I. Introduction: The Power of Cost-Benefit Analysis in Six Sigma
When organizations initiate Six Sigma projects, they often face uncertainty in selecting the most effective projects to enhance processes and achieve financial benefits. To make smarter, data-driven decisions, organizations conduct a cost-benefit analysis before implementing improvement actions. This approach helps prioritize projects that offer the greatest potential for process optimization and financial gain.
Cost-benefit analysis involves identifying the costs and benefits associated with a system, assigning monetary values to them, estimating future cash flows, and evaluating the project’s financial viability. It can also be described as a process that assesses all incurred costs and potential profits to determine the feasibility and profitability of a business opportunity or proposal.
Example: Battery Manufacturing Company – Evaluating the adoption of a new battery production technology by comparing the costs (e.g., materials, new machinery, training) with the benefits (e.g., reduced battery charging time, less recycle, higher production efficiency).
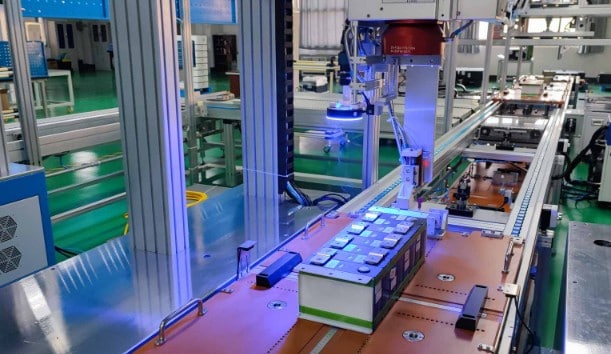
Car Manufacturer – Reviewing the financial feasibility of launching an electric vehicle line by comparing the costs (e.g., R&D cost, battery, production setup) with the benefits (e.g., new market demand, government incentives, reduced fuel dependency).
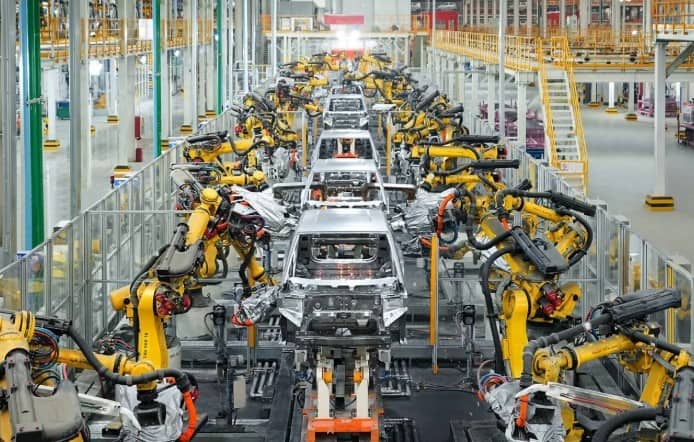
Cost-benefit analysis is utilized at all levels by Six Sigma practitioners. Yellow Belt practitioners typically focus on small process improvements and use cost-benefit analysis to justify these changes by assessing the costs of improvement against the expected benefits. Green Belts applies this concept to medium-sized projects, helping to evaluate multiple improvement opportunities and select the project with the highest return on investment (ROI).
Black Belts uses cost-benefit analysis for large-scale projects, conducting detailed financial evaluations to support senior management in decision-making. This process helps leadership select projects based on financial projections and risk assessments.
II. What Is Cost-Benefit Analysis?
Cost-benefit analysis is a systematic approach used to assess the financial value of a project or decision by comparing its associated costs with the expected benefits. This method helps identify whether the benefits surpass the costs and to what extent, enabling informed decision-making.
Cost-benefit analysis helps organizations to get a clear understanding of a project’s financial opportunities and risks. Since capital resources are often limited, multiple projects compete for funding. The higher the project cost, the more in-depth the analysis must be to ensure informed decision-making and optimal resource allocation.
Steps Involved in Cost-Benefit Analysis
- Identify the benefits of the project.
- Determine the benefits in terms of dollars, time, and duration.
- Evaluate project costs, including materials, labor, and resources.
- Estimate the costs in terms of dollars and expenditure periods.
- Calculate the total project losses and gains.
- Determine whether to implement the project based on the benefits.
- If top management still desires to proceed despite low benefits, identify and implement the changes needed to make the project cost-effective
Key Components:
Costs: Direct and indirect, such as labor, materials, or downtime.
- Developmental costs: These are the tangible expenses that are incurred during the creation of system such as salaries, hardware, software expenses, consultant fees training, and office space and equipment.
- Operational costs: Tangible costs that are required to operate the system such as salaries, software license fees, equipment upgrades, and communication charges. Operational costs are usually ongoing costs
Benefits: Tangible (revenue increase) and intangible (improved customer satisfaction).
- Tangible benefits: Tangible benefits include the revenue that the system enables the organization to collect such as increased sales. In addition, the system may enable the organization that avoid such costs leading to another type of tangible benefits
- Intangible benefits: Projects also can affect the organization’s bottom line by reaping intangible benefits. Intangible benefits are more difficult to include in the cost-benefit analysis
III. The Role of Cost-Benefit Analysis in the Define Phase
- Project Selection: Cost-benefit analysis helps identify high-impact projects by analyzing all the costs associated with implementation and the projected benefits. Moreover, important metrics such as ROI, NPV, and Payback Period help highlight projects that provide the highest relative value. Cost-benefit analysis also helps assess risks and uncertainties to understand the financial impact of different scenarios. When organizations align financial benefits with their strategic objectives, it supports the achievement of long-term goals.
- Tools for Analysis:
- SIPOC diagrams to map processes.
- Stakeholder analysis to align expectations.
- Practical Example: A Yellow Belt project reducing operational waste.
IV. Applying Cost-Benefit Analysis in the Improve Phase
Solution Validation: A formal cost-benefit analysis usually includes costs and benefits over a selected number of years to show cash flow over time. It calculates key financial metrics such as ROI, Payback Period, and NPV. By analyzing the cost-benefit ratio, it helps identify high-impact projects that align with business objectives and provide maximum value to customers. In the Improve phase, it assesses risks and supports informed decision-making and resource optimization.
Metrics to Include:
ROI (Return on Investment).
The return on investment (ROI) is a calculation that measures the average rate of return earned on the money invested in the project. ROI is a simple calculation- The project net benefits / total cost.
ROI = Net income/ investment = (Total benefits – Total cost)/ Total cost *100
A high ROI suggests that the project benefits far outweigh the project cost.
Net Present Value (NPV).
Net present value (NPV) is simply the difference between the total present value of the benefits and the total present value of the costs.
NPV=ΣPV of Total benefits- Σ PV of total costs.
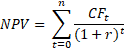
Where n is the number of periods, t is the time period, r is the per period cost of capital for the organization and CFt is the cash flow in time period t.
As long as the NPV is greater than zero, the project is considered economically acceptable.
Internal rate of return (IRR)
The internal rate of return (IRR) is the interest or discount rate, I or r, that results in a zero net present value, NPV=0 for the project. The internal rate of return (IRR) is the percentage of returns that a project will generate within a period to cover its initial investment. It is attained when the Net Present Value (NPV) of the project amounts to zero.
An IRR higher than the discount rate signifies a profitable investment opportunity.
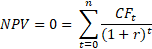
Payback period.
The payback method (also called the break-even point) is defined length of time necessary for the cash benefits to net costs. In other words, the number of years it takes an organization to recover its original investment in the project from net cash flows.
Payback period= Initial (& incremental) investment/ Annual (or monthly) cash inflow
Case Study: A Green Belt initiative improving assembly line efficiency.
Step-by-Step Example:
A manufacturing plant is planning to start a new project with an initial investment of $80 million. Management expects returns of $15 million in the first year, $20 million in the second year, $25 million third year, $35 million in the fourth year, and $20 million in the fifth year. Calculate the payback period.
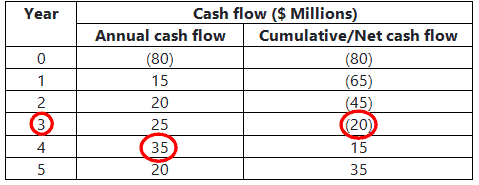
Payback period = Last time period with negative net cash flow + (Net cash flow at the time of last negative value/ cash flow of the consecutive year) = 3+(20/35) = 3+0.57=3.57 years.
V. Cost-Benefit Analysis as a Performance Metric
- Measuring Success: Cost-benefit analysis quantifies the impact of Six Sigma projects by converting process improvements into measurable financial outcomes. It calculates all the costs incurred to implement the process improvements and the corresponding estimated benefits. The following are the key performance indicators (KPIs) to track.
- KPIs to Track:
- Cost reduction.
- Increased profitability.
- Process efficiency.
- Reduced manpower efforts
- Avoidance of failures, rework, and warranty costs
- Visualization Tips:
- Use charts or dashboards to display CBA results.
- Share results with stakeholders to build trust and buy-in.
VI. Sustaining Improvements: Cost-Benefit Analysis in Control Plans
- Why It Matters: Many organizations implement process improvements but struggle to sustain them long-term, resulting in wasted resources and efforts. To ensure operational sustainability, it is essential to continuously monitor performance metrics, conduct regular audits, and gather stakeholder feedback. Integrating cost-benefit analysis with the control plan also enables systematic monitoring, maximizing the value of improvements over time.
- Control Plan Integration:
- Regularly monitor cost-benefit metrics.
- Adjust processes when benefits decline or costs rise.
- Example: A Black Belt project for supply chain optimization, monitored quarterly for cost savings and efficiency.
VII. Avoiding Common Pitfalls in Cost-Benefit Analysis
- Use reliable data and realistic cost assumptions to avoid underestimating the expenses associated with process improvements.
- Always consider intangible benefits, such as brand value, employee engagement, and customer satisfaction, to capture the full impact.
- Work with evidence-based data to eliminate biases.
- Conduct risk analysis to identify potential challenges and assess the extent of benefits.
- Improvement projects should align with organizational strategies and objectives.
- Evaluate both long-term and short-term cost-benefit analyses to ensure sustainable financial growth.
- Use appropriate metrics and methods for cost-benefit analysis to enhance accuracy and reliability.
VIII. Tools and Techniques for Effective Cost-Benefit Analysis
- Simple Tools:
- Excel templates for CBA calculations.
- SIPOC and DMAIC integration.
- Advanced Software:
- Tools like Minitab or specialized Six Sigma calculators.
IX. Real-Life Applications of Cost-Benefit Analysis in Six Sigma
Yellow Belt Example:
Reducing meeting times in an office environment. The team should evaluate the costs involved, such as training, tools, and costs related to change management. Similarly, they should consider the benefits, such as productivity improvements, reduced resource usage (e.g., A/C, room occupation), and increased employee satisfaction. For example, if the implementation cost is $6,000 for tools, training, etc., and the total hours saved per month is 50, with an average hourly rate of $60, the payback period would be 2 months ($6,000 / (50 * $60)).
Green Belt Example:
Streamlining production workflows. The Cost-benefit analysis evaluates the costs and benefits of streamlining the production flow. Consider costs such as new equipment, training expenses, layout change costs, and waste during the new setup. Benefits include increased production speed, reduced material movement, lower labor costs, and improved product quality.
For example, if the implementation cost is $40,000 and streamlining production workflows saves $10,000 per month, the annual benefit would be $120,000.
ROI= (Annual Benefit−Cost)/Cost×100 = (120,000−40,000)/40,000×100=200%
The 200% ROI shows that the project generates two times the initial investment, justifying the improvement.
Black Belt Example
Enterprise-wide implementation of automated systems. Cost-benefit analysis evaluates the costs related to purchasing automated tools, server expenses, installation costs (including travel to various locations for installation and training), temporary production stoppages, software maintenance, and production environment changes. Benefits include improved efficiency across locations, real-time reporting systems, reduced labor costs, increased production output, and enhanced consistency.
For example, suppose the implementation cost is $480,000 and the enterprise-wide implementation of automated systems saves $150,000 per year for five years. In that case, the Net Present Value (NPV) can be calculated using a discount rate of 10% to account for the time value of money.
Here r =0.1
1+r = 1.1
NPV=ΣPV of Total benefits- Σ PV of total costs.



With an NPV of $88,618, the Enterprise-wide implementation of automated systems shows a positive return, indicating that the automation investment is financially beneficial and justifies the initial cost.
X. Conclusion: Making Cost-Benefit Analysis Work for You
Cost-benefit analysis is an economic evaluation technique that measures all the positive and negative consequences of an intervention in monetary terms. Simply put, cost-benefit analysis is a process used to measure the benefits of a decision minus the costs associated with taking that action.
Start using CBA in your organization for smaller projects and measure metrics such as NPV, payback period, and more to build confidence. Please share your experiences and thoughts in the comments section to help others understand various aspects of cost-benefit analysis.
XI. FAQ Section
How often should CBA be updated in a control plan?
There is no specific periodicity for updating the control plan; however, it should be updated at least once a year to reflect changes in costs, benefits, and market conditions. Regular updates help maintain the relevance and accuracy of the CBA, ensuring informed decision-making and resource allocation.
What is the difference between cost-benefit analysis and ROI?
Cost-benefit analysis assesses all costs and benefits, including tangible and intangible factors, to determine a project’s overall financial worthiness. In contrast, ROI measures the profitability of an investment by calculating the percentage return relative to its cost.
Can cost-benefit analysis include intangible benefits?
Yes, cost-benefit analysis can include intangible benefits, even though they are not easily quantifiable in monetary terms. Intangible benefits may include brand value, employee engagement, and customer satisfaction.
What’s the best software for CBA in Six Sigma?
Microsoft Excel and Minitab