Tires have come a long way since they were used 100 years ago. However, there is still a need for continuous improvement in their design to make them more useful and reliable. To achieve this, tire companies use various tools and methods, including the Six Sigma DMAIC methodology. An Indian tire manufacturer, Apollo Tyres Limited, has studied implementing Six Sigma to improve its process quality. A recent Tire Manufacturer Sigma Six Case Study focuses on reducing the process variations of bead splice, which causes wastage of material. The case study shows how to implement the DMAIC methodology to achieve this goal.
In 2017, Vikash Gupta wrote a study as a requirement for his Master of Technology degree in Industrial Engineering at Malaviya National Institute of Technology Jaipur. The researcher collaborated with Islamic Azad University (IAU), Tehran, to publish the study in the Journal of Industrial Engineering International.
The study aimed to analyze and assess a tire manufacturer’s current processes, determine its capabilities, and improve them using the DMAIC methodology.
This tire manufacturer lean sigma six case study explains how Apollo Tyres Limited implemented the Six Sigma DMAIC methodology.
The Application of Lean Six Sigma Methodology for a Tire Manufacturer
Apollo Tyres Limited researched to improve its process efficiency using Six Sigma.
The team uses “Process Capability” to analyze how well a process works by using statistical tools like the normal curve and control charts. This analysis is done by combining data and engineering judgment. The results help them improve their design, planning, and evaluation techniques. By using process capability, they can also improve the design of machines and reduce defects during production.
Once they decided on what to study and how to do it, they began using the DMAIC cycle. This method helps identify and eliminate unnecessary steps and find ways to improve the process in many industries. Specifically, this research aims to reduce process variations and improve decision-making by creating a system where everyone in the company collects and analyzes data organizationally.
Each step of DMAIC used both qualitative and quantitative techniques. First, they tested the data to ensure it was normal and then calculated the process performance capability index (Cpk) to measure the performance of the process. The information helped the team establish a baseline for the system and identify areas to improve.
DMAIC Phases: Tire Manufacturer Lean Sigma Six Case Study
Here is the six-step approach followed in the research:
Define Phase
The team set goals to improve the bead splice process in the define phase. First, they found a problem by looking at what customers said (VOC data). Customers reported excessive material waste due to inconsistent product assembly, costing the company money. They discovered that the way the product was assembled was causing a problem. To solve it, they needed to make adjustments to use more material.
Measure Phase
In the measure phase, the researchers wanted to create a system to measure how well a process works. To do this, the team used the process capability index ( Cp & Cpk). First, they looked at the variation in the bead splice and used a MINITAB program to analyze it.
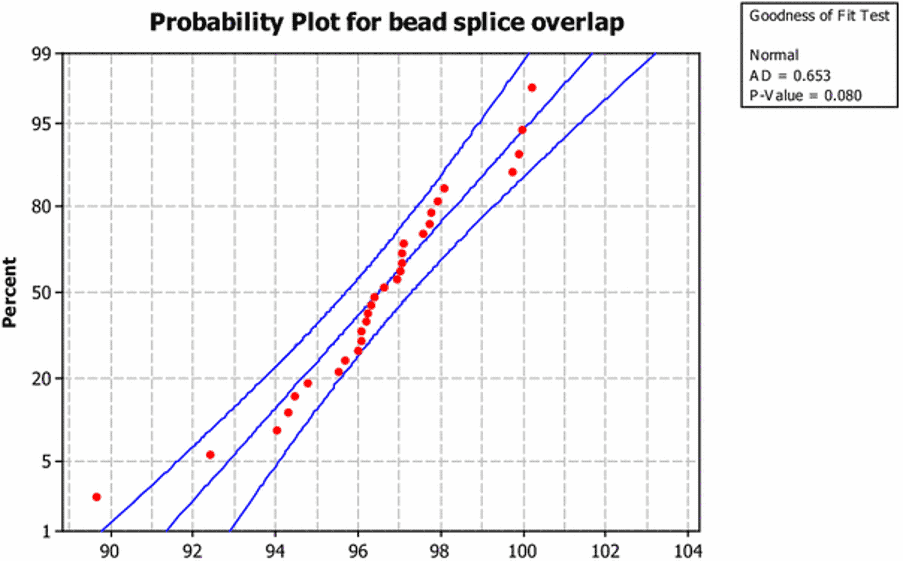
The research found that the Cpk value was 0.94 and the Ppk value was 0.82, less than 1.33. This means the process could be performing better. They also examined the relationship between the sigma level and the process capability indices.
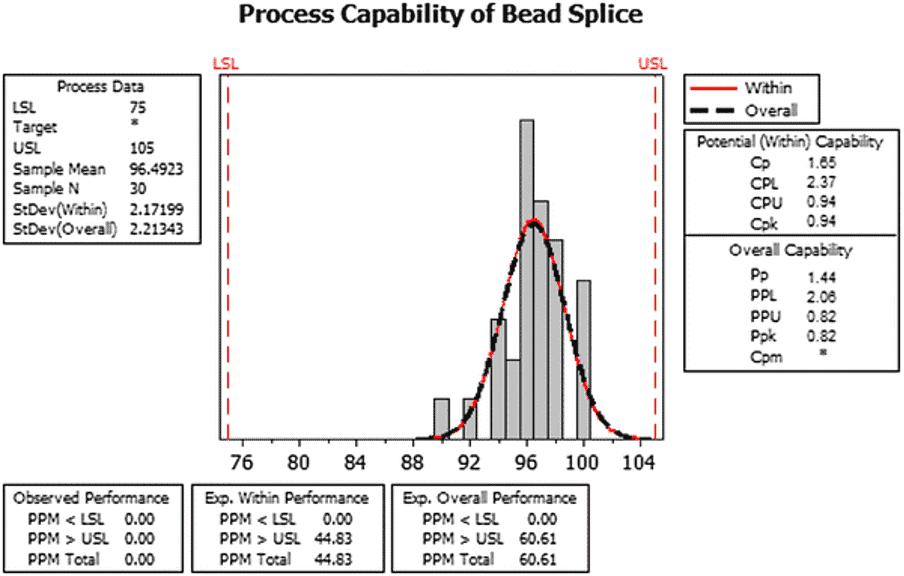
The team used this information to create a system performance evaluation starting point. Again, this was based on the improvement areas they identified in the planning phase.
Analysis Phase
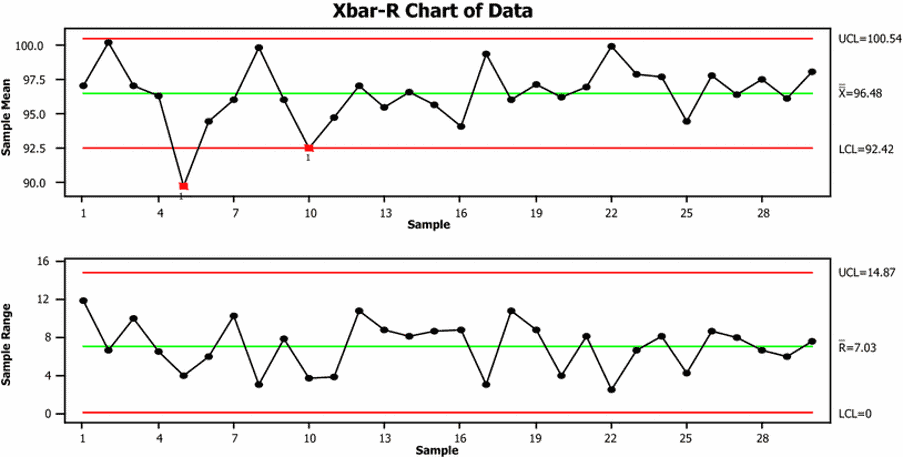
In this step, they looked at the data and made charts to help them understand it better. Then, they used six-sigma quality tools to determine how well things were going. Then, they dug deeper into the data to find out what was causing any problems. To do this, they used the Ishikawa diagram.
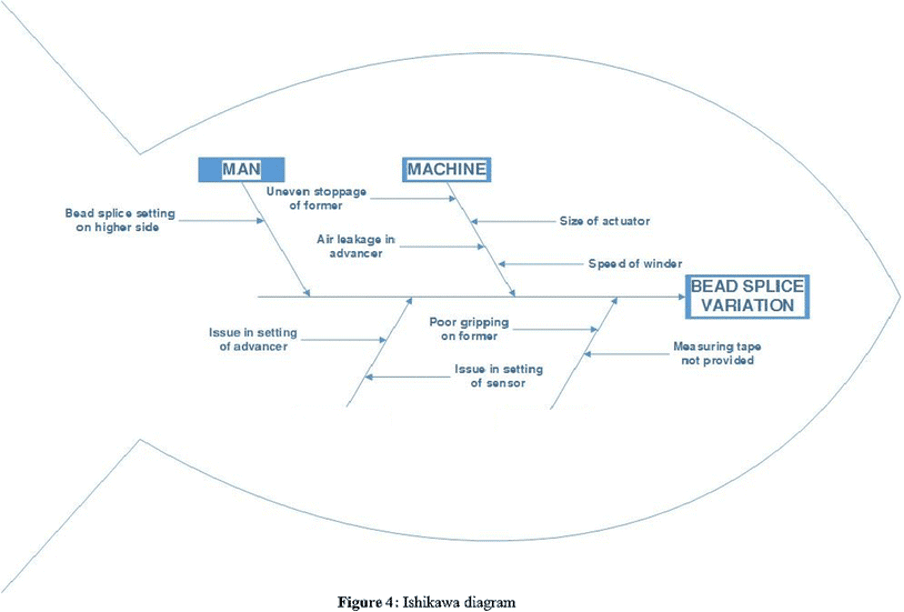
The was discovered that:
- The bead splice setting was too high because the tape slipped from the gripper. This happened because the gripper key was worn out.
- The advancer setting varied because different workers had different skills. There needed to be standard guidelines to follow.
- The sensor setting needed to be adjusted frequently because the diameter of the material changed, but there were no guidelines for how often to do this.
- The last cause was that the workers were not using measuring tape.
Improve Phase
During the improve phase, the team searched for new and creative ways to improve things faster and cheaper. They tried different approaches and suggested statistical methods for continuous improvement.
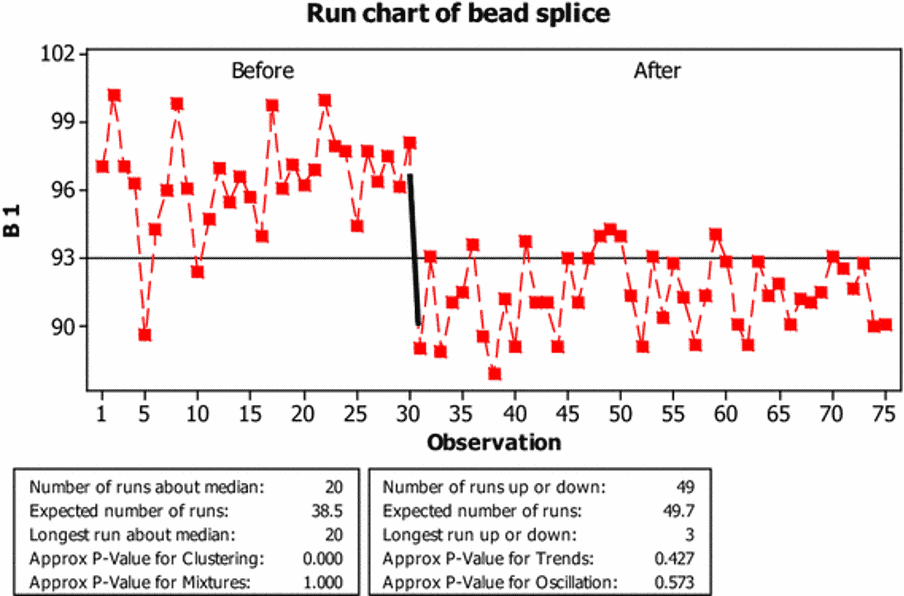
They calculated the process capability index, which measures how well the process can produce good results. After making improvements, the capability index value improved to 2.66, which means the process can now have good results.
Control Phase
To keep the tire manufacturer’s company successful, it’s important to continue the progress made in earlier steps. The control phase helps maintain these improvements in the screening process, ensuring that the organization maintains its high sigma quality level.
After obtaining the result, the first step is to evaluate whether the root cause has been reduced and if there has been any improvement in the sigma level. Additionally, it is important to identify any further actions that may be required to achieve the ultimate goal. It is crucial to take note of the lessons learned during the process and apply them in future endeavors. Finally, it is essential to determine the next steps and plan the remainder of the process accordingly.
Tire Manufacturer Lean Six Sigma Case Study Conclusion
This study uses the six-sigma DMAIC quality method to help decide how to fix a specific problem. It aimed to improve the way the bead splice process works, and this was achieved. The Cp was raised from 1.65 to 2.95, while the Cpk value was increased from 0.94 to 2.66.
This lean sigma six case study found that using the DMAIC methodology can greatly improve a tire manufacturer company’s work. This thesis’s research is not just about tire manufacturer companies but can also apply to other companies.