Selecting Six Sigma projects is critical for project success. Project selection should be based on objective data and be quantifiable. It depends on the maturity of your organization.
A good Six Sigma project should align with the organization’s strategic goals and solve customers’ issues or concerns.
A successful Six Sigma project will direct the improvements in delivery schedule, quality, or financial benefit and meet the external and internal shareholder’s needs and expectations.

What is a Six Sigma Project?
Six Sigma is an important methodology that can be implemented in both manufacturing and service sectors. Usually, organizations deal with the known solution and unknown solutions of Six Sigma projects. Six Sigma black belts and green belts manage the projects of the unknown solution, while project or delivery managers lead the known solution projects.
Process identification is effortless, especially in manufacturing units, but it is not the case for the financial and service sectors. Hence organizations taking Black Belts help to identify the Six Sigma projects. Six Sigma is a disciplined and structured method that utilizes data and statistical analysis to measure and improve an organization’s operational performance and systems. Moreover, it is well suited for problems with unknown solutions.
Often projects tend to fail, and indeed even researchers and journals say that projects do not succeed and tend to fail, basically due to improper selection of projects. There is no guarantee that the Six Sigma project always succeeds, but with the right people and proper project selection, there is a high chance of success.
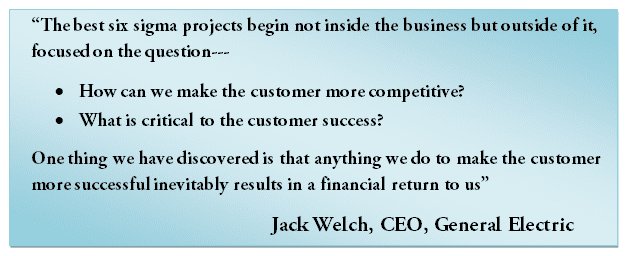
Elements of selecting a good Six Sigma project
Good Six Sigma projects are always linked to the organization’s goals and have the following characteristics:
- Connected to the organization’s business goals
- Clear gap between the current performance and the desired performance of the process; should have a high financial impact
- Projects should be focused on one critical process of the organization; in other words, the process is of major importance to the organization
- Clear measurable, and quantifiable performance of the process
- Project score should be optimal; in other words, do take too long or too short of a period (should be doable between 3 to 6 months)
- Needs management support for resources and budget
Roles and Responsibilities
Executive Leadership Roles:
- Describe the organization’s priorities that will help to grow and increase the market share
- Communicate the strategic organization initiatives
- Support the Six Sigma initiatives across the organization
- Assign responsibilities to Six Sigma champions and process owners
Champion Roles
- Discuss with relevant stakeholders, and select the projects that have a high business impact and also that have a high probability of success
- Develop a strong business case and map the project deliverables to the organizational goals
- Identify the critical features for project success
- Determine the quantifiable metrics to measure the project’s progress
- Assign resources and closely work with process owners
Where to find them
Six Sigma project ideas can basically come from two sources.
- External: Voice of the customer, benchmarking studies, market surveys, field complaints, competitive analysis, external rework, etc.
- Internal: Process assessments, employee surveys and suggestions, internal rework, manufacturing problems, etc.
Most of the institutions struggle to find high business impact projects. The following are the tools or methods that help to find and select the right Six Sigma projects:
Voice of Customer (VOC)
An understating of customer needs is critical for business success. Furthermore, businesses must be constantly in contact with customers. Collecting the voice of customers is a multi-level task. Below are the tools to get the Voice of the Client in an effective way:
- Reactive
- Complaint logs
- Hotlines
- Tech support calls
- Website activity
- Proactive
- Focus Groups
- Interviews
- Surveys
- Comment cards
- Marketing research
- Observation: “Go to the Gemba”
Kano Diagrams: The Kano model is a framework to prioritize features based on the degree to which they will satisfy or delight the users. In other words, a model that helps to prioritize features based on how much they will delight the users.
Critical-to-Quality Tree: A Critical to Quality Tree (CTQ Tree) reflects what the consumers of your process cite as absolutely essential to success. This helps to clarify what is a defect in the process. It also helps to distinguish what your client’s needs vs. what their requirements are.
The Pareto Chart is a graphical tool to map and grade business process problems from the most recurrent to the least frequent. In other words, this helps to identify the most frequently occurring problems or separate the vital few from the trivial many.
House of Quality: Quality Function Deployment (QFD) is a planning process for products and services that starts with the voice of the customer. Furthermore, it is a structured approach for defining customer requirements and translating design specifications or product control characteristics into the form of a planning matrix.
Hoshin Kanri
Hoshin Kanri is a management method that arose in Japan after World War II. Because it was extremely effective, it soon caught the attention of companies in other countries. These days, you can find people using the principles of Hoshin Kanri around the world.
Hoshin: Compass
Kanri: Management
Hoshin Kanri: You need direction in order to have effective management.
The basic steps in a Hoshin Kanri process are:
- Develop a strategic vision.
- Use the vision to decide company-wide goals spanning 1-5 years.
- From these goals, extract yearly objectives.
- Break down yearly objectives into monthly and weekly objectives.
- Develop and agree on the measures used to meet objectives.
- Measure progress toward these objectives monthly.
- Conduct an in-depth progress review annually.
FMEA: Failure Mode Effects Analysis (FMEA) is a tool that helps us anticipate what might go wrong with a product or process. We can also use it to identify the possible causes and probabilities of failures. Every process has potential weak spots. So, if we can recognize these in advance, we go a long way toward minimizing the damage caused. That’s why FMEA is such a handy tool.
Kaizen: Kaizen means an improvement on a continuous basis. If you are looking to minimize waste, improve customer satisfaction, augment business procedures and maximize operational efficiency, then it is time to implement Lean Kaizen in your organization. Kaizen is also highly effective in implementing and speeding up the change process in the organization.
Factors to consider process improvement methodologies
Six Sigma, Kaizen, and Lean are all process improvement methodologies that can help organizations achieve their goals. The choice of which methodology to use depends on several factors, including:
- Type of Process: Six Sigma is best suited for improving complex processes with many factors. While Kaizen is more effective for optimizing small, repetitive processes, and Lean is ideal for streamlining processes with waste elimination.
- Scope of the Project: Six Sigma is best suited for larger-scale projects requiring a significant amount of data analysis or SPC. Kaizen and Lean are more suitable for medium to smaller processes with more focused improvement initiatives.
- Resources: Six Sigma requires significant time and resources to implement, while Kaizen and Lean are generally more accessible and require fewer resources and less time.
- Organizational Culture: Kaizen and Lean are more suitable for organizations that value continuous improvement or waste elimination, while Six Sigma may be more suitable for organizations that prefer a more data-driven approach.
- Desired Outcome: If the goal is to achieve reduce variability or improve quality, Six Sigma may be the best choice. Otherwise, if the goal is to improve efficiency or eliminate waste, then consider lean. Kaizen may be the best fit if the goal is to achieve continuous improvement through employee engagement and involvement.
Ultimately, the choice of methodology will depend on the specific needs of the organization and the context of the project.
How to organize a large body of future projects
Kanban is a popular method for managing tasks in Lean and Agile environments. It can be used at all levels, from individuals to teams and entire companies.
It’s often used synonymously with Kanban boards. However, Kanban also involves a way of thinking about tasks and progress that enhances the use of the board.
How to Use a Kanban Board
Write every task on a card or post-it note at the start of a sprint or project. Add these tasks to the Backlog or To-Do column. Each team member picks a task, adds their name to it, and moves it to the next column.
While the rules vary depending on the methodology you’re employing, typically, one person should only have one task assigned to them at a time. That’s the task they are working on at the moment. If they aren’t working on it, it should be unassigned so anyone free can take it over.
Kanban Boards and Levels of Organization
We mentioned earlier that you can use Kanban boards at all levels, from individual to company. As you can probably imagine, the level of information displayed needs to change as the level of organization changes. Here are some examples of Kanban tasks at each level in a business:
- Individual: Modify User_Create code; Modify User_Edit code; Write unit test; Document code changes for code review; Run build test.
- Team: Add new user fields to code; Test user creation and modification; Modify knowledge base.
- Department: Extend user account.
You can see that as the number of people decreases, the granularity of tasks increases. You get more detail the further down you go. Try to imagine every person’s detailed tasks on a company-wide Kanban board; it would be a huge mess.
How to prioritize projects:
Project selection is a process to assess each Six Sigma project idea and select the ones with the highest priority.
During project selection, all the stakeholders review and identify the possible benefits of the project. All the projects are to be assessed and ranked according to a selection matrix.
Prioritization matrix – The prioritization matrix can help you to work out and negotiate priorities for a project. It can also be used to prioritize projects themselves, although opinions are mixed on whether this usage is a good idea.
Weighted and Scored Priority Matrix for Selecting Six Sigma Projects
In this style of project priority matrix, you use criteria and weightings to come up with scores for each competing feature, task, or project.

How to create a weighted and scored matrix
To create a scored and weighted priority matrix, follow the steps below. We’ve added cumulative examples for each step so you can see the matrix as it forms.
List your criteria for the tasks
These should be general factors that will apply to all of the tasks, features, or projects under consideration.
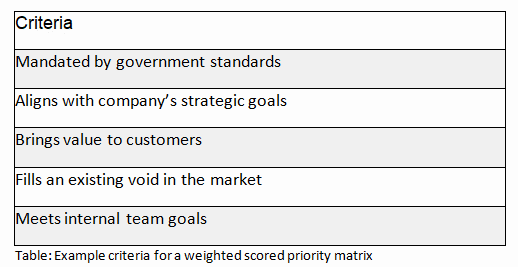
Decide a rating scale for each of the criteria
To make life easier, use the same number range for each. You don’t have to, but if you don’t, you’ll need to modify your weightings accordingly.
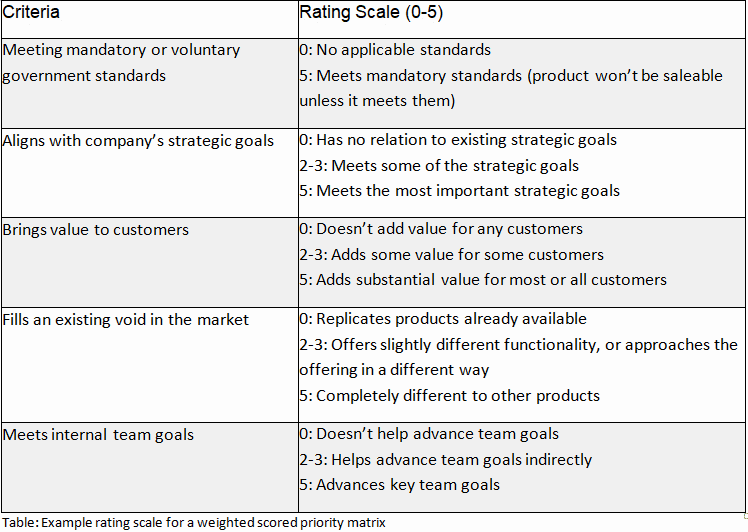
Set a weighting for each criteria
In any project, certain criteria will be more important than others. For example, in a project aimed at improving internal processes, you won’t be particularly interested in whether your improvements fill a void in the market. Or, when creating a new product, you typically won’t care much about individual team goals.
Your weighting needs to be a numerical value. The higher the weighting, the more important this criteria is to the project. Don’t include zero in weightings. This can mess up your calculations.
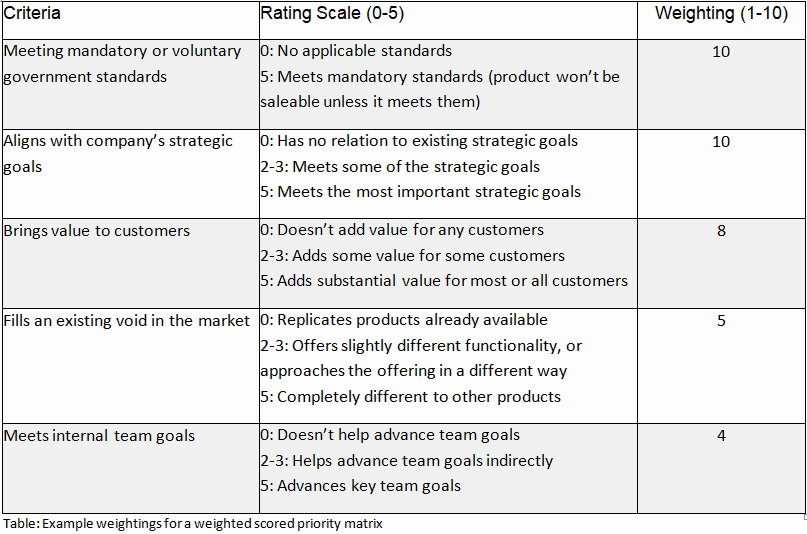
Score each of the criteria
It’s best to split up for this part because, typically, each stakeholder will have a different (and often valuable!) perspective. Group people into similar interest areas. For example, in a software project, you might create discrete groups of developers, project owners, salespeople, and user advocates.
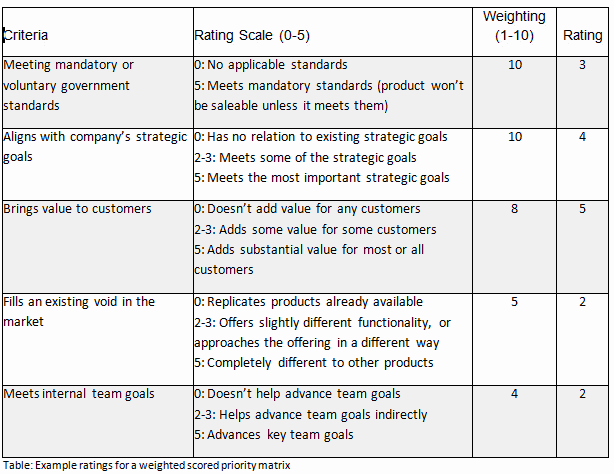
Calculate the score for each contender
Your ‘contenders’ are the features, tasks, or projects you’re trying to prioritize.
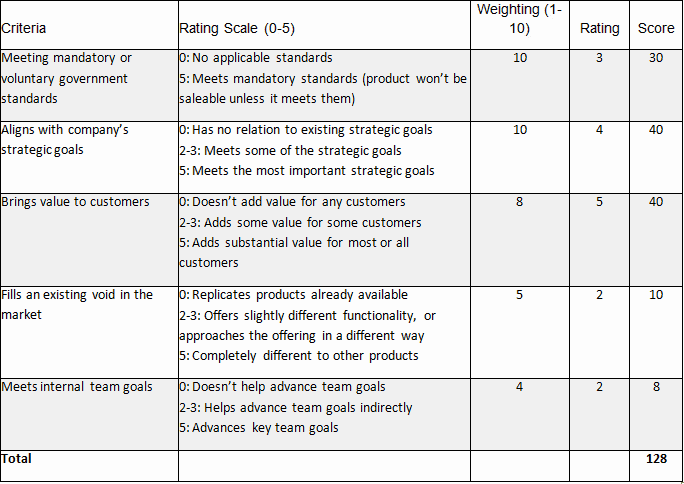
Discuss scores for each contender
This is a very subjective step. Pull all of your groups back together, and talk about the scores you gave each contender. You’ll find that there’s almost always disagreement between the various stakeholders. What’s more, that very disagreement will often dig up important information.
List agreed-upon scores in each criteria for all contenders.
Construct the priority matrix
- List your contenders down the side of your matrix, then add your criteria across the top.
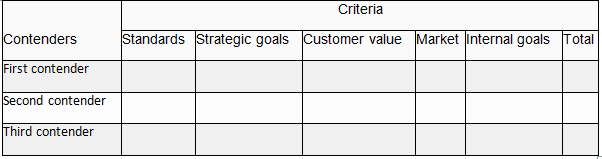
- Add the agreed-upon weighted scores.
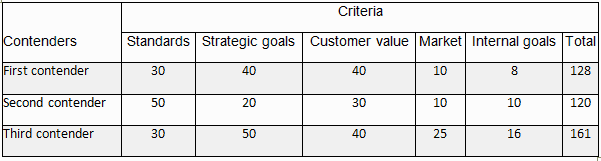
You can see in the example matrix above that the last option is a pretty clear winner. It hits a lot of goals, meets some industry standards, adds value to the customer, AND fills a void in the current market. Those are all clear advantages.
Videos
If it’s Just You Selecting Six Sigma Project
Yes, at the corporate level, there are guidelines on how to select projects. But what if you’re at a company without a strong Six Sigma office (or a continuous-improvement-minded Project Management Office)? What if you’re trying to be the first, what should you do? Similarly, what if you’re trying to get a Six Sigma certification that requires you to lead a project and you don’t have a formal structure?
Here are some thoughts on how to overcoming those hurdles:
https://sixsigmastudyguide.com/how-to-find-qualified-six-sigma-projects/
When you’re ready, there are a few ways I can help:
First, join 30,000+ other Six Sigma professionals by subscribing to my email newsletter. A short read every Monday to start your work week off correctly. Always free.
—
If you’re looking to pass your Six Sigma Green Belt or Black Belt exams, I’d recommend starting with my affordable study guide:
1)→ 🟢Pass Your Six Sigma Green Belt
2)→ ⚫Pass Your Six Sigma Black Belt
You’ve spent so much effort learning Lean Six Sigma. Why leave passing your certification exam up to chance? This comprehensive study guide offers 1,000+ exam-like questions for Green Belts (2,000+ for Black Belts) with full answer walkthroughs, access to instructors, detailed study material, and more.