Introduction to Lean
First, what is lean? Lean is about delivering value to your clients with the help of minimum organizational resources. We’ll learn more about Lean geared to help you pass your Six Sigma certification exam.
Basically, the goal of a lean organization is to enhance customer value by mitigating waste from its processes and procedures. It generally means working smarter and not harder for your team and your processes. You can use lean techniques like Value Stream Mapping, 5s, and Poka Yoke to improve your customers’ cost, quality, and service delivery.
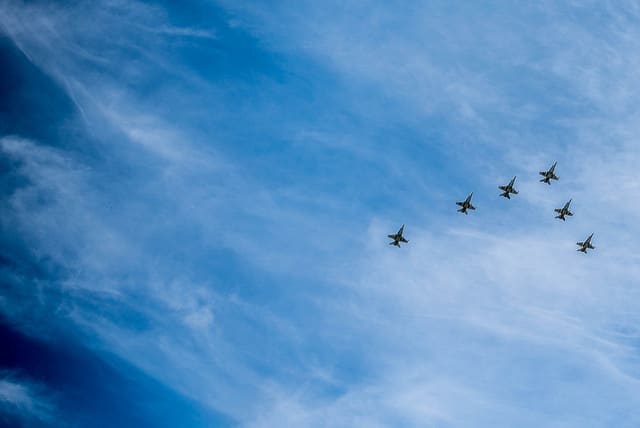
Why is Lean Important?
Lean is about just-in-time processing. Hence, the materials, information, and work arrive as the customer needs. There is a little stockpiling ahead of time as possible. In a manufacturing environment, the raw materials arrive at the plant at exactly the right time. Accordingly, the manufacturer moves the materials to the assembly line quickly. The goal of lean is to avoid having input sitting around waiting to be used so that there is as little output as possible beyond what customers have ordered.
The Lean Philosophy
The Lean philosophy focuses all efforts and resources on creating value-added activities for the end customers. Therefore, lean is about just-in-time processing. The materials, information, and work arrive right on time. There is a little stockpiling ahead of time as possible. In a manufacturing environment, the raw materials arrive at the plant at exactly the right time. The manufacturer then unloads and moves the materials to the assembly line as quickly and in as short a path as possible. Moreover, lean handles the movement of raw materials between different processes in such a manner to avoid any waiting time and overpiling of work in progress.
Principle of Flow in Lean Manufacturing
In a Lean system, flow refers to the smooth and continuous work movement through a process, with minimal interruptions or delays. In other words, it refers to how individuals or objects move from one step to another from starting to ending the process.
Optimizing flow is a key principle of Lean that helps organizations to create value more efficiently, reduce waste, and deliver high-quality products and services to customers. In other words, the target is to move the product as quickly as possible without affecting customer satisfaction or quality.
To achieve a smooth flow, Lean emphasizes eliminating waste and reducing variability in the process. By identifying and eliminating these sources of waste, Lean seeks to create a more streamlined process that can deliver value more quickly and with less effort.
How to Improve the Flow
Organizations follow a systematic method to improve the good flow within their processes:
- Map the entire process
- Categorize and record all issues faced by the process owners
- Find all the waste in the current process
- Map an ideal state using lean principles to achieve a flawless process
- Create an action plan
- Periodically monitor the new processes with the help of key performance measures.
By improving the good flow in manufacturing, the productivity and quality of the individuals improve. It then becomes possible to increase business and also helps optimize the resources.
Steps for a Lean Project
Organizations can use the following steps to foster lean philosophy:
- Specify the requirements of the customer value. The organizations can basically define and establish customer value using tools like:
- CTQ tree
- Quality Function Deployment (QFD)
- Identification and elimination of Muda from the value stream of each product family: In this step, you must identify the value stream of each product family and the value-added steps and non-value-added activities. The organization must look for steps to reduce wastage and non-value-added activities to focus on improving customer value.
- The focus should be on shortening the throughput times by creating a flawless and continuous flow among the value-added activities and processes. To achieve this, organizations can utilize the one-piece flow technique.
- Design a pull value system in which the customer demand originates a signal, and accordingly, the tools are available to be moved to the next process. Likewise, this means that customer demands dictate the material flow between different processes.
Example
- Think of the coffee made at Starbucks as a simple example of a pull-lean manufacturing system. Starbucks never makes the finished coffee in advance; they begin the process only when the customer orders. All the coffee-making steps begin only after the customer signals the demand. If Starbucks produces coffee in advance, thinking about reducing the wait time during peak hours would be highly costly and impractical for the company.
Following these steps would help the organization reach high levels of efficiency and effectiveness by delivering enhanced customer value and mitigating Muda (waste).
Origins of Lean
The “Big Picture” was created by Womack. All about VALUE!
Great LEAN Six Sigma Presentation by MIT
A Lean Framework.
Good Lean Overview Video
Also, See:
Recommended Lean Overview Reading List:
- Lean Thinking: All businesses must define the “value” that they produce as the product that best suits customer needs. The leaders must then identify and clarify the “value stream,” the nexus of actions to bring the product through problem-solving, information management, and physical transformation tasks. Next, “lean enterprise” lines up suppliers with this value stream. “Flow” traces the product across departments. “Pull” then activates the flow as the business changes to the pull of the customer’s needs. Finally, with the company re-engineered towards its core value in a flow process, the business reorients towards “perfection,” rooting out all the remaining Muda (Japanese for “waste”) in the system.
- The Lean Six Sigma Pocket Toolbook: Blends Lean and Six Sigma tools and concepts, providing expert advice on determining which tool within a “family” is best for different purposes. Packed with detailed examples and step-by-step instructions, it’s the ideal handy reference guide to help Green and Black Belts move from the classroom to the field.
ASQ Six Sigma Black Belt Exam Lean Overview Questions
Question: A system that delivers products or services at the correct time and in the correct quantities is referred to as: (Taken from ASQ sample Black Belt exam.)
(A) takt time
(B) kaizen
(C) just-in-time
(D) single-piece flow
Answer:
Just-in-time. That just-in-time system is the ultimate goal of Lean, a process with zero waste. Takt time is a calculation used to synchronize supply with demand. You have to calculate a Takt time to achieve just-in-time production, but it’s not the best answer. Kaizen is a system for incremental improvement. Single-piece flow is a process for producing a finished product in a streamlined fashion.
When you’re ready, there are a few ways I can help:
First, join 30,000+ other Six Sigma professionals by subscribing to my email newsletter. A short read every Monday to start your work week off correctly. Always free.
—
If you’re looking to pass your Six Sigma Green Belt or Black Belt exams, I’d recommend starting with my affordable study guide:
1)→ 🟢Pass Your Six Sigma Green Belt
2)→ ⚫Pass Your Six Sigma Black Belt
You’ve spent so much effort learning Lean Six Sigma. Why leave passing your certification exam up to chance? This comprehensive study guide offers 1,000+ exam-like questions for Green Belts (2,000+ for Black Belts) with full answer walkthroughs, access to instructors, detailed study material, and more.