DMAIC is Six Sigma’s signature framework for process improvement. It provides a structured way of improving a process.
Key Attributes
A DMAIC improvement process:
- Is data-driven.
- Is followed in a strict sequence.
- Uses all five steps.
The Five DMAIC Stages
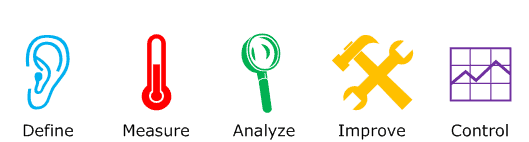
The five stages we use are:
- Define: Collate what we already know about the existing process.
- Measure: Collect further data about the existing process.
- Analyze: Identify the core problems that we’ll address.
- Improve: Plan, test, and implement solutions.
- Control: Set up supports to ensure that successful solutions are sustainable.
Note how this is reminiscent of the Deming wheel or Shewhart Wheel: Plan-Do-Study-Act).
History of DMAIC
Michel Harry & Bill Smith created “MAIC” – the methodology that evolved to become DMAIC.
Harry includes the following strategy elements in the traditional approach to Six Sigma:
- (R) Recognize the true state of your business
- (S) Standardize the systems that prove to be best-in-class
- (I) Integrate best-in-class systems into the strategic planning framework.
What’s the difference between Six Sigma and DMAIC?
Six Sigma and DMAIC are closely related, as DMAIC is the problem-solving methodology used in Six Sigma. Six Sigma is a data-driven approach to process improvement that aims to minimize defects and variability in products and services. It uses statistical analysis and other tools to identify and eliminate the root causes of defects, and ultimately improve business performance.
DMAIC, on the other hand, is the acronym that describes the five-step problem-solving process used in Six Sigma projects. It stands for Define, Measure, Analyze, Improve, and Control. DMAIC provides a structured and disciplined approach to problem-solving that enables organizations to achieve Six Sigma levels of quality and efficiency.
Can you use DMAIC outside of Six Sigma?
Absolutely! DMAIC can be used for non-Six Sigma purposes as well.
DMAIC is a structured and disciplined problem-solving methodology that can be applied to a wide range of industries and situations beyond just Six Sigma. The five steps of DMAIC (Define, Measure, Analyze, Improve, and Control) provide a framework for identifying and eliminating problems, improving processes, and achieving better outcomes.
For example, DMAIC can be used in healthcare to improve patient care processes, reduce medical errors, and increase patient satisfaction. In the software industry, DMAIC can be used to identify and fix software bugs, improve user experience, and optimize software development processes. In construction, DMAIC can be used to improve safety practices, reduce waste, and increase productivity.
The key benefit of using DMAIC outside of Six Sigma is that it provides a standardized and data-driven approach to problem-solving that can be applied in any industry or situation. By using DMAIC, organizations can identify and address the root causes of problems, improve processes, and achieve better outcomes, regardless of whether they are formally practicing Six Sigma or not.
The DMAIC Phases
Define Phase
Summary
In the Define phase, you collate a lot of information you already have available. You’ll:
- Understand the project, including its purpose and scope.
- Map the current process.
- Determine whether the process is a good candidate for DMAIC.
- Detail customer expectations.
- Estimate timelines and costs.
Should you use DMAIC?
Some projects aren’t suitable for this process. For example:
- It’s already very clear what the problem is and how to solve it.
- There’s no or little available data on the process to be improved.
- Managers and leaders do not support improvements to this process.
- The process does not directly impact key performance indicators.
- Measuring process improvements would be difficult or impossible.
Further information about the Define phase
For more information about the Define phase, the steps to go through, and the tools to use, see Define Phase (DMAIC).
Measure Phase
Summary
You’ve mapped the existing process, understood the project, and decided that this is a good DMAIC candidate. You’ve listed customer expectations and estimated the times and costs involved.
Your next phase involves a lot of measurements. You need to have baseline figures to assess progress accurately in later phases.
During this phase, you will:
- Identify the data that you need to collect.
- Decide what measurements to use.
- Figure out what methods to use to collect your measurements.
- Determine the level of variation that you’ll be dealing with.
- Collect the data as per previous points.
Further information about the Measure phase
For more information about the Measure phase, the steps to go through, and the tools to use, see Measure Phase (DMAIC).
Analyze Phase
Summary
In the Analyze phase, you work with the data that you collected in the Measure phase. You’ll:
- Identify defect causes.
- Analyze these to pinpoint the root cause.
Further information about the Analyze phase
For more information about the Analyze phase, the steps to go through, and the tools to use, see Analyze Phase (DMAIC).
Improve Phase
Summary
You’ve identified the root cause of your issue in the Analyze phase. Now you need to come up with a solution. You’ll:
- Pull in people who perform or oversee the process.
- Brainstorm potential solutions.
- Determine criteria for selecting a solution.
- Weigh potential solutions against the criteria.
- Pick a solution.
- Test the chosen solution.
- Measure the results and compare them to the Measure phase data.
Further information about the Improve phase
For more information about the Improve phase, the steps to go through, and the tools to use, see Improve Phase (DMAIC).
Control Phase
Summary
Once you’re happy that the chosen solution will improve the process, it’s time to implement the Control phase. This is where you actually implement the said solution, but there are some other tasks too:
- Document the solution.
- Collect data about how the solution is working in production.
- Put supports in place to ensure the solution is permanent, not temporary.
- Set up a plan to deal with any issues that might arise.
- Plan handover to the operations personnel.
Further information about the Control phase
For more information about the Control phase, the steps to go through, and the tools to use, see Control Phase (DMAIC).
DMAIC Tollgate Reviews
You’ll typically review progress regularly with your sponsors. This kind of review, especially when ending one phase and moving on to the next, is called a Tollgate review.
Learn more about DMAIC tollgate reviews here.
Comments (8)
Is there suppose to be a “what makes a good DMAIC project” video attached?
There will be soon. We’re currently reconstructing this page to have a different organization and more details.
H Ted,
Can DMAIC tools or methodology can be used in FOCUS PDCA project? what tools are relevant? What tools are not relevant?
I hadn’t heard of FOCUS so thank you for mentioning it so I could look it up.
DMAIC is an offshoot of the PDCA process (As is Agile and many other frameworks) so I’m inclined to say yes, it is.
Here’s how I would see it stacking up:
Plan -> D: Define, M: Measure, A: Analyze
Do – > I: Implement.
Check -> C: Control.
Act -> C: Control (specifically Control Plans which could be a simple process, return to Implement and do a new thing, or even return to Define / Measure / Analyze)
Thanks for the great question!
Hi, could DMAIC be used as a root cause analysis method, specifically for the resolution of failures/problems/deviations not necessarily generated in a project but by normal operations within a process?
Hi Jennifer,
DMAIC is an acronym for the framework (Define, Measure, Analyze, Improve, Control). Root cause analysis is one step inside the Analysis phase.
Best, Ted.
Hi Ted,
I just wanted to let you know that while studying for my Green Belt in Six Sigma I have found this an invaluable resource that has demystified the whole concept of lean and DMAIC! I work in the intellectual disability sector where it is not the norm to apply lean / DMAIC to quality improvement, but where it absolutely can be applied to great effect. Thanks and kind regards,
Emer
Thank you so much for the kind words, Emer! We work hard to make these concepts clear and it’s gratifying to know it’s helpful!
I don’t want to presuppose, but you might be interested in a few articles that Jamie Garret contributed about how he applied Lean Six Sigma teaching – another field where Six Sigma is not traditionally applied.