A response plan goes with a control plan. A control plan sets out the quality requirements for a process and how to measure them. A response plan, on the other hand, sets out what to do if a process doesn’t meet one of those requirements.
Say, for example, you’ve just developed a new widget. The tooling on this widget is tricky, and if it’s only a fraction of an inch out in its sizing, it won’t fit into the gadget it’s designed for. So, your first step in the Control phase is putting together a widget’s control plan. This control plan specifies the required height, width, and depth of the widget, as well as its weight. It also tells the QA team which tools to use to measure each of these requirements. All good so far, right? Your next step is to develop a plan for what the team needs to do if the widgets aren’t measuring up. They might need to look at the tooling machine, check their measurement instruments, or halt production entirely while investigating the source of the variation.
The plan needs to:
- Address problems found by following the control plan.
- Give a detailed list of instructions to follow and checks to make in several potential scenarios.
Your plan might be very detailed or quite basic, depending on the complexity of your processes, equipment, and materials. You’ll often find that a control plan will include a response plan.
Where Does it Fit into DMAIC?
During the Control phase of a DMAIC project, you will want to write a response. This phase is dedicated to ensuring that improvements made during the project will continue once it’s finished. The plan generally helps the project by guiding staff on what to do if problems develop.
How to Develop a Response Plan
Likewise, your plan needs to be based on your control plan. If you don’t have one, then start there. You’ll often need a response plan for each QA requirement in the control plan.
- Designate a person responsible for addressing a problem with the requirement.
- Specify the initial steps to take.
- Based on those initial steps, provide guidance on what to do next in common scenarios.
- Give at least one general action plan if none of the common scenarios apply.
- Test it in real-time and amend the plan where needed.
Example
A company that makes fixings for the building industry has developed a new line of screws made from a tougher blend of steel. It has a control plan, but now it needs a response plan to go with it.
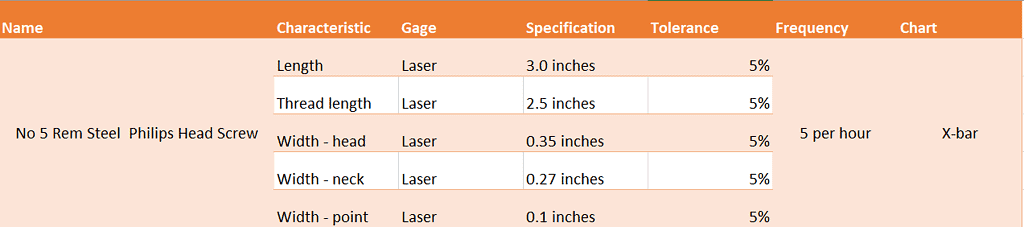
There are five points during the manufacturing process where a malfunction could cause a size variation:
- Firstly, before it begins – wrong wire used (neck width)
- Secondly, cutting machine (length)
- Thirdly, head-stamper (head width)
- Fourthly, shaping (point width)
- Finally, thread cutting (thread length).
So the response plan includes:
- Identify which specification is out of tolerance.
- Check the machine or material associated with that specification.
- If the machine is working correctly or the material is correct, check the quality of the material provided.
- If no material quality issues are detected, raise an issue with the factory manager.
Characteristic | Specification | Action |
---|---|---|
Length | < 2.85 inches > 3.15 inches | Check the most recent settings on the cutting machine. Run diagnostic on cutting machine. If the diagnostic is all clear, send a wire sample to QA for a pull test. If clear, escalate to the QA team lead. |
Thread length | < 2.375 inches > 2.625 inches | Run calibration test on thread cutter. If clear, run the diagnostic procedure. If clear, escalate to the QA team lead. |
Width – head | < 0.3325 inches > 0.3675 inches | Check head die in use on head-stamper. If correct, run diagnostic on head-stamper. Send a wire sample to QA for a pull test. If clear, escalate to QA team lead. |
Width – neck | < 0.2565 inches > 0.2835 inches | Check wire in use – should be 0.27″ gauge. If correct, send a wire sample to QA for a pull test. If clear, escalate to QA team lead. |
Width – point | < 0.095 inches > 0.105 inches | Run calibration test on shaper. If clear, run diagnostic procedure. If clear, escalate to QA team lead. |
Further Resources
Here are a few extra resources to check out on the topic of creating response plans:
- https://www.projectengineer.net/how-to-create-a-risk-response-plan/
- https://www.greycampus.com/opencampus/project-management-professional/plan-risk-responses
- https://www.wrike.com/project-management-guide/faq/what-is-contingency-plan-in-project-management/
Example Videos of Response Plans
The following videos are chiefly about cybersecurity Response Plans. Note that they follow the same general principles we discuss above applied to their domain.
Six Sigma Green Belt Response Plan Questions
Question: As a Belt completes a LSS project she creates for the Process Owner a Control Plan. The ________________ portion of the Control Plan details the actions to be taken when the KPI’s indicate they may be moving outside acceptable limits.
A) Visual Factory
B) Response Plan
C) Readjustment Plan
D) Variance Tracking
Answer:
B: Response plan. This is a definition question. See the Response plan here. Also see Visual Factory, Control Plan.
When you’re ready, there are a few ways I can help:
First, join 30,000+ other Six Sigma professionals by subscribing to my email newsletter. A short read every Monday to start your work week off correctly. Always free.
—
If you’re looking to pass your Six Sigma Green Belt or Black Belt exams, I’d recommend starting with my affordable study guide:
1)→ 🟢Pass Your Six Sigma Green Belt
2)→ ⚫Pass Your Six Sigma Black Belt
You’ve spent so much effort learning Lean Six Sigma. Why leave passing your certification exam up to chance? This comprehensive study guide offers 1,000+ exam-like questions for Green Belts (2,000+ for Black Belts) with full answer walkthroughs, access to instructors, detailed study material, and more.
Comments (4)
Create a Response plan are only for emergency? or we have to create to all process
Hi Alexa,
Yes, you want to create a response plan for every process that is in control. The idea is that you are providing a handbook of what to do should a currently in-control process suddenly become out of control.
This way we are able to lock in the gains and the improvements we’ve made to a process.
Best, Ted.
Hi Ted,
The link provided didn’t work. I wonder if you could update the source?
Best,
Qian
Hi Qian,
I’ve ear-marked this page for more updates but in the meantime I replaced the reference link with 3 others that should help!
Thank you for calling it to my attention!
Best, Ted.