Lean Six Sigma (LSS) has become a widely accepted management strategy for achieving global process excellence in the service sector. The application and success of LSS in Information Technology (IT) organizations have been remarkable in the last decade. However, research on Lean Six Sigma Implementation in IT has been limited. A recent IT support services lean sigma six research study published in the 2019 TQM Journal by Gijo, EV, Antony, J, and Sunder M attempted to study the application of LSS DMAIC (Define-Measure-Analyze-Improve-Control) methodology in an IT services department of a large electrical equipment manufacturing company in India. The authors selected a problem with a high impact on customers to demonstrate the benefits of the LSS methodology to all parties involved in the case study.
During the research, processes were examined, data was recorded, and statistical tools and techniques were used to identify root causes. In addition, lessons learned from the initiative and challenges encountered during implementation were documented, which could aid future research in this area.
The research results demonstrate the effectiveness of LSS in improving processes and delivering customer value in IT services. However, the study also highlights the importance of selecting the right problem to address and the need for a continuous improvement mindset to sustain the benefits of the LSS methodology.
Here is an overview of how the IT support services in an electrical equipment manufacturing company implemented the DMAIC methodology of Six Sigma.
The Application of LSS Methodology In IT Support Services
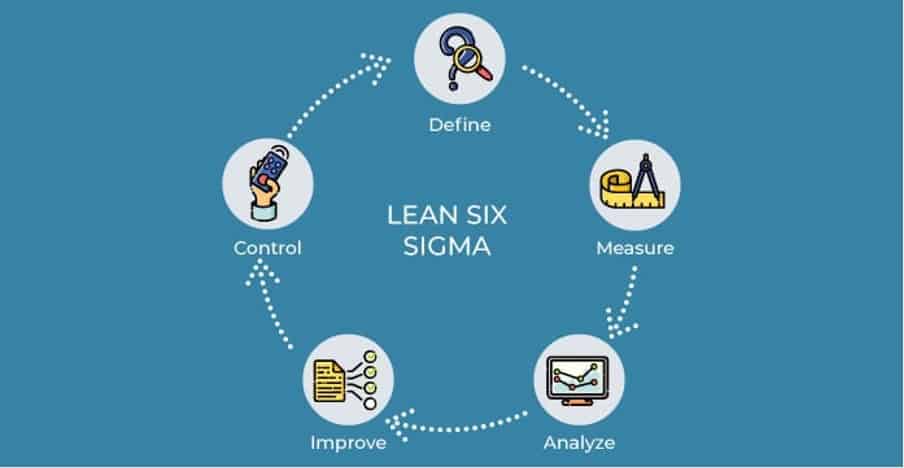
This case study is about a big company in India that makes electrical equipment and has about 12,000 employees. The company has a good management team that likes to use new technologies. They have some certificates for quality and have been using technology to improve things for over ten years. However, these concepts were mostly only taught and used in manufacturing and engineering processes.
The company uses an ERP computer system for everything, from buying materials to paying employees. But because the company is so big and does so many things, they use a lot of computers and the internet. They have a team to help with computer problems, but people often say they must wait too long to get help.
The organization uses computers and networks because it’s big and has many departments. Many people use the system simultaneously, so there are often problems with connections and other things. There’s a department that helps with computer, network, and software problems. People can report problems by email, phone, or writing in a book. But people often complain that it takes too long to solve the problems.
The company wants to use Lean Six Sigma DMAIC methodology to make things faster and better. The next section explains how they’re going to do it.
DMAIC Phases
Define Phase: Lean Six Sigma Implementation Case Study
The first step in the DMAIC methodology is called the “define phase,” which has two goals:
- To figure out what needs improvement based on what the customer wants, and
- To identify the process that needs fixing.
The Manager of the Systems Department formed a team of five people to achieve these goals. The other members were an Engineer in System Maintenance, an Engineer in Networking, an Engineer in Software Maintenance, and the Manager of Purchase. The team leader ensures timely project completion with expected results by involving all team members.
The project’s first step was to create a project charter containing all the necessary details, such as the team composition and the project schedule. Then, to better understand the process, the team created a SIPOC (Supplier-Input-Process-Output-Customer) mapping for the complaint resolution process, which is critical to the quality (CTQ) characteristics. The team chose to focus on this study.
The complaint resolution time was measured in hours. The team decided that the target for this characteristic should be five hours or less for all types of complaints. It is considered a complaint unresolved if it takes more than five hours to resolve.
Measure Phase: Lean Six Sigma Implementation Case Study
During this phase, the Six Sigma team created a data collection plan, specifying the data type, sampling method, and collection duration. First, the system collected data on Resolution Time (in days) for the past six months. They documented a total of 4265 complaints. Next, the data were checked for normality and found not to be normally distributed, with a p-value less than 0.05.
To fix this, they tried Box-Cox and Johnson transformations to normalize the data. Then, they calculated the summary statistics to understand the process baseline performance based on the chosen CTQ. Then, the lean six sigma team figured out how well the process was going by looking at some important numbers. They looked at these numbers based on the selected CTQ.
The average resolution time was 12.49 hours, with a standard deviation of 28.01 hours. Since the focus for the CTQ was 5 hours, the baseline performance shows room for improvement.
Analyze Phase: Lean Six Sigma Implementation Case Study
During this phase, the team investigated the reasons for complaint resolution delays by analyzing the process and data. The team used two methods to find out: process analysis and brainstorming.
They made a flowchart of the complaint resolution process to perform the process analysis. The researchers then checked all the steps in the process to see which ones were useful and which were not. Next, they found the steps that could have been more useful and made a list of them. After this, they talked to the project champion and customers to decide what to do with these useless steps.
They met with the project team and some user department staff to brainstorm. The team then investigated the potential causes of the delays. They did this by going to the place where the process happens (called “Gemba”) and observing what was happening. Next, they talked to the people who work there to see if they could find any root causes for the delays.
Ultimately, the team found two root causes for the delays: one from the flowchart and one from the brainstorming session. By solving these root causes, they hope to make the process simpler and faster.
Improve Phase: Lean Six Sigma Implementation Case Study
The goal of the improvement phase is to find ways to improve a process by fixing the root causes of problems. The team uses a cause-and-effect diagram and non-value-added analysis to choose the best solutions. Finally, the team put the plan into action and saw results. They gathered data from 460 samples after making improvements. The process now has an average of 8.47 and a standard deviation of 17.368.
Control Phase: Lean Six Sigma Implementation Case Study
Improving things is usually easy, but keeping them that way is harder. This is especially true for services, which often involve people. To make sure that improvements last, service providers can use methods like standardization, training, and motivation. For example, one IT service team documented procedures and told everyone how to report complaints.
They also made a chart to track how quickly they resolved issues, and the IT department checked it daily. After a while, they were able to make the process faster and more consistent. The time it took to solve problems went from 12.49 hours to 8.47 hours, and the variation in how long it took also decreased from 28.01 days to 17.368 days.
IT Support Services Lean Six Sigma Conclusion
This case study shows how the Lean Six Sigma methodology can improve processes and change staff and management mindset. The project focused on three important things: leadership & management commitment, customer focus, and bottom-line impact & cultural change. By implementing DMAIC, the project led to faster resolution times and less variability, which saved the company INR 2.5 million. The study also demonstrates the importance of collecting data and how it can help managers make better decisions.