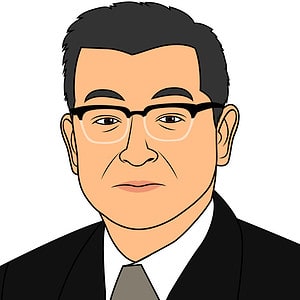
Kaoru Ishikawa is considered the Father of Japanese Quality. He invented the Fishbone diagram (aka 4M/5M or cause and effect diagram) and CWQC – Company Wide Quality Control. He also sponsored the concept of “next operation (process step) as the client” to avoid workplace politics.
Kaoru Ishikawa Biography
The oldest of eight sons, Kaoru was born in 1915. He went to the University of Tokyo and received an engineering degree in applied chemistry. After working at Nissan until 1947, Kaoru started as an associate professor at the university where he went to school. Then in 1978, he assumed the presidency of the Musashi Institute of Technology. Many industry experts and historians consider him to be instrumental in the development of quality initiatives in Japan, notably of which is the quality circle. He also created the Ishikawa (fishbone diagram), which Six Sigma Practitioners widely use today when analyzing industrial processes.
Quality Control and Process Efficiency Philosophy
Ishikawa spent his life trying to make people think differently about the way they work. When management became complacent, he argued for continuously improving the quality of their products. He always said that you can take those improvements and go one step further. He believed that you should service your customers even after they have bought the products.
Kaoru Ishikawa noticed that a lack of internal coordination in the operations affected a customer’s needs. Improved cooperation led to better quality & process efficiency. His “the next process is your customer” policy refers to a desire for better cooperation among a company’s internal departments. “Do it right,” “zero defects,” and process efficiency are all parts of that statement.
He was a strong believer that top-level personnel had to support the team under their control all the time. He felt that if top-level management did not take quality control courses, those programs would not succeed.
Dr. Ishikawa followed other quality control believers as well. One of those was W. Edwards Deming, the creator of Plan-Do-Check-Act model. As a matter of fact, he expanded that into a 6-step plan from the original 4-steps:
- Determine goals and targets
- Determine methods of reaching those goals
- Engage in education and training
- Implement the work
- Chuck the effects of implementation
- Take appropriate action
Awards
He has received many awards and among them are the Shewhart Medal for outstanding technical leadership in the field of modern quality control and the Order of the Sacred Treasure (Japan) for outstanding technical leadership in the field of modern quality control. The ASQ has also recognized him as an influential person in the field of quality control. They awarded him the Industrial Standardization Prize for writings on quality control, the Nihon Keizai Press Prize, and the Grant Award from the American Society for Quality Control for his educational program on quality control.
Dr. Ishikawa is widely recognized as one of the leading authorities in quality control techniques and training. His methods have been utilized by Komatsu, Bridgestone, and IBM just to name a few. He has shown them how to manufacture better quality products at a lower cost factor. “What is Total Quality Control? The Japanese Way” his book from Prentice Hall, Inc. was a best seller in the business sector.
Dr. Kaoru Ishikawa highly believed in the strength of six quality tools:
- Control chart
- Histogram
- Flow chart
- Run chart
- Scatter diagram
- Pareto chart
Dr. Ishikawa’s Timeline:
1915 – Born on July 13th.
1939 – Graduated in applied chemistry from the University of Tokyo
Worked in coal liquefaction, where he got experience in design, construction, operations, and research.
1939-1941 – Naval Tech Officer overseeing 600 workers constructing a factory which he said was invaluable in his QC career later in life.
1947 – Became a researcher at the University of Tokyo where he began studying statistical methods.
1949 – Joined JUSE QC research where he became an instructor.
1952 – Became the Chemical Society of Japan’s Director.
1960 – Received his promotion to professor and his Doctorate of Engineering at the Musashi Institute of Technology.
1969 – Became a member of the ISO, Japan.
1970 – Began having quality control training seminars. Worked with Ford, the American Society for Quality Control, and thousands of other companies.
1977 – Chairman of ISO, Japan.
1981 – Executive member of ISO and published ”What is Total Quality Control? The Japanese Way”, first edition.
1989 – Died on April 16.
Kaoru Ishikawa and Quality Control
Dr. Ishikawa believed that company-wide quality control did not just mean the quality of the product being sold. It also included the quality of the management, the company itself, after-sales service to the customer, and the human beings involved. He strongly believed that if all these things came together, then the company would see the following:
- Reduced costs
- Reduced wasteful reworks
- Improved reliability of goods
- Increased production
- Expanded market for sales
- Decreased reporting in false data and reports
- Reduction in poor product quality & defects
- Better relationships between departments
- Improved human relations
- Meetings run more smoothly
- Establishment of better operating techniques
- Testing and inspection costs drop
- Vendor and vendee contracts better
- More democratic discussions
- Fewer equipment repairs and installs done
Dr. Ishikawa was a tireless leader who saw opportunities to make things better and went after them. He lived a full life, and he has helped many companies around the globe create a better workforce who can and do accomplish more than they ever thought possible.
Comments (7)
this article helped me a lot to answer my assignment
Glad to hear, Carlos!
What are the 6 fundamental principles of total quality control by Kaoru Ishikawa?
Hi Martini,
To be honest, I never heard of Total Quality Control until your question. The only thing that I can find on it is here, which is based in the 4 steps of Plan, Do, Check Act.
You may also be interested in my Total Quality Management article found here.
Best, Ted.
Total Quality Control was part of Dr. Ishikawa’s book title, first published in 1981 (per the article above).
my question is the contribution of ishikawa to quality management
Did you read the article above, Ileni?