In the Analyze phase of DMAIC, we want to identify the root cause of the defects that are causing variation in our process. Sometimes the culprits are easy to identify. We use the 6M’s in Six Sigma (Six Ms or 5Ms and one P or 5M1P) to find the possible root cause of the process variation or problems. More often, we have to hypothesize what is causing the variation and then test that hypothesis to see if our hunch was right. But how do you come up with a hypothesis for what is causing variation?
In Six Sigma, we describe process variation in terms of 6M’s (aka 5 M’s and 1 P). These are six elements that contribute to variation in a process. Those six elements – 5 Ms and on P (or 6Ms) influence variation in all processes – manufacturing or not.
The 5Ms and one P is a concept that is a quality management and problem-solving methodology, particularly in the manufacturing industry. They represent six potential sources of problems or causes for variations in a process. The 5Ms stand for:
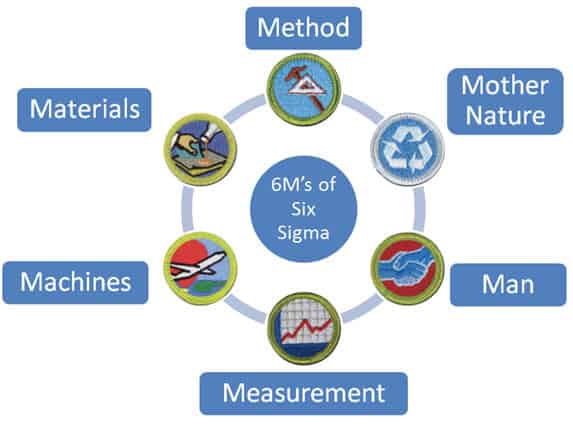
Ishikawa states the 6 Ms (also known as the 5 Ms and 1 P) as Man, Machine, Material, Method, Measurement, and Mother Nature.
- Method
- Mother Nature’s “Environmental”
- (Man) People
- Measurement
- Machine
- Materials
Let’s Takes A Look at 6M’s in Six Sigma (Six Ms or 5Ms and one P or 5M1P) Attributes
6 Ms in Manufacturing Example
- Method: Method refers to the procedures, instructions, and techniques used to carry out the process. It includes standard operating procedures (SOPs), work instructions, process flow, and overall process design.
- Following an assembly line is much different than a manufacturing floor that does not.
- (Man) People: Man refers to the human resources involved in the process, including operators, technicians, and supervisors. It focuses on the skills, training, and expertise of the people performing the tasks.
- Empowering any single employee to stop the entire production line if he finds a defect.
- Measurement: Involves the measurement systems and instruments used to assess and monitor the process. It focuses on the accuracy, precision, calibration, and reliability of measurement devices.
- If the supplier measures in English units and the manufacturer measures in metrics, issues could arise.
- Machine: Machine represents the equipment, machinery, and tools used in the process. It includes factors such as machine capability, maintenance, calibration, and reliability.
- The age and robustness of the machine may impact the process.
- Materials: Encompasses the raw materials, components, and supplies used in the process. It involves aspects like material quality, specifications, storage conditions, and handling procedures.
- Some materials are harder to work with than others.
- Mother Nature’s “Environmental”: This additional factor is sometimes included to represent the physical surroundings or conditions in which the process takes place. It includes factors like temperature, humidity, lighting, cleanliness etc
- Ambient humidity may cause more breakdowns in machines than normal.
6 Ms in Management
- Method
- If one team is developing software following a Waterfall approach while a second is using an Agile practice and a third is using Kanban, each method is different.
- Mother Nature’s “Environmental”
- Offices in the north are more lenient to snow days than those in the south.
- (Man) People
- People untrained in 6 Sigma tend to focus on the ‘Man’ portion of the 6Ms when looking at a process.
- A manager who is unenlightened in six sigma is most likely going to focus on Man. Unenlightened managers tend to think of the process performance as being influenced more by the person component than by the other five components of the six Ms of the machine, material, method, measurement, or mother nature. (Don’t ask whom, ask why.)
- Measurement
- It’s difficult to evaluate teams evenly if each team leader rewards their teams for different behaviors.
- Machine
- Software development productivity may be different if developers have slower machines or worse tools to use.
- Materials
- Employees can only build a product as good as the raw materials they get.
How to develop a Cause and Effect Diagram using 5Ms and 1P
The Cause and effect diagram is a structured graphical diagram listing all possible causes and their relationship with the main effect or problem. The diagram’s basic input is the brainstorming that pushes to identify all the possible causes rather than just more noticeable ones.
Following are the steps to draw a fishbone diagram:
1: Identify the problem:
- Identify and clearly write down the effect or a problem that needs to be analyzed
- Then create an operational definition of a problem to ensure all the stakeholders will understand it
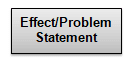
2: Determine Effect or Problem:
- Draw a horizontal line. This is a spine
- At the end of the spine, towards the right, draw a box and determine the description of an effect

3: Identify major causes contributing to the effect or a problem
- Establish main causes and write down a few main causes above the horizontal line and a few below the horizontal line. Make sure they are placed on the tail of the same arrows.
- Each cause or reason for imperfection is a source of variation. Causes are usually grouped into major categories to identify these sources of variation.
- Man/People: Anyone involved with the process.
- Methods: How the process is performed and the specific requirements for doing it, such as policies, procedures, rules, regulations, and laws.
- Machines: Any equipment, computers, tools, etc., required to accomplish the job.
- Materials: Raw materials, parts, pens, paper, etc., used to produce the final product.
- Measurements: Data generated from the process that is used to evaluate its quality.
- Environment: The conditions, such as location, time, temperature, and culture, in which the process operates.
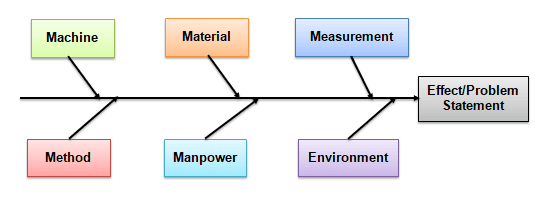
4: Identify sub causes
- Identify as many sub-causes that are relevant to the main causes
- For instance, if the sub-cause applies in multiple places, list it under each main category.
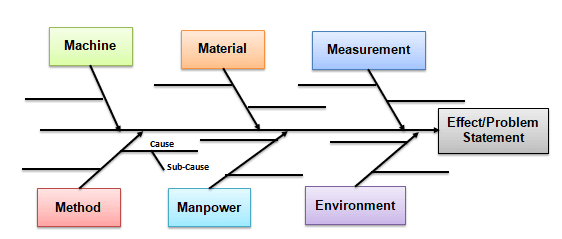
5: Analyze the diagram
- At this time, the fishbone diagram shows all the possible causes of an effect.
- Identify causes that are not impacting the effect and also identify causes that need further investigation.
- Further, perform a 5Why analysis of the identified causes (also called noises) to arrive actual root cause.
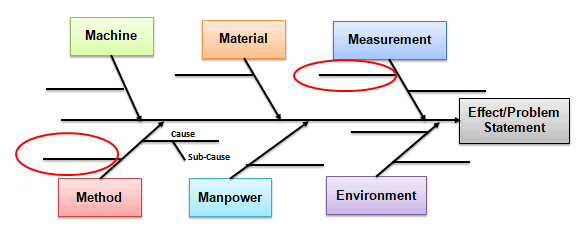
Six Sigma 5M and 1P Example
By and large, Fishbone diagrams are used to identify the root causes of a problem in the “Analyze” phase of Six Sigma’s DMAIC (Define, Measure, Analyze, Improve, and Control).
Example: XYZ is a valve manufacturing unit receiving persistent customer complaints about the valve diameter. The plant’s General Manager asked QA and Production team to conduct a root cause analysis. So, the team performed Brainstorming and drew the Cause and Effect diagram to identify all the possible causes.
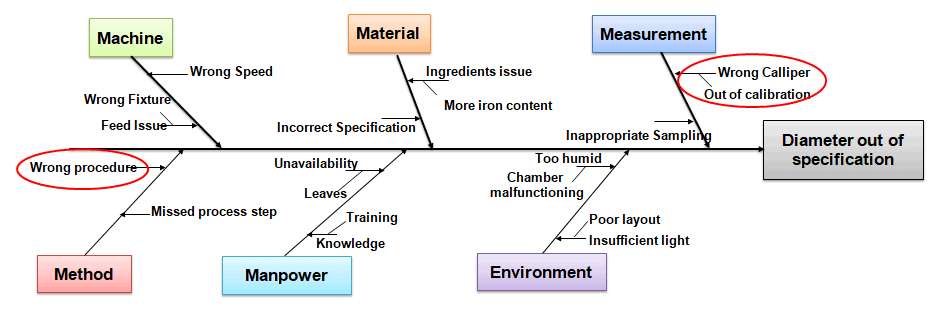
The team identified that the wrong caliper and wrong procedures were the probable causes. Further, the team has to perform a 5 Why analysis to identify the root cause.
6M’s in Six Sigma (Six Ms or 5Ms and one P or 5M1P) Template Download
Benefits of 6M’s in Six Sigma (Six Ms or 5Ms and one P or 5M1P)
- The framework helps in troubleshooting, root cause analysis, and implementing effective corrective actions to improve quality, productivity, and overall performance.
- Further, it graphically displays all the possible causes related to a problem to discover the root causes.
- Helps the team to focus on the problem and brainstorm until the elimination of the root cause.
- Easy to implement in any case.
6M Insights
- When you have a bell-shaped curve, none of the 5 Ms or one P are unduly influencing the process.
- Six elements contribute to variation in a process. Those six elements – 5 Ms and on P (or 6Ms) influence variation in all processes – manufacturing or not.
- You could also use the 6M approach as a spine on each of the fishbone diagrams and then ask the 5 whys to narrow down the potential root cause.
Comments (6)
Variation by Method -Drilling can be done in single/multiheades machines or in a modern CNC machine. Based on your product cycle you can choose a method wherein which variation & cost to be considered
Variation by men performing the operation will come thro. his skill/experience level he got with
Thanks for the addition! Much appreciated.
Hi
I’ve heard it before; 5 M
Mother nature use for outdoor workshop and indoor you can Control Envioment.
Thanks, Larry. That’s a neat variation I haven’t heard of before.
Thank you for the concise 6M analysis method summary. On another note I see that you used Boy Scout merit badges as visual inserts haha.
Hah! You noticed!! Glad it was helpful, Kenneth!