project charter is a commonly used Six Sigma tool for providing an overview of the project, and it can take the form of a poster that includes this information.
Measure Phase
The measure phase is all about understanding how the process currently works. First, the team collects data on how fast, good, and expensive the process is and figures out what’s causing the problems. They do this by examining the process and creating key performance indicators (KPIs) that show improvement. In this step, one of the main things they need to create is a map of the current process, the KPIs they’ve created, and the KPIs they’ve measured for the current process.
For example, let’s say they are looking at a process that involves moving materials up to a high platform. The team has observed that the process involves many manual steps and created a flow diagram to show how it works. They have watched the process several times and wanted to understand its speed, efficiency, and cost.
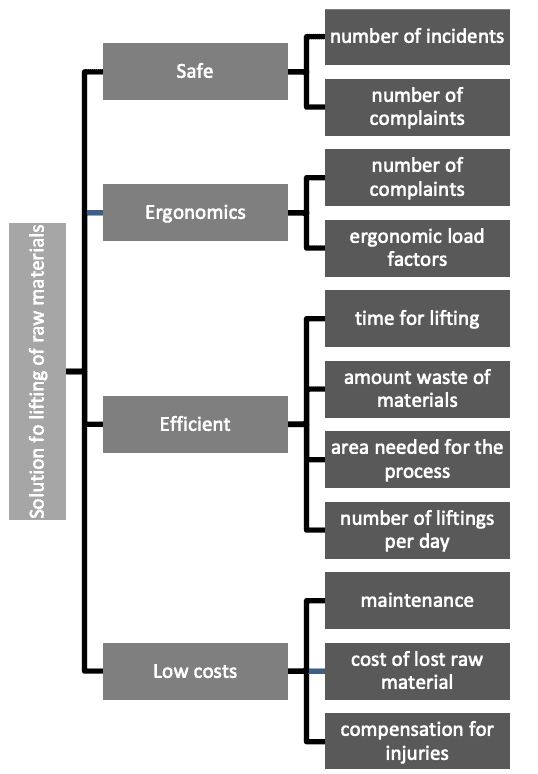
To create KPIs, the researchers consider what the end user wants and how to measure whether they meet their needs. They used the “Tree of Requirements” to break down the end user’s needs into measurable indicators. For instance, you can measure the time it takes to move the materials to the platform. This can help the manufacturing company’s workers achieve a faster process.
Explore Phase
This phase aims to identify the underlying cause(s) of a problem and focus on solving it in the subsequent phase. The team performs root cause analysis using tools such as Fishbone Diagram, Pareto Chart, 4CP Analysis, 5 Whys, etc. The entire project team is involved in this phase to brainstorm possible issues and identify the root cause(s) of the problem. It is possible for a problem to have multiple root causes at times. That’s where the Pareto Chart comes in handy, as it helps prioritize which root cause is causing most of the problems.
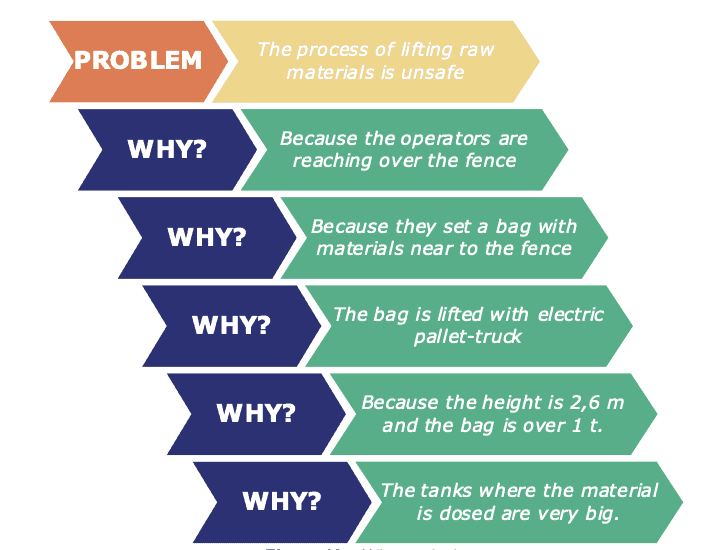
As multiple factors contribute to this issue, the 5 Why analysis presented in this case study focuses on one of the primary concerns: the unsafe process of lifting raw materials. To illustrate how the 5 Whys analysis works, let’s take the example of the “unsafe process of lifting raw materials. First, the team would ask, “Why is lifting raw materials unsafe?” Then, they would gather data during the first two phases. Based on this data, the team would answer the question. Finally, they would conclude that lifting raw materials is unsafe because operators must reach over a fence to get the materials.
In addition, with the help of an electric pallet truck, the raw materials are elevated to a height of 2.6 meters above the ground. Then, the team continues asking “Why?” based on the answer to the previous question until they identify the root cause(s) of the problem. The root cause analysis phase of Six Sigma is crucial in identifying and addressing the underlying cause(s) of a problem.
Design Phase
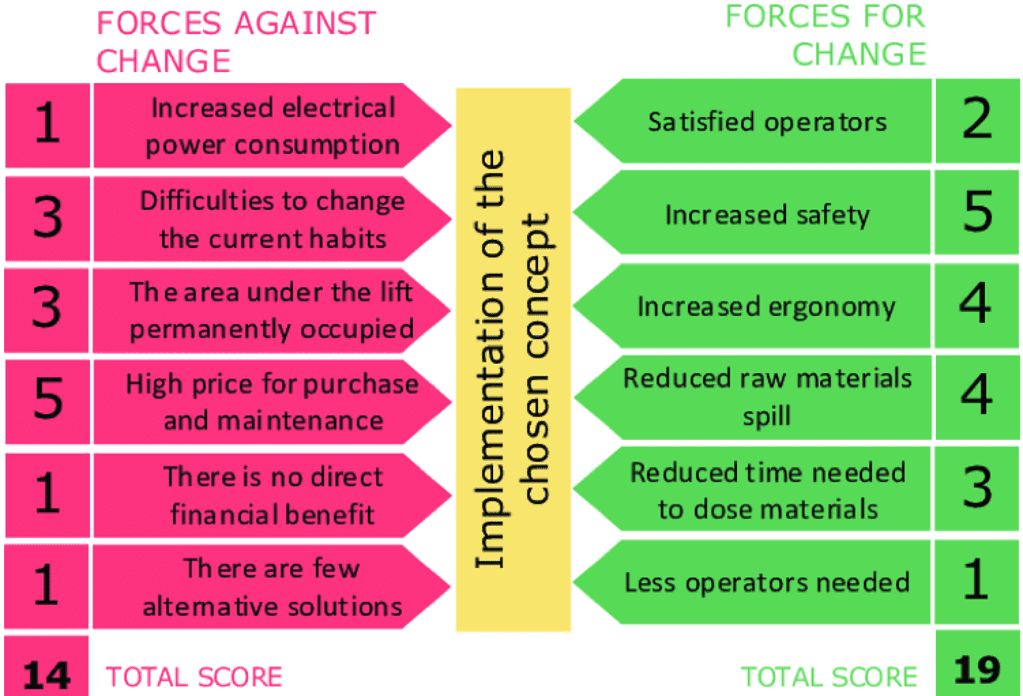
The Six Sigma DMEDI project did not entail detailed design or technical drawings for manufacturing. However, it confirms the design specifications to ensure the solution meets the end user’s requirements, enhances measured KPIs, and resolves issues identified through root cause analysis.
The team employs the Morphological Matrix to generate new concepts for this case study. This tool features two columns:
- The first for necessary functions of the product or process
- The second is for brainstorming solutions for each function.
By combining these solutions, several concepts can be generated. Then, after evaluating these concepts based on end-user needs, the best concepts can be chosen for further development.
Implement Phase
This project aims to meet user requirements, improve processes, and solve previous issues. However, it won’t make technical drawings or detailed designs for manufacturing.
The team uses a Morphological Matrix to develop new ideas. It has two columns. One lists the necessary functions, while the other brainstorms solutions for each. Combining different solutions for each function can create many concepts. Then, the team will evaluate these concepts based on the user’s needs and select the best one for further development.
To ensure sustainable and effective solution control, Six Sigma DMEDI offers several options. These include providing employee training, measuring KPIs periodically, implementing 5S, and standardizing work instructions.
Manufacturing Industry Six Sigma DMEDI Conclusion
The Six Sigma DMEDI framework is a detailed approach in Six Sigma to solving problems. It helped Company A find solutions to issues that made work difficult and unsafe for its operators. The team used Six Sigma tools like Voice of the Customer, Process Flow Diagram, Key Performance Indicators, and Control chart. As a result, they delivered the project’s crucial outcome while satisfying the end user with a minimum number of tools.
Company A used these tools to solve ergonomic, safety, spillage, and time issues in powder dosing and promote LEAN culture. The improvements also led to cost reduction, faster production, and better quality, making the company more competitive. Six Sigma improves specific issues and promotes a systematic approach to problem-solving. It also builds a new culture in companies, leading to faster satisfaction for the end user.
When you’re ready, there are a few ways I can help:
First, join 30,000+ other Six Sigma professionals by subscribing to my email newsletter. A short read every Monday to start your work week off correctly. Always free.
—
If you’re looking to pass your Six Sigma Green Belt or Black Belt exams, I’d recommend starting with my affordable study guide:
1)→ 🟢Pass Your Six Sigma Green Belt
2)→ ⚫Pass Your Six Sigma Black Belt
You’ve spent so much effort learning Lean Six Sigma. Why leave passing your certification exam up to chance? This comprehensive study guide offers 1,000+ exam-like questions for Green Belts (2,000+ for Black Belts) with full answer walkthroughs, access to instructors, detailed study material, and more.