The 5 Whys is a root cause analysis technique used in the Analyze phase of the Six Sigma DMAIC (Define, Measure, Analyze, Improve, Control). To solve a problem, we need to identify the root cause and then eliminate it. Therefore, the 5 Whys goal is to drill down to the bottom of the problem and then prevent its recurrence.
To understand why we use the 5 Whys, picture a child asking her dad “Why” repeatedly. It might drive him mad, but it teaches the child (and us) an important lesson in the Six Sigma Quality chapter.
5 Whys does not contain hypothesis testing, regression analysis, data segmentation, or other types of advanced statistical tools. Rather, it is a simple technique. Here, we ask “Why” until we can’t ask “Why” again. The number 5 is a good rule of thumb, but it is of course, arbitrary. You are free to ask “Why” as many times as needed. By doing so, we can quickly reach the underlying causes of a problem.
Origin
Sakichi Toyoda, one of the fathers of the Japanese industrial revolution and the founder of Toyota Industries Corporation, developed this technique in the 1930s. By the 1970s, this method became popular, and Toyota and many other firms still use it to solve problems.
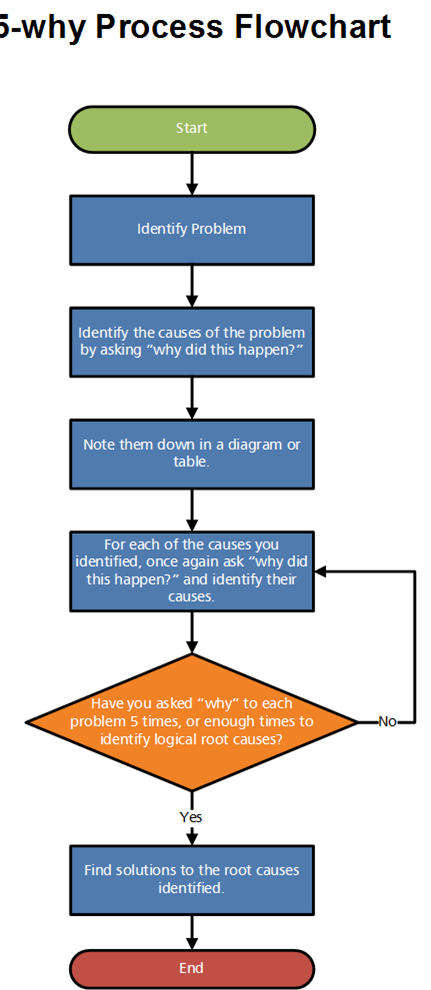
How to Complete the 5 Whys
Step 1. Forming a team:
Here the team members who gathered should be the ones familiar with the details, affected by the problem, or noticed the problem.
After this, select a master for the meeting who will lead the discussion, ask the 5 whys, and assign responsibility for the solutions the group comes up with.
Step 2. Define the Problem:
After observing the problem, write down a clear problem statement that is acceptable to all team members.
Step 3. Ask the “Whys for 5 times?”:
Answer at least five levels of “whys.” This seems to be easy, but sometimes it turns out to be the difficult part. The key part of this step is to start with the right question. The team can adapt two types of approaches in this step, such as single lane 5 Whys or multiple lane 5 Whys.
Single Lane Process
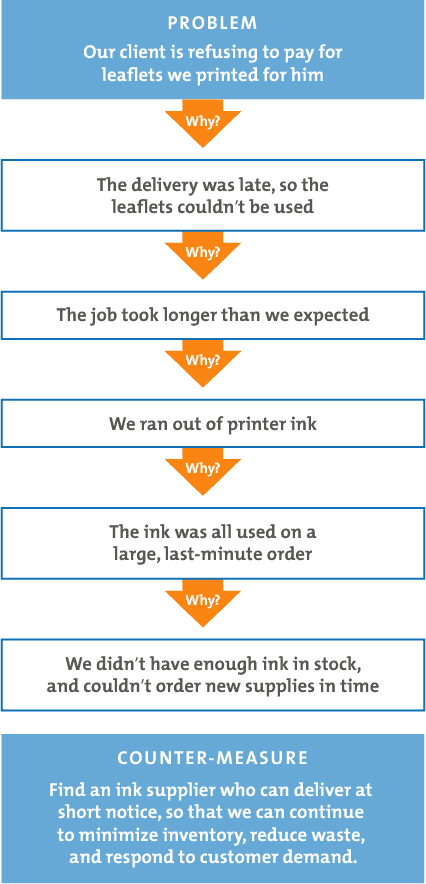
Multi-Lane Process
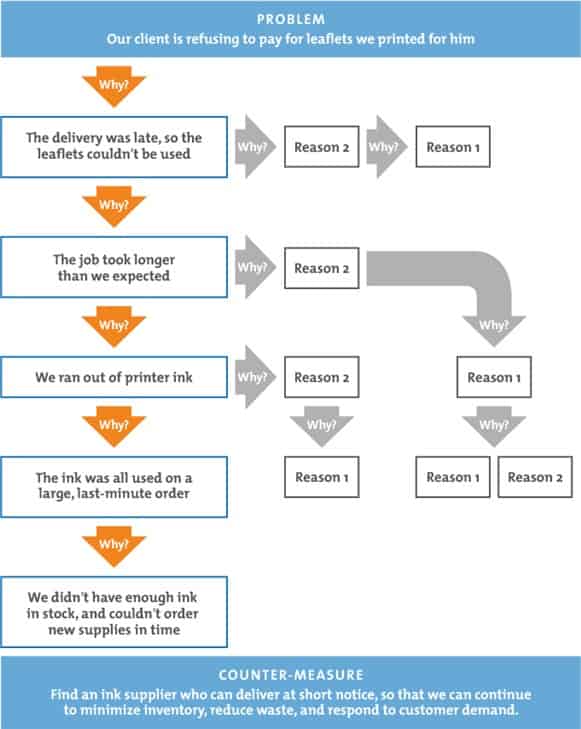
Step 4: Addressing root cause and assigning responsibilities:
After identifying the true root cause of the problem, the team needs to discuss and agree on the practical and the most effective countermeasures that fit their case to prevent the recurrence of the problem.
Step 5. Monitor the measures:
Continue monitoring the countermeasures until the problem statement is eliminated effectively or completely. Repeat the steps of 5 Whys if necessary to ensure that you’ve identified the correct root cause.
Jefferson Memorial Example
Limitations of the 5 Whys
5 whys will not help us analyze the root cause if the cause is unknown. We cannot reach the countermeasure if the person or team doing this type of analysis doesn’t know the problem or provide meaningful answers to the questions. Sometimes assumptions that we make in each step might not be the real underlying cause of the problem–there may be more causes to the problem. Also, the 5 Whys are clearly unable to differentiate between causal factors and root causes, and the lack of rigor where users aren’t required to test for sufficiency of the root causes generated by the method. The success of this method completely depends, to a degree, upon the skill with which the method is applied.
5 Whys make use of the countermeasures approach rather than giving priority to a solution approach. In countermeasure, which is a robust method, a set of actions are taken to prevent the reappearance of the root cause problem. Still, in the case of the solution approach, we have to give priority to symptoms by finding out the real solution for the root cause rather than preventing it from recurring.
In industries such as nuclear, health care, aviation, and aerospace, the 5 Whys are inadequate for problem-solving and need more advanced root cause analysis techniques.
Additional Videos
When you’re ready, there are a few ways I can help:
First, join 30,000+ other Six Sigma professionals by subscribing to my email newsletter. A short read every Monday to start your work week off correctly. Always free.
—
If you’re looking to pass your Six Sigma Green Belt or Black Belt exams, I’d recommend starting with my affordable study guide:
1)→ 🟢Pass Your Six Sigma Green Belt
2)→ ⚫Pass Your Six Sigma Black Belt
You’ve spent so much effort learning Lean Six Sigma. Why leave passing your certification exam up to chance? This comprehensive study guide offers 1,000+ exam-like questions for Green Belts (2,000+ for Black Belts) with full answer walkthroughs, access to instructors, detailed study material, and more.
Comments (2)
I’m from DC and never knew that story
It’s a neat one, right?