Cellular Systems is a kind of Lean approach that seeks to achieve efficiencies by leveraging the similarities between production units. It is an application of group technology in which dissimilar machines have been aggregated into cells, each of which is dedicated to the production of a part family.
The basic advantage of a cellular system is that a large manufacturing system can be decomposed into a smaller subsystem of machines called cells.
The cellular manufacturing system layout is based on recognizing similarities in geometry, material, size and manufacturing process etc. Every cell contains a group of machines to produce the family of parts. Cellular manufacturing allows us to shorten lead time and become more productive.
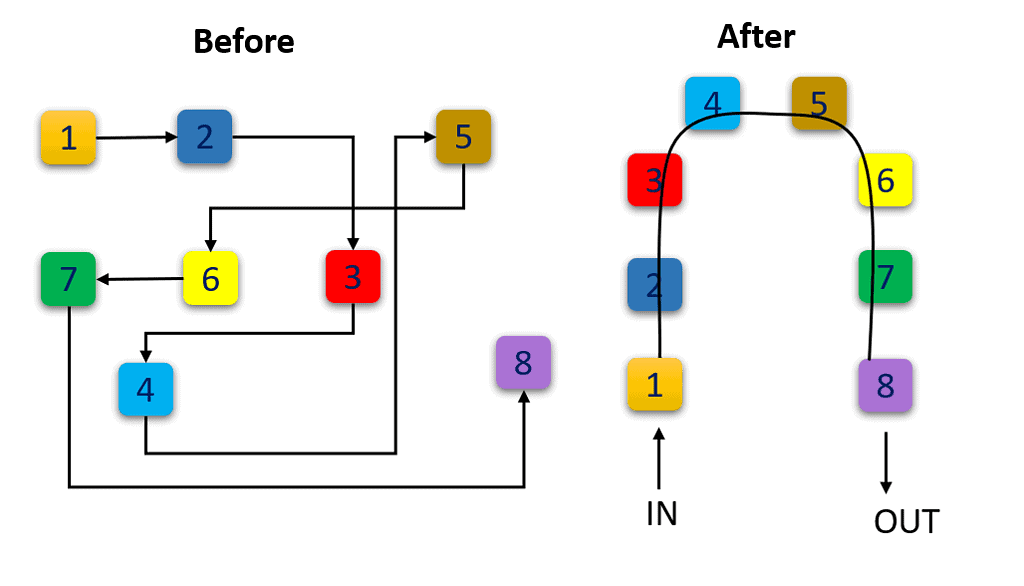
History of Cellular Systems
Cellular manufacturing was first introduced by Ralph Flanders in the year 1925. The concept is becoming famous after 1970, and evolved as part of lean concepts. In Japan during1990s, cellular manufacturing is one of the influential concepts in lean, including just-in-time (JIT) manufacturing.
Further, the long production lines at Toyota were wrapped using a cellular layout that facilitates lean manufacturing. This increases the efficiency of the workers operating multiple machines at a time. The Toyota Production System (TPS) practices the oneāpiece flow. In other words, produces one piece at a time opposed to mass production. Toyota places a single piece between different workstations with the advantage of the least variance in cycle time and minimum waiting time. This would help to facilitate an optimum balance between different operations and mitigate over-production.
The goal of cellular manufacturing is the aggressive minimization of waste, to achieve maximum efficiency of resources.
What are ‘part families?‘
A ‘part family’ is a collection of parts which are similar either because of geometries or similar processing steps in manufacturing. In other words, arrange parts/amities where each part family possesses similar design and/or manufacturing characteristics. Characteristics in classifying parts are known as attributes.
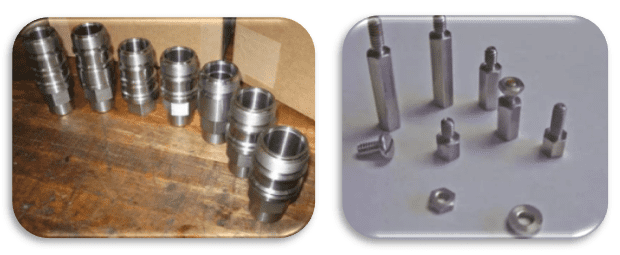
Cellular Systems Design
- Group Products: Similar products are collected “Grouped” instead of being treated as individuals and established product families. These cells produce similar products or a family of parts. Decide which products or product families will go into the cells, and determine the type of cell.
- Establish takt time: Takt time is the rate at which an organization needs to complete the production process in order to meet customer demand.
- Takt time = Net available time for production / Average customer demand
- Review the work sequence: Team to use process mapping to understand of each process step and work sequence. This will help to compute the number of machines and resources required and also help to understand the tooling requirements.
- Combine work elements to balance the process: Identity work elements and corresponding time to make each part. Furthermore, capture the time needed for each step individually multiple times and use the lowest repeatable time. Then, determine if the machine within the cell can meet takt time, here, make sure to consider the machine downtime, changeover time, etc.,
- Design the cell layout: The technique of arranging operations and people in a cell (U-shaped, etc.) instead of a straight assembly line for better utilization of people and improved communication. The physical location of machines should correspond to the work sequence. Always limit the space between processes within a continuous flow to eliminate motion waste and prevent unwanted WIP accumulation.
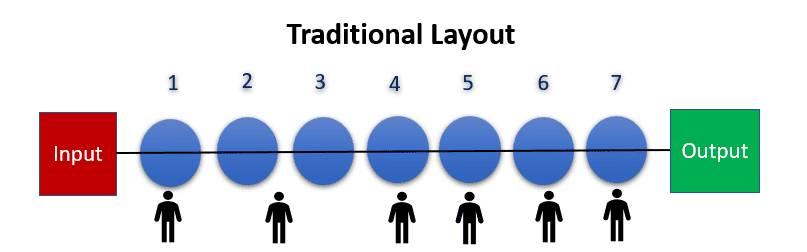
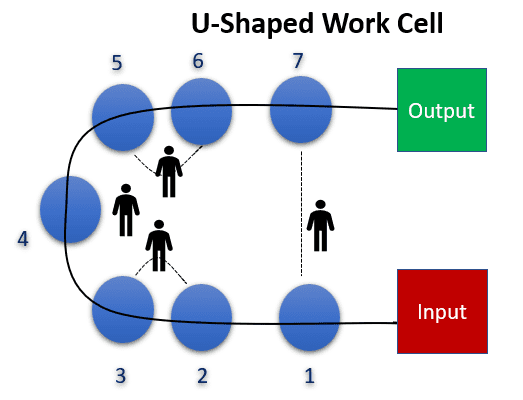
Improved layout in U-shape, operators have better access and optimized the resources efficiently.
How Many Operators are Required?
Once the layout finalizes, balance the cell and create standard work or work instructions for each operator within the cell. Then, identify the number of operators required for production to meet takt time and then split the tasks between the operators.
Optimum # operators = Sum of Operator Cycle Time / Takt Time
Types of Cellular systems layouts
The main idea of cellular systems layouts is to recognize similarities in geometry, material, size and manufacturing process, etc, and arrange the machines or workstations to optimize the production process. There is various type of cellular system layouts, and organization selects the layout based on product and process.
I-Shaped
I-shaped cell also known as a linear cell, where the workstations are arranged in a linear design. The liner cell design suits where the sequence of operation is in one direction and no back-and-forth travel between workstations.
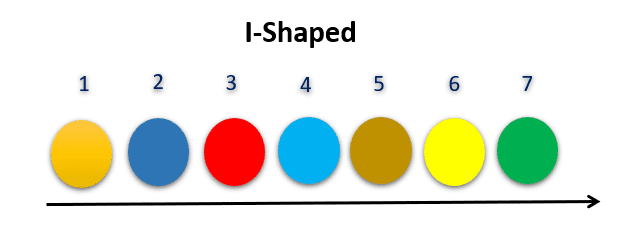
U-Shaped
As the name indicated, the cell looks like a U-shape. This is one of the most common cellular layouts. U shape design is the most compact and less traveled distance between the workstations. It also acquires the most effective communication between the operators than the other cell designs.
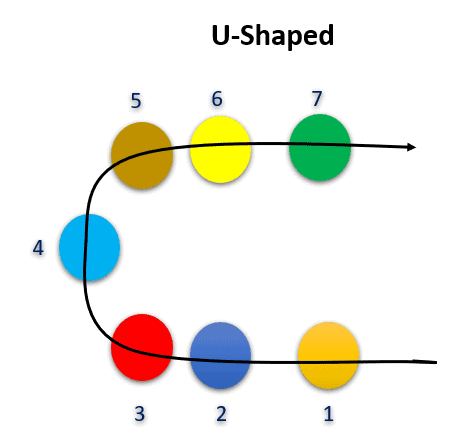
O-shaped
O-Shaped also called cage design as the shape consists of a circle or square. This design suits where the product requires multiple repeat steps. In cage design, an operator manages multiple machines in the cage.
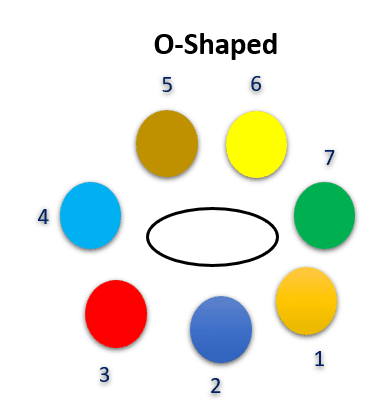
T-Shaped
T-shaped cells are used in organization where production or assemblies requires raw materials from various sources. The cell layout looks like a T shape.
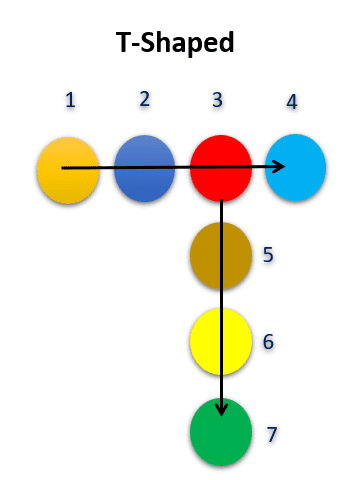
S-Shaped
In a manufacturing unit, S-shaped cells are used to work around the obstruction. On a shop floor, it is impractical to move the large machines may be due to electrical or plumbing issues, such instance, s or z shape cell act as U-shape or I-shape cells.
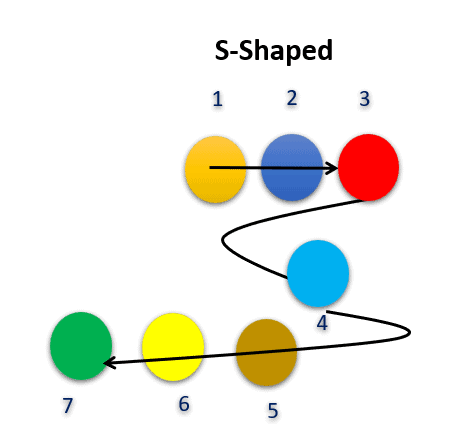
Characteristics of Cellular Systems
- The ideal cellular design is a Counter-clockwise U-shape cell.
- The aim of cellular systems is production meets the takt time.
- Machines in order of process to maintain minimum inventory between operations.
- Multi-process-handling workers. Design the cellular system so that workers can handle multiple machines in the process
- Materials-Use Kanban to regulate parts replenishment and also use gravity to move parts and materials where possible. Furthermore, keep a dedicated location for stock.
- Work Stations- Optimize bench height and maintain adequate light. In a cell, arrange equipment and workstations close together in a sequence of processing steps. Make sure to design the layout to minimize travel and eliminate surfaces where things can accumulate.
- Human Movement- Design the layout in such a way that worker movements follow a rhythm and address ergonomic issues. Reduce unnecessary walking and transport to promote flow and avoid sharp turns in the cells.
Advantages of Cellular Systems
- Reduces work-in-process inventory
- Better use of human resources
- An operator can handle multiple machines
- Increases equipment & machinery efficiency
- Less setup-time
- Better scheduling, easier to control and automate
- Reduces waste
Limitations of Cellular Systems
- Issues to form a cell due to lack of inadequate part families
- Poorly balanced cells due to variation in production volumes. Some cells may have high volumes and others have low volumes
- Identification of bottleneck machines during cell formation
- High capital investment to place duplicate machinery in the cells
- Machines may require their own induvial stock of materials