A Cause-and-Effect Diagram (aka Ishikawa, Fishbone) is a picture diagram showing possible causes (process inputs) for a given effect (process outputs). In other words, it is a visual representation used to determine the cause(s) of a specific problem.
The Cause and Effect diagram is called the “Ishikawa diagram” or fishbone diagram. This is because the diagram looks much like the skeleton of a fish. Fishbones are drawn right to the left, with each large bone of the fish drawn out to include smaller bones that add more detail.
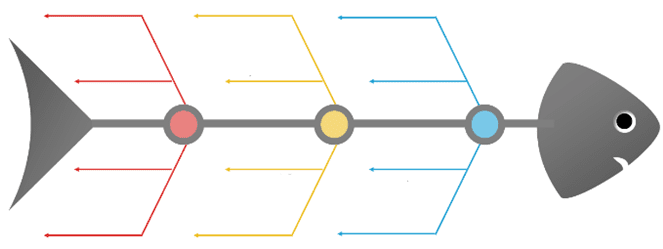
The Cause-and-Effect Diagram (aka Ishikawa, Fishbone) introduced by Kaoru Ishikawa (1968) shows the causes of a specific event. Additionally, Ishikawa introduced company-wide quality control (CWQC) and the concept of quality circles in Japan. Typical uses of the Ishikawa diagram are product design and quality defect prevention to identify potential factors causing an overall effect. It is one of the seven essential tools of quality control.
In particular, this method is standard in brainstorming and the “open” phase of root cause analysis.
When to use the Cause and Effect Diagram
- When the problem has multiple possible causes
- To identify the possible root causes for an effect
- Identify and sort interactions among the factors on an effect
- Finally, to initiate appropriate corrective action for existing problems
Why use a Cause-and-effect diagram
- It is an essential step to study a problem and determine the root cause.
- It allows you to study all the probable causes of why a process begins to have a problem.
- It helps you identify areas of data collection for further study.
How to develop a Cause-and-effect diagram
The Cause and Effect diagram is a structured graphical diagram listing all possible causes and their relationship with the main effect or problem. The diagram’s primary input is the brainstorming that pushes to identify all the possible causes rather than just more noticeable ones.
Following are the steps to draw a fishbone diagram:
Step 1: Identify the problem:
- Firstly, identify and clearly write down the effect or a problem that needs to be analyzed.
- Then, create an operational definition of a problem to ensure all the stakeholders will understand it.
- An effect may be positive, like an objective (to improve the process further), or negative, like a problem (to identify customer dissatisfaction).
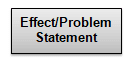
Step2: Determine Effect or Problem:
- Next, draw a horizontal line. This is a spine.
- At the end of the spine, towards the right, draw a box and determine the description of an effect.

Step 3: Identify major causes contributing to the effect or a problem
- Establish leading causes and write them down above the horizontal line and a few below the horizontal line. Make sure they are placed on the tail of the same arrows.
- Each cause or reason for imperfection is a source of variation. Causes are usually grouped into major categories to identify these sources of variation. These include: (Also see the 5Ms and 1P).
- Man/People: Anyone involved with the process.
- Methods: How the process is performed and the specific requirements, such as policies, procedures, rules, regulations, and laws.
- Machines: Any equipment, computers, tools, etc., required to accomplish the job.
- Materials: Raw materials, parts, pens, paper, etc., used to produce the final product.
- Measurements: Data generated from the process used to evaluate its quality.
- Environment: The conditions, such as location, time, temperature, and culture, in which the process operates.
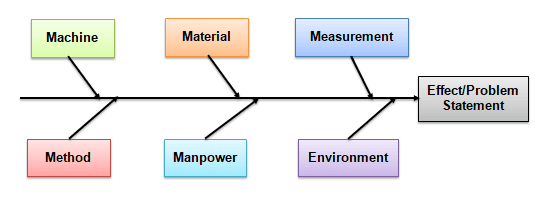
Step4: Identify sub causes
- Identify as many sub-causes that are relevant to the leading causes and are placed under each main cause category.
- For instance, if the sub-cause applies in multiple places, list it under each main category.
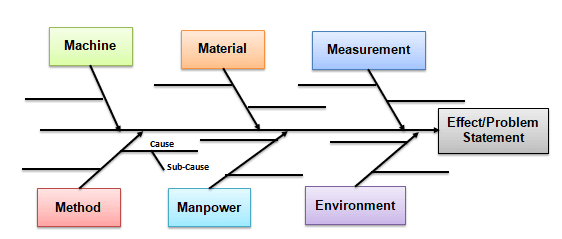
Step 5: Analyze the diagram
- Currently, the fishbone diagram shows all the possible causes of an effect.
- Identify causes that are not impacting the effect and also identify causes that need further investigation.
- Further, perform a 5Why analysis of the identified causes (also called noises) to arrive actual root cause.
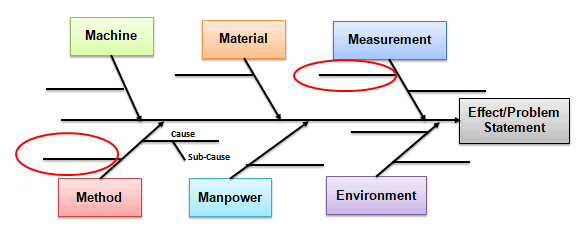
Cause and Effect Diagram Example
By and large, Fishbone diagrams are used to identify the root causes of a problem in the “Analyze” phase of Six Sigma’s DMAIC (Define, Measure, Analyze, Improve, and Control).
Example: XYZ is a valve manufacturing unit receiving persistent customer complaints about the valve diameter. The plant’s General Manager asked the QA and Production team to analyze the root cause. So, the team performed Brainstorming and drew the Cause and Effect diagram to identify all the possible causes.
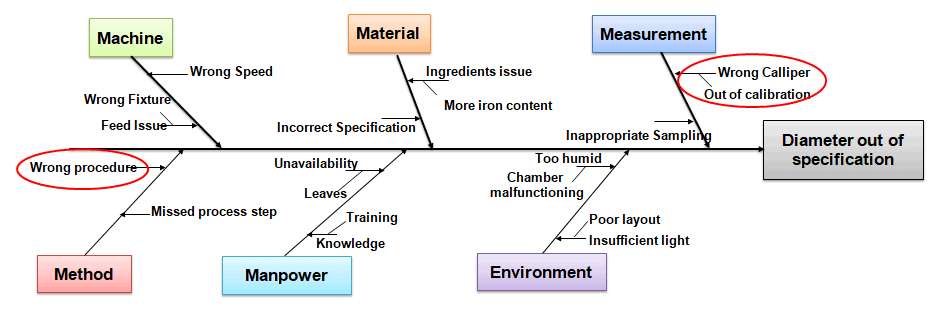
The team identified that the wrong caliper and wrong procedures were the probable causes. Further, the team has to perform a 5 Why analysis to determine the root cause.
Benefits of Cause and Effect Diagram
- It helps to identify all the probable causes of an effect to identify root causes further.
- It encourages a systematic approach to problem-solving by categorizing potential causes into different categories.
- Furthermore, it visually depicts all potential causes associated with a problem, aiding in identifying root causes.
- The cause and Effect diagram is easy to implement in any case.
- Cause and effect diagrams can save time and resources that would otherwise be wasted on addressing symptoms or applying ineffective solutions.
- Fosters teamwork and inspires the team to brainstorm until the root cause is eliminated.
- A shared understanding of the factors causing the problem.
Fishbone Diagram Best Practices
- Focus on the cause, not just solutions.
- Go beyond the superficial levels to find root causes. So, don’t merely outline options.
- Finally, ask “why” until it is absurd to continue.
Cause and Effect Diagram Template Download
Fishbone Diagram videos
Further, Minitab put out a good video on how to use their software to brainstorm and create a fishbone diagram. If you’ve never done this before, this is a great reference.
ASQ Six Sigma Black Belt Exam Fishbone Diagram Questions
(Taken from ASQ sample Black Belt exam.)
Question: A company’s accounts payable department is trying to reduce the time between receipt and payment of invoices. If the team has just completed a process flow chart and identified the critical steps, which of the following tools should be used next?
A) Fishbone diagram
B) Scatter diagram
C) Box and whisker plot
D) Histogram
Answer:
When you’re ready, there are a few ways I can help:
First, join 30,000+ other Six Sigma professionals by subscribing to my email newsletter. A short read every Monday to start your work week off correctly. Always free.
—
If you’re looking to pass your Six Sigma Green Belt or Black Belt exams, I’d recommend starting with my affordable study guide:
1)→ 🟢Pass Your Six Sigma Green Belt
2)→ ⚫Pass Your Six Sigma Black Belt
You’ve spent so much effort learning Lean Six Sigma. Why leave passing your certification exam up to chance? This comprehensive study guide offers 1,000+ exam-like questions for Green Belts (2,000+ for Black Belts) with full answer walkthroughs, access to instructors, detailed study material, and more.
Comments (14)
Should we conduct WW analysis first or conduct fishbone diagram first?
I’m not sure what you mean by WW analysis. Can you elaborate?
Thank you Ted, been enjoying the learning from your web… just tickled to reply on this, I thought WW refers to World War asked by previous commenter Praful.
Hah! Yeah, I wasn’t sure. I wonder if he meant the 5 Whys.
can i please get an example or sample of fishbone analysis on the account payable process improvement?
I can help. Please share with me how you started.
thank you for the review. I remember this from Beth Cudney(I believe her name is) with IVMF.
Great to hear that name again! I met Beth and attended her lecture on lessons learned teaching Six Sigma and DMAIC back at the 2018 ASQ World Conference.
Her presentation inspired me to also become a presenter at ASQ’s various world conferences.
From the little bit of time I spent there I could tell that she’s a wonderful instructor with a passion for sharing the material.
10.15.2020 Good morning,,, 1.4.4 The 7 Elements of Waste has refused to print as has the Kaizen sub-group in 1.4.1. Would you fix it??
I’m learning just what I needed with the math, formulas and explanation of how to work the problems. The other group offered none of this. You work from right to left in complex math formulas or do you start with all contained within parantheses and/or brackets? Bobbie
Hi Bobbie,
I don’t see those items on this page, which page are you referring to.
As for what order to do algebra in, your referring to Order of Operations. There’s a good primer here: https://www.mathsisfun.com/operation-order-pemdas.html
In short PEMDAS:
P: Parentheses first
E: Exponents (ie Powers and Square Roots, etc.)
MD: Multiplication and Division (left-to-right)
AS: Addition and Subtraction (left-to-right)
Does that help?
10.16.20 yes, thanks…PEMDAS does te trick!
In the DPMO example problem, 1.2.5 Basic Six Sigma Metrics, where does the 0.8406 value come from?
Bobbie
Hi Bobbie,
It’s easier for me to answer questions if you put them in the comments on the page you’re asking them about.
In this case I think you’re asking about the Process Sigma level calculation discussed here.
It’s a good question.
The numbers 0.8406, 29.37 and 2.221 come from, they are constants that help us calculate the DMPO or level simply.
Process Sigma = 0.8406 + SQRT(29.37 – 2.221 * (ln(DPMO))).
Reference: >a href=”https://amzn.to/2T6sLgg”>Breyfogle, F., 1999. Implementing Six Sigma: Smarter Solutions Using Statistical Methods. 2nd ed. John Wiley & Sons.
I’ve updated that page to include these notes.
Best, Ted.
It’s very good to know Lean AI concept and it’s interesting to come up with such advanced tools which make our work life easier.
Happy to help, Vignesh!