Standard work–also often referred to as standardized work–is a Lean methodology concept. It involves finding the best current method of completing a process and making that method the standard.
An important point to remember is that standard work is not static. You won’t develop standard work processes and then leave them in place forevermore. Rather, standard work is part of a continual improvement cycle.
Elements of Standard Work
When developing standard work processes, we look at three specific variables:
- Takt time is the required rate of production.
- Work sequence is the best-practice process to be used.
- Inventory is the material required for the process.
Note that all of these elements are subject to change with the market and technology.
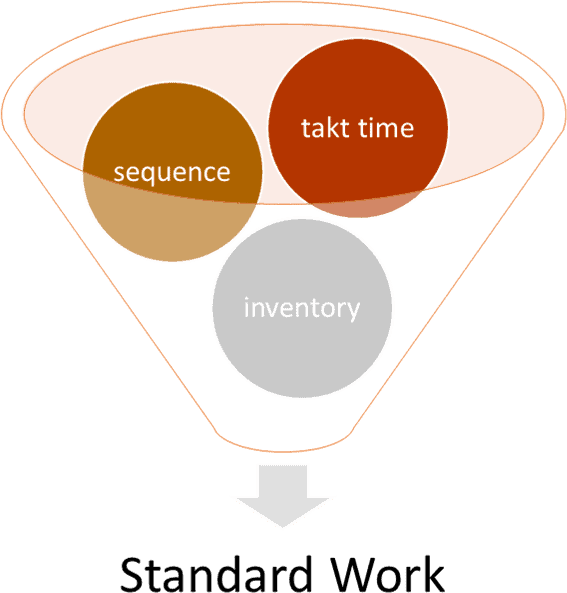
Takt time
Takt time is the rate (time per unit) at which you must produce items to keep up with customer demand. For example, if your standing orders add up to 500,000 widgets per month, and you have 140 hours of work time each month, then you can calculate your takt time thus:
Work seconds = 140 x 60 x 60 Work seconds = 504,000 Takt time = work seconds / demand Takt time = 504,000 / 500,000 Takt time = 1.008 seconds
For more information, see Takt time.
Sequence
The work sequence is the steps you require to perform a process best. You have two basic options when developing this sequence:
- Do lots of analysis work to figure out the most efficient method.
- Set a baseline with the current method and talk to staff to determine potential improvements.
While the first option might sound more reliable, it can become a rabbit warren of variables and what-ifs. It can also encourage an inflexible attitude to improvement (“We’ve already calculated the best possible method!”). Typically, you’ll actually find that the second approach is faster and gets better results. It also works better with Lean principles of including all staff in operational decision-making.
This is where the Lean/Agile concept of rapid iterations can be very useful to you. Making small adjustments to a process each week or fortnight and mapping the results can help you hone in on the most practically efficient process.
Inventory
Inventory is the material required to complete this process. As per Lean guidelines, it includes only the minimum material needed for the process. This might consist of parts, raw ingredients, or – in the case of a software-based project – even server time and resources.
When to Use It
This concept was designed for the manufacturing industry, and that’s still where it’s used most. However, it can be adapted to almost any environment; at least most jobs will have some best practices. Generally speaking, use standard work where:
- You have procedures that need to be repeated frequently if your company’s work changes from week to week, and procedures with it, trying to put standard work into place, will likely be an exercise in futility.
- Consistency is important. Does it matter if everyone does a job the same way? In many situations, the answer will be yes. If so, standard work will probably be ideal. However, it might not be your best option if it really doesn’t matter how the work is done.
- You want to improve continually. You can tweak and modify procedures to deliver improvements in quality and efficiency.
Why Use It?
Used correctly and appropriately, standard work helps you to eliminate waste, improve quality, and increase efficiency.
It eliminates waste by decreasing variation (because each product is manufactured similarly) and streamlining inventory. When you clearly define the materials needed for a specific process and know the required output in advance, you limit the waste opportunities.
Limiting the opportunities for mistakes in a procedure can improve quality. When everyone uses the same procedure, variation between end products decreases, improving customer confidence in the product.
You increase efficiency when procedures keep quality improvements but also decrease manufacturing or wait times.
Developing Instructional Material
Instructional material is a key part of standard work. Staff need quick, easy information to learn and remember key procedural points. Some tips from experts are:
- Keep it simple. Wherever possible, procedures should be linear progressions from one step to the next.
- Diagrams over words. Most people can grasp pictorial information more quickly and easily than written. See Visual Factory.
- Easy updates. Consider beforehand that you’ll need to be able to update instructions when you improve a procedure. Many companies use digital displays.
- Quick access. There’s no point situating the instructions on the other side of the factory from the machines to be used. Locate instructional material where it’s needed.
Example of Standard Work
A manager at an engine repair shop has noticed that there is a wide range of ‘time per unit’ between operators repairing engines in the service department. While this is partly due to the different models worked on, she thinks standard work might improve service efficiency and quality.
Takt time
She first looks at the time per unit the service team needs to keep up with repair demands. There’s a substantial backlog at the moment, so the team clearly isn’t meeting the required takt time.
She talks to the team to determine how much work time they have. Out of a standard 40-hour week, they spend 10 hours meeting and talking to customers. That leaves 30 hours per employee. There are five mechanics on the team. The center currently receives, on average, 100 requests a day for repairs to cars, motorbikes, and lawn mower engines. Some of these are turned away because the company can’t keep up with demand.
Work time = 30 x 5 = 150 Takt time = work time / demand Takt time = 150 / 100 Takt time = 1.5 hours
Note: We don’t use work seconds for procedures that will take substantially longer – work hours or minutes are more appropriate. Here, we’ve used hours because each task takes at least half an hour.
She looks at each employee’s time per job. Some achieve under the target time; others are substantially over, up to 3 hours per job.
Sequence
The manager spends some time on the floor to observe employees in action. She quickly realizes that the numbers haven’t told the whole story. One of the people whose job times are significantly over the takt time has more expertise and tends to take the harder, more fiddly jobs. However, she also notes that some of those jobs, while difficult, are routine in nature–just rare enough that no one else can do them as quickly. This is exactly the sort of situation that standard work can help with.
The manager talks to the staff about what she wants to achieve. She underlines that any procedures developed will be created with their input and will be open to continual improvement as they test the new processes. To minimize the time taken from employees’ work in putting the procedures together, she installs video cameras at the back of the faster and more expert employees’ benches. Each procedure video taken is matched with a model of the engine and one or more issues. Then, she hires a procedural writer to create simple graphic-heavy procedures that can be displayed on a touchscreen monitor.
As they develop the library of procedures, employees can soon enter the engine model, report problems, and see a best-practice procedure to follow in repairing the engine.
Inventory
Another issue is that staff often need to find specific parts for an engine. They could waste ten or fifteen minutes identifying and then finding a replacement for a part. It isn’t efficient for an employee to collect all parts that might be required at the start of a job; they won’t need most of them. Instead, she puts together lists of all parts used in each engine and matches these to inventory records. Staff can identify and find parts far more quickly.
Result
Now, when an employee starts a repair job, they:
- Enter the engine model and the issue reported by the customer.
- Read a best-practice procedure to follow.
- Can view the parts used in the engine and where to find each.
While some jobs are still taking more than the takt time, the majority–on common engines and with common issues–are taking less. In fact, the staff sometimes exceeds demand. The job queue is rapidly shrinking. The manager can now consider new marketing methods to bring in extra business.
Standard Work Videos
What You Need to Know to Pass Your Exam
Villanova Six Sigma Black Belt
Standard work
From Villanova Six Sigma Black Belt Body of Knowledge
Identify the key aspects of a standard work.
ASQ Six Sigma Black Belt
Waste elimination
From ASQ Six Sigma Black Belt Body of Knowledge
Select and apply tools and techniques for eliminating or preventing waste, including pull systems, kanban, 5S, standard work, poka-yoke, etc. (Analyze)
When you’re ready, there are a few ways I can help:
First, join 30,000+ other Six Sigma professionals by subscribing to my email newsletter. A short read every Monday to start your work week off correctly. Always free.
—
If you’re looking to pass your Six Sigma Green Belt or Black Belt exams, I’d recommend starting with my affordable study guide:
1)→ 🟢Pass Your Six Sigma Green Belt
2)→ ⚫Pass Your Six Sigma Black Belt
You’ve spent so much effort learning Lean Six Sigma. Why leave passing your certification exam up to chance? This comprehensive study guide offers 1,000+ exam-like questions for Green Belts (2,000+ for Black Belts) with full answer walkthroughs, access to instructors, detailed study material, and more.
Comments (2)
Based on the definition of standard work at the top of the page, finding a best current method and applying it as standard, it sounds very similar to benchmarking except its more narrow and only uses takt time, sequence, and inventory. Is there a better distinction between the two than saying standard work is a subset of benchmarking?
Hi Matthew,
Good question. Here’s how I see it:
Benchmarking is the research to find the best in the business. You might benchmark a process or the results an organization achieves based on that process. That benchmark may become or inform your own organization’s goals.
Standard work is the realization of an idealized process. You may use the Benchmarked process entirely, or develop a less-intense version of it that meets immediate needs or criteria.
I have soccer/football on the mind so I’ll use that as an example.
A youth coach might benchmark what Real Madrid does but then implement standard work as a version that fits his team. As his organizations matures (in skill, age, capabilities), he might improve the rigor of the standard work.