The history of lean tells the story of luminaries such as Toyoda, Ford, Ohno, Taylor, and many others. Read about their accomplishments and contributions.
When we talk about Lean, the first name that strikes us is Toyota. However, it is worth noting that the history of Lean started way back in the 1450s in Venice. Further, in 1799, Eli Whitney came up with the concept of interchangeable parts. Thereafter, the first person who brought the concept of Lean into the manufacturing system was Henry Ford.
Then in 1913, Henry Ford innovated the flow of production by experimenting with the interchanging and movement of different parts to achieve standardization of work. However, there were limits to Ford’s system. It lacked variety and was applied to only one specification.
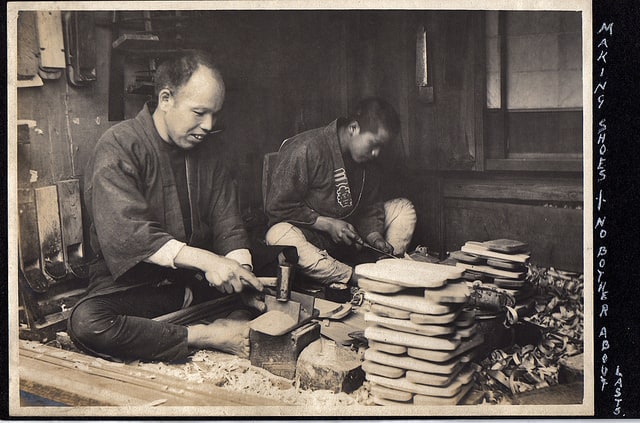
Post-World War II
It was in the following period after World War II that Toyota began to develop elements of the Lean model. Inspired by Ford’s flow of production concept, they invented the Toyota Production System. The premise of this new system is to change the focus from the use of individual machines to the workflow of the total process.
The Toyota Product System aims to reduce the cost of production, enhance the quality of products, and increase the throughput times so that the customer’s dynamic needs are met. Some of the steps that the system incorporates are the sight-sizing of the machines, keeping in mind the needed volume of production; self-regulating features of the machines so that the quality of the products is enhanced; sequencing the machines as per the process; developing quick steps so that the manufacturing of multiple parts in small comparative volume becomes possible, and keeping a strong communication of the requirements of the parts between the steps of the process.
Key Voices in the History of Lean
The concept of Lean management was continuously revived with the changing times and needs of the industry. With dynamism in the industrial environment, several Lean manufacturing proponents have made significant contributions to the field.
Frederick Taylor
Early in the 1890s, the father of scientific management, Frederick Taylor, investigated the methods and labor of factories. After his investigation, he propounded the concepts like standardization of work, time studies, and motion studies to achieve efficiency in the work methods, processes, and operations. However, he ignored the behavioral aspect of the work, which invited many criticisms against him.
- The Principles of Scientific Management: Outlines the foundation for modern organization and decision theory. He does this by describing the dilemma: workers harbor fears that higher individual productivity will eventually lead to fewer jobs. Taylor suggests deriving this fear by providing incentives for workers and re-framing the consumer, shareholder, and worker relationship. This a great and informative read for anyone interested in efficient management practices.
Henry Ford
Starting in 1910, Henry Ford pioneered his famous manufacturing strategy, making his mark in Lean history. He organized the Ford Company so that all the resources used at the manufacturing site – people, machines, equipment, tools, and products – facilitated a continuous production flow. Ford was the earliest American advocate of waste reduction (LEAN). He attained immense success through this process in manufacturing the Model T automobile. Eventually, he became the richest man in the world because of it.
However, as the world began to change, Ford could not change its work methods. The company began to fail when the market demanded new models, colors, and varieties of products. Finally, during the 1920s, labor unions and product proliferation ate away at the success of Ford. By the mid-1930s, General Motors dominated the automobile market.
Sakichi Toyoda
Sakichi Toyoda established the Toyoda spinning and weaving company in the year 1918. He was one of the initial contributors to the famous Toyota Production system, which eliminates waste via the Jidoka concept. Jidoka-automation with a human touch means facilitating quality at the source. He invented the automatic loom in 1896, which not only substituted manual work but also installed the capability to make judgments into the machine itself. The system enhanced work effectiveness and efficiency by mitigating product defects and associated wasteful work practices. The principle of Jidoka leads to early detection of an abnormality, easy stopping of the machine or process on the detection of the issue, immediate fixation of the abnormality, and even helped to investigate the root cause of the issue.
Kiichiro Toyota
Kiichiro Toyota is another important figure in the history of Lean. Many will remember him as the founder and second president of Toyota Motor Corporation. He was the son of Sakichi Toyoda, and later in 1937, he founded the Toyota Motor Corporation. Kiichiro Toyota took forward his father’s concept of Jidoka and developed his philosophy about Just-in-Time (JIT) concept in manufacturing. He paid a visit to Ford’s plant in Michigan to understand the flow of the assembly line concept. This led him to then develop the Toyota Production System. The new system aimed at right-sizing the machines concerning the actual volume needed and introduced mistake-proofing to ensure quality and proper sequencing of work processes.
Taichi Ohno
One of Taichi Ohno’s biggest achievements was integrating the Just-in-Time system with the Jidoka System. After his visit to America to study Ford’s methods in 1953, he was inspired to improve his own processes. He understood the importance of focusing on the future needs of the consumer. He realized that products need to be replenished at the same rate that consumers select them from the shelves. This inspired him to build the successful Kanban system. He even practiced the Dr. Edwards Deming method to incorporate quality at each step of the process, from design to aftersales services to the consumers. Ohno integrated this philosophy with Kiirocho’s JIT concept and the principle of Kaizen and brought it to the floor level. Hence, he is the true architect of the ‘Toyota Production System.’
TPS
The Toyota Production System relies on a number of concepts: pull system, elimination of waste, Quick Die changes (SMED), non-value added work, U-shaped cells, and one-piece flow.
The pull system defines the flow of the material between different processes as determined by the needs of the customers. The company practices the pull system by using a Kanban system, which provides a signal to the customer that the tools are available for shipment to the next process in the sequence.
The Toyota Production System also identifies the waste, termed as Muda. Additionally, it recognizes that waste is anything that does not add value to the customers. There are seven types of waste: over-production, inventory waste, defects, waiting, motion, over-processing and transportation, and handling. The system aims at identifying and eliminating these wastes to foster efficiency and effectiveness in the production system.
SMED and U-Shaped cells in the History of Lean
SMED
Another method adopted by the company is the Quick die changes (Single Minute Exchange of Dies). The aim is to improve the flow (Mura) of production. In other words, the tools and changeovers should take less than one minute (single digit) at the maximum. During the 1950s and 1960s, the company suffered from bottlenecks at the car body molding presses. The root cause was identified as the high changeover times, which increased the lot size of the production process and drove up production costs. This was especially true for the transfer of heavy-weight dies on large transfer stamping machines used to produce the body of the vehicles. Toyota implemented the SMED by placing the precision measurement devices.
U-Shaped Cells
Further, the long production lines at Toyota were wrapped using a U-shaped cell layout that facilitates Lean manufacturing. This increases the efficiency of the workers operating multiple machines at a time. The Toyota Production System (TPS) practices the one–piece flow. In other words, it produces one piece at a time instead of mass production. Toyota places a single piece between different workstations with the advantage of the least variance in cycle time and minimum waiting time. This helps to facilitate an optimum balance between different operations and mitigates over-production.
- The Toyota Way: In factories around the world, Toyota consistently makes the highest-quality cars with the fewest defects of any competing manufacturer while using fewer labor hours, less on-hand inventory, and half the floor space of its competitors. Furthermore, The Toyota Way is the first book for a general audience that explains the management principles and business philosophy behind Toyota’s worldwide reputation for quality and reliability.
Shigeo Shingo
Dr. Shigeo Shingo was an industrialist engineer and a major consultant at Toyota that successfully helped the company achieve Lean manufacturing. He mastered the Kaizen concept. He also understood the success of Lean manufacturing by integrating people with effective and efficient processes. In 1960, he developed the SMED system to achieve zero quality defects.
A Revolution in Manufacturing: The SMED System.
Written by the industrial engineer who developed SMED (single-minute exchange of die) for Toyota, A Revolution in Manufacturing provides a full overview of this powerful JIT production tool. It offers the most complete and detailed instructions available for transforming a manufacturing environment to speed up production and make small lot inventories feasible. The author delves into both the theory and practice of the SMED system. It explains the fundamentals as well as techniques for applying SMED.
Zero Quality Control: Source Inspection and the Poke-Yoke system
A combination of source inspection and mistake-proofing devices is the only method to get you to zero defects. Shigeo Shingo shows you how this proven system for reducing errors turns out the highest quality products in the shortest period of time. Shingo provides 112 specific examples of poka-yoke development devices, most of them costing less than $100 to implement. He also discusses inspection systems, quality control circles, and the function of management concerning inspection.
A Study of the Toyota Production System
Here is Dr. Shingo’s classic industrial engineering rationale for prioritizing process-based improvements over operational improvements in manufacturing. He explains the basic mechanisms of TPS and examines production as a functional network of processes and operations. Then, he discusses the mechanism necessary to make JIT possible in any manufacturing plant.
Kaizen and the Art of Creative Thinking:
Dr. Shingo reveals how he taught Toyota and other Japanese companies the art of identifying and solving problems. Furthermore, many companies in the West are trying to emulate Lean, but few can do it. Why not? Possibly because we in the West do not recognize the creative potential of every worker in solving problems. Toyota makes all employees problem solvers. Dr. Shingo gives you the tools to do it.
James Womack
James P. Womack was the research director at the Massachusetts Institute of Technology (MIT), Massachusetts. Dr. James P. Womack was born in Little Rock, Arkansas on July 27, 1948. He joined the MIT team to study the Japanese TPS system. Dr. Womack and the team flew to Japan to visit the Gemba.
In 1990, they released a book on the revolutionary manufacturing practices developed by Toyota Motor Co. entitled The Machine That Changed the World. Dr. Womack and his team identified that TPS continually creates value for customers with fewer resources. Furthermore, Dr. Womack and his team were convinced that TPS was applicable to any company in any industry in any country. So they searched for a name that would demonstrate the philosophy’s universal nature. They called it “Lean.” The name stuck.
History of Lean Videos
When you’re ready, there are a few ways I can help:
First, join 30,000+ other Six Sigma professionals by subscribing to my email newsletter. A short read every Monday to start your work week off correctly. Always free.
—
If you’re looking to pass your Six Sigma Green Belt or Black Belt exams, I’d recommend starting with my affordable study guide:
1)→ 🟢Pass Your Six Sigma Green Belt
2)→ ⚫Pass Your Six Sigma Black Belt
You’ve spent so much effort learning Lean Six Sigma. Why leave passing your certification exam up to chance? This comprehensive study guide offers 1,000+ exam-like questions for Green Belts (2,000+ for Black Belts) with full answer walkthroughs, access to instructors, detailed study material, and more.
Comments (15)
This is a wonderful video as it sunccintly explains the origins and the present day application of the lean methodology visually, and it clearly shows how sustainable the process is.
Glad you liked it, Enock!
“The principle was jikoda.”
The principle is called jidoka, not jikoda.
Wow, what a silly typo error. All fixed. Thank you for pointing it out!
Awesome read!!!! As a lean practitioner, I always look for the background to further understand what I practice.
Thanks for the kind words, Roger!
“It was only after the World War II in 1930s”… I think I missed something in my history class. 🙂
Very interesting article. Thanks for putting this together,
Hah! Yeah, that’s awkwardly phrased. Although WWII did start in the end of the 30s, most of the US audience would only think of our country’s participation in the 40s.
Hi Ted,
Probabaly you should include James Womack in the article.
Its in the official practice exam.
Thanks,
Xiang
Hi Xiang,
We can do that.
Which official practice exam are you referring to?
Best, Ted.
Hi Ted,
IASSC’s.
Best, Xiang
Xiang,
I’m still not following. To my knowledge IASSC does not publish it’s own practice test.
Best, Ted
We have added James Womack to the article. Thank you for the suggestion!
Isn’t Krafcik who was the first to introduce the term “Lean” in 1988, with his article “Triumph of the Lean Production System”?
Hi Jean-François Biron,
John Krafcik coined the term Lean in his 1988 article, “Triumph of the Lean Production System”. However, the Lean concepts were used in Ford and Toyota plants much before 1988 to maintain continuous production flow and Just-in-time.
Thanks