The healthcare industry has been exploring the benefits of RFID-embedded technologies, particularly in improving supply chain performance measurements. This is critical for hospitals, where patient safety and flows are key operational efficiency measures. Hospitals must address process bottlenecks to ensure timely discharge times, higher costs, and higher quality of service. Failure to do so can impact their overall business performance. Hospitals can use RFID technology to optimize technology spending and reduce costs. This can address the issue of suppliers and operational expenses. RFID data can also be a valuable component of Six Sigma DMAIC applications.
Six Sigma DMAIC has become a popular methodology for improving process performance in various industries, including Healthcare. The methodology addresses common challenges such as reducing waiting times, increasing capacity, and deploying resources effectively. Hospitals can achieve cost savings and process improvements by using RFID technology. This involves eliminating non-value-added activities such as locating supplies and equipment and preventing postoperative infections.
This case study used the Six Sigma approach and various analytical tools to examine the effectiveness and efficiency of RFID technology in outpatient surgical processes. In 2012, a study published by Peter B. Southard, Sameer Kumar, and Charu Chandra showed that RFID technology reduced costs and time for outpatient surgical procedures in hospitals.
The research methodology chosen for this study includes DMAIC and simulation, which are well-suited to examining complex interrelationships between tasks and the stochastic nature of those tasks. Here is an overview of how the authors implemented the Six Sigma methodology of DMAIC.
The Application of Six Sigma DMEDI Methodology and Simulation In Implementing RFID in Healthcare
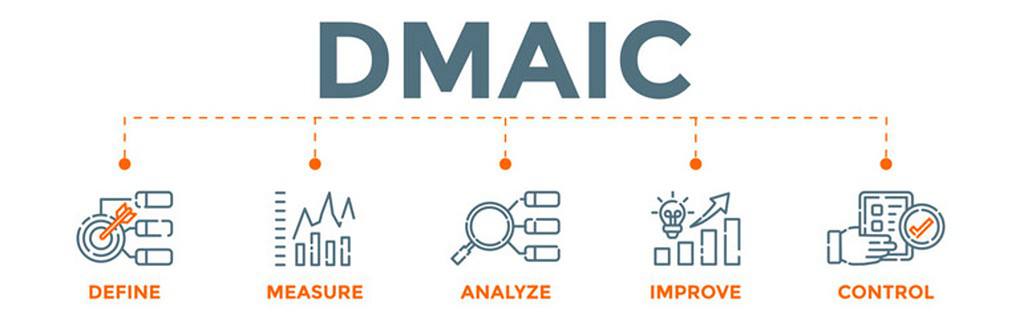
The use of Six Sigma DMAIC methodologies and tools by businesses to identify and reduce the root causes of variation in processes and systems has been well-established. This study applies the primary Six Sigma methodology, the DMAIC cycle, to reduce variability in healthcare processes.
In addition to DMAIC, this study also uses discrete event simulation, a process improvement tool, to examine the impact of radio frequency identification (RFID) technology on improving the effectiveness (quality and timeliness) and efficiency (cost reduction) of healthcare service delivery.
The objective of the case study is to generate further quantitative proof regarding the advantages of incorporating RFID technology in healthcare operations. It also aims to address the research query of whether RFID improves the effectiveness and efficiency of dispensing services in healthcare frameworks. The study is limited to regularly scheduled hospital outpatient surgery but provides a representative example of a typical healthcare delivery process.
The healthcare industry six sigma DMAIC study uses Arena, a computer simulation package, to model the existing process and the process with RFID technology implemented, with the main dependent variable being the overall throughput time. They obtained the arrival and processing times for individual processes from publicly published sources or through personal interviews with managers and staff from local hospitals.
After deciding on the project and research, the authors used the DMAIC cycle to move forward. Here’s how they did it!
DMAIC Phase: Healthcare Industry Sigma Six Case Study
Define Phase
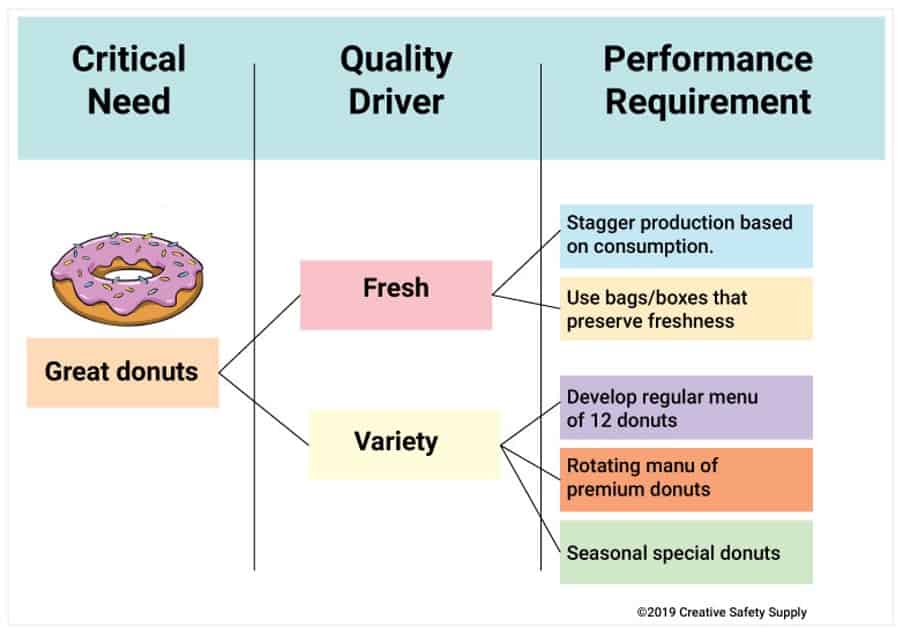
The Define phase aims to identify system characteristics that are Critical to Quality (CTQ) of the customer. For this study, the authors looked at a hospital’s outpatient surgery system, when patients come in for surgery but don’t have to stay overnight. The objective was to determine what causes mistakes and delays and what is needed to make the surgery happen. They also wanted to understand the costs involved.
The healthcare Industry Six Sigma DMAIC study focused on a real outpatient surgery center in Minnesota that performs around 12 different types of surgeries on approximately 7,800 patients per year. Some surgeries include eye, vein, hernia, nerve, foot, shoulder, knee, breast augmentation, plastic surgery, liposuction, and hand surgeries. The surgery center has 12 primary care doctors, 12 surgeons, 7 technicians, and 22 nurses to help out. They also have 10 operating rooms, 6 exam rooms, and 10 beds for recovering patients.
Measure Phase
The authors must first determine how to measure what they have now to improve things. This helps them make a plan to improve. So they looked at a few things, such as:
- How long it takes to do each task
- How long it takes to do the whole process
- How much money it costs to do the process
- How resources are used
- How many mistakes are made
During the measure phase, the team created a “current-state value stream map” (csVSM) to understand the improvement processes. This map looked at how things work in a hospital system. It showed that some big problems needed fixing, like wasting time looking for equipment and supplies and mistakes that happened during surgeries because of bad procedures or sterilization. To fix these problems, they decided to use RFID technology.
Analyze Phase
The DMAIC analysis phase aims to uncover the causes of variation and errors in a process and subsequently determine their root cause. To achieve this, a comprehensive understanding of the process, including its current performance, expected performance, capabilities, and required controls, is crucial. This study employed various six sigma tools to facilitate the analysis process.
The healthcare Industry Six Sigma DMAIC study used process mapping and discrete event simulation tools to analyze process variation and the impact of introducing RFID technology to reduce it. Process mapping involves creating a diagram of the individual tasks involved in transforming inputs into the desired output, i.e., the service. As previously discussed, this technique is also a fundamental component of value stream mapping.
The team also describes potential failures in outpatient surgery and measures to prevent mistakes using RFID technology, such as tagging equipment and patients with RFID chips. For instance, using an RFID wristband on patients eliminates the need for physical scanning each time identification is required, and a pharmaceutical ID with an RFID tag is used to purchase post-operative medications.
The authors examine the effect of implementing these measures on reducing patient misidentification, lost equipment, and complications due to fatigue, sterilization issues, or training, modeling the time savings and reduced reentry of patients into the system from postoperative infections. RFID technology helps prevent these failures by facilitating supply and equipment location through a hospital’s wireless network system and reducing complications caused by post-operative infections.
A simulation model is created to evaluate the implementation of RFID, using parameters based mainly on literature from documented empirical studies of similar systems. The model assumes that RFID significantly improves the coordination and visibility of the processes required to complete an outpatient surgical system, thereby reducing the need for additional processes associated with finding supplies.
Improve Phase
This phase of DMAIC aims to make changes to improve the system. In this study, the researchers simulated using radio frequency identification (RFID) technology in their study processes. They based these improvements on previous studies that showed the benefits of RFID. The researchers analyzed the costs and time savings and did a cost-benefit analysis. They also checked for any risks by doing a sensitivity analysis.
The researchers compared two models. First, they showed the total and average cost and time per patient with and without the RFID system. They also broke down the costs by value-added and non-value-added processes. For example, they considered any waiting time non-value added, except for moving the patient and searching for supplies. The team also showed how they accumulated costs by distinguishing between hourly and per-use payments for resources.
They divided the time per patient into value-added, non-value-added, and wait time categories. Value-added time was when the patient was involved in a value-added process, and the same for non-value-added time. Wait time was when the patient waited in a queue. Finally, they summarized the costs and times.
The researchers created a Future State Value Stream map. It showed that they eliminated the non-value-added activity of searching for supplies and equipment. They also eliminated the loop created by preventable postoperative infections. The RFID system ensures proper sterilization between each patient and procedure.
Control Phase
During the Control phase of DMAIC, the authors ensure the changes are kept in place. The hospital can’t go back to doing things the old way. To do this, they must create rules and procedures to keep everything running smoothly. They also need to keep an eye on key measurements to make sure they stay at acceptable levels.
RFID technology can help with this. It can collect and report information quickly to see what’s happening in real time. This is important for six sigma processes, which emphasize the need for immediate feedback and transparency.
Healthcare Industry Six Sigma DMAIC Conclusion
The case study examined whether using RFID technology in outpatient surgeries could help track patients, equipment, and supplies and reduce errors and infections. Using the DMAIC methodology, the study found that implementing RFID technology could reduce non-value-added activities and process variation. For example, using RFID technology could greatly reduce the time spent searching for supplies and equipment, reducing process variation and preventing post-operative infections. The study estimated that using RFID technology could save $1.93 million annually and reduce patient wait times by 1.1 hours.
The study recommends using RFID technology to avoid patient mix-ups, miscommunication, inaccurate medication, and knowledge errors. The improved value stream process map with RFID implementation eliminates non-value-added activities and complications in recovery. However, implementing RFID technology requires involvement from clinical staff and cost-benefit analysis to ensure success. Neglecting to involve physicians and senior hospital leadership could have negative consequences. Overall, investing in RFID projects can lead to significant cost savings, improved business processes, and better patient outcomes.