Preventative techniques in Six Sigma are used to proactively identify and address potential problems or defects before they occur. By implementing preventive measures, organizations can minimize the likelihood of errors, reduce waste, and improve overall process performance.
Implementing these preventive techniques in Six Sigma enables organizations to create a culture of proactive problem-solving and continuous improvement. By focusing on prevention rather than detection and correction, organizations can achieve higher levels of quality, efficiency, and customer satisfaction.
Why implement preventative techniques?
Implementing preventive techniques in Six Sigma allows organizations to take a proactive and strategic approach to quality management. This results in preventing defects and failures, leading to cost savings, increased efficiency, and improved customer satisfaction.
- Proactive Approach: Preventive techniques allow organizations to take a proactive approach to quality management instead of waiting for defects or problems to occur.
- Customer Satisfaction: Preventive techniques ensure the delivery of higher quality products or services, increasing customer satisfaction and loyalty.
- Cost Savings: Preventing defects and failures saves organizations significant costs associated with rework, scrap, customer complaints, and warranty claims.
- Improved Efficiency: Preventive techniques help streamline processes, eliminate waste, and optimize resource utilization.
- Risk Mitigation: Implementing preventive measures helps organizations identify and mitigate risks before they escalate into significant issues.
- Continuous Improvement Culture: Emphasizing preventive techniques fosters a culture of continuous improvement within the organization.
What are various preventative techniques?
There are several process analysis techniques that can be used to identify potential failures in a process. These techniques help organizations proactively identify risks and vulnerabilities to prevent failures before they occur.
By implementing preventive measures, organizations can minimize the likelihood of errors, reduce waste, and improve overall process performance. Here are some common preventative techniques used in Six Sigma:
Failure Mode and Effects Analysis (FMEA);
FMEA is a structured approach to identifying potential failure modes in a process, assessing their impact, and prioritizing preventive actions. In other words, it is a tool that helps us anticipate what might go wrong with a product or process.
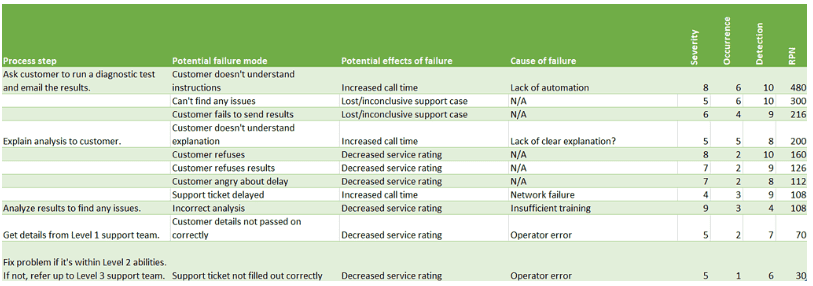
By conducting an FMEA (Failure Mode and Effects Analysis), organizations can proactively analyze and understand the causes and effects of potential failures. As a result, they can develop preventative measures and take action to mitigate or eliminate the identified risks.
Design for Six Sigma (DFSS):
DFSS is an approach used to design or redesign processes, products, or services to meet high-quality standards. It helps organizations to design efficiently that are less likely to have errors and defects.
DFSS focuses on building quality into the design from the beginning, considering customer requirements, process capabilities, and potential failure modes. Design validation serves as a preventive technique to ensure that a product or system meets its intended functions before releasing it.
Furthermore, organizations can proactively identify any design flaws, errors, or functional issues that may lead to failures or defects. This helps prevent problems or failures from occurring in the final product or system and ensures that it meets the desired quality standards.
Root Cause Analysis (RCA):
A Root Cause Analysis is a problem-solving method used to identify the root causes of faults or problems. By performing RCA, organizations can identify potential risks and take preventive measures to address the root causes. This helps in preventing similar issues from occurring in the future.
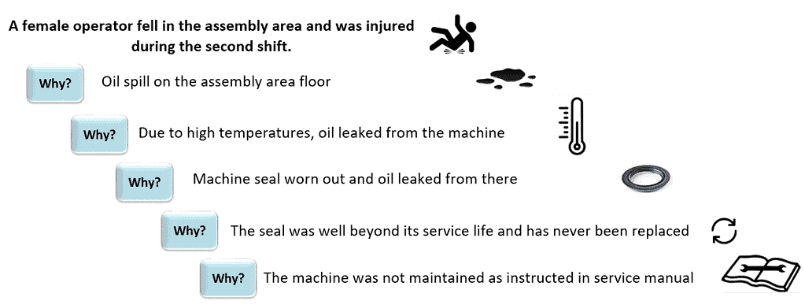
Mistake-Proofing (Poka-Yoke):
Poka-Yoke Error-proofing is the practice of making errors impossible through effective design. By implementing mistake-proofing techniques, organizations design processes or systems in a manner that prevents errors or mistakes from occurring. Furthermore, this can be achieved through the use of sensors, alarms, checklists, or other mechanisms that provide feedback and deter incorrect actions.
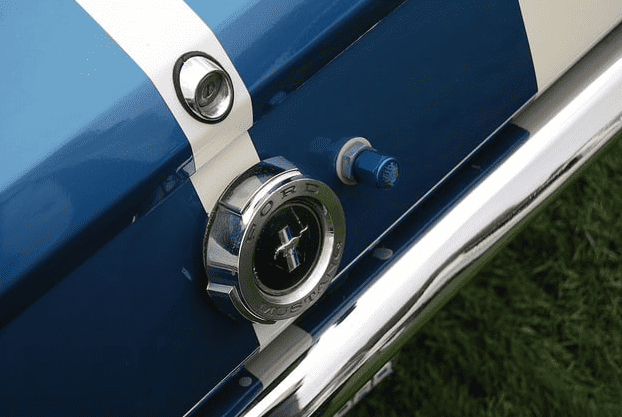
A great example for anyone driving in the US is gas pump nozzles’ different shapes and sizes. I can remember one bleary-eyed road trip in college where I was half awake when I tried to fill my 1986 Buick Regal with diesel instead of regular! Fortunately for me, the design of the gas nozzles incorporates poka-yoke. So, the triangular shape of the diesel gas nozzle makes it impossible to fit into the cylindrical gas receiver of my car. This demonstrates effective error-proofing.
Standard Operating Procedures (SOPs):
SOPs define the steps, controls, and best practices to be followed in a process. Furthermore, by providing employees with clear instructions and guidelines to follow, organizations effectively minimize the chances of errors and variations in the process.
SOPs typically include information such as the purpose of the procedure, the responsibilities of individuals involved, the sequence of steps to be followed, safety precautions, and any necessary documentation or forms.
Statistical Process Control (SPC):
Statistical Process Control (SPC) ia method that employs statistical techniques to measure, monitor, and control a process. Additionally, it serves as a scientific visual method to monitor, control, and improve the process by eliminating special cause variations.
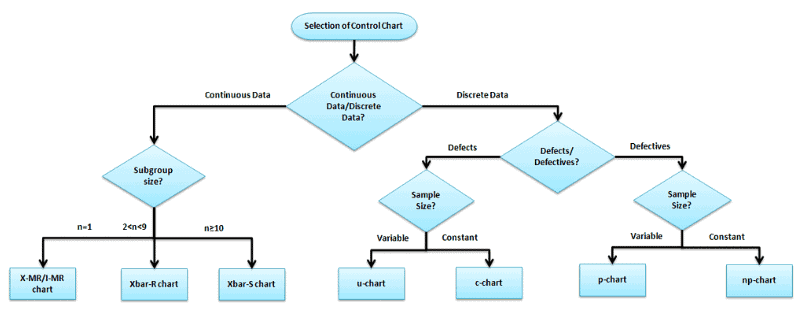
By using control charts and statistical analysis, organizations can detect process variations and take preventive actions before they lead to defects. Additionally, SPC helps identify early signs of process instability or shifts, allowing for timely intervention.
Training and Education:
Providing comprehensive training and education to employees is crucial for preventing errors and defects. As a result, employees gain the ability to perform their tasks accurately and efficiently, effectively preventing errors and defects.
Verify the effectiveness of Preventative action.
- Data analysis: Analyze data before and after implementing the preventive action to assess the impact on key performance indicators (KPIs) and metrics. Look for improvements or reductions in incidents, defects, or downtime.
- Periodic reviews and audits: Perform periodic reviews and conduct regular audits to assess compliance with preventive measures and identify any deviations or areas for improvement.
- Root cause analysis: If incidents or issues occur despite the actions, conduct root cause analysis to identify causes or gaps in the preventive measures. Make necessary adjustments to improve effectiveness.
- Continuous improvement cycle: Continually evaluate the preventive action using a continuous improvement approach, such as the PDCA (Plan-Do-Check-Act) cycle.
- Internal and external benchmarks: Compare the organization’s performance with industry best practices to assess the effectiveness of the preventive action(s).
Benefits of Preventative Techniques
- Reduces the likelihood of defects and failures, ensuring higher quality standards.
- Minimizes rework and scrap, optimizing resource utilization and reducing waste.
- Lowers the costs associated with quality issues, leading to improved financial performance.
- Improves process efficiency and productivity, streamlining operations and reducing cycle times.
- Enhances customer experience and fosters loyalty through consistently delivering high-quality products or services.
- Mitigates risks and prevents adverse events, safeguarding operations and minimizing disruptions.
- Protects the organization’s reputation and brand image, reinforcing trust and credibility in the market.
Important Videos
When you’re ready, there are a few ways I can help:
First, join 30,000+ other Six Sigma professionals by subscribing to my email newsletter. A short read every Monday to start your work week off correctly. Always free.
—
If you’re looking to pass your Six Sigma Green Belt or Black Belt exams, I’d recommend starting with my affordable study guide:
1)→ 🟢Pass Your Six Sigma Green Belt
2)→ ⚫Pass Your Six Sigma Black Belt
You’ve spent so much effort learning Lean Six Sigma. Why leave passing your certification exam up to chance? This comprehensive study guide offers 1,000+ exam-like questions for Green Belts (2,000+ for Black Belts) with full answer walkthroughs, access to instructors, detailed study material, and more.