Critical to X (CTX) requirements are elements of a project that are important to the end customer.
As an example, think about going to buy a burger. There are several factors that you probably won’t think about much when ordering. However, you expect them in your order:
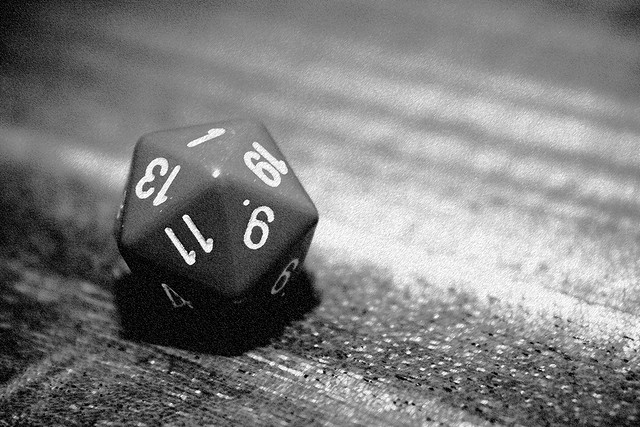
- Quality: You expect an edible, tasty burger.
- Cost: You expect to pay a certain amount for your burger.
- Delivery: You expect to receive that burger fairly quickly.
- Safety: You expect the result will not give you food poisoning.
These are all Critical to X (CTX) requirements.
Types of Critical to X (CTX) Requirements
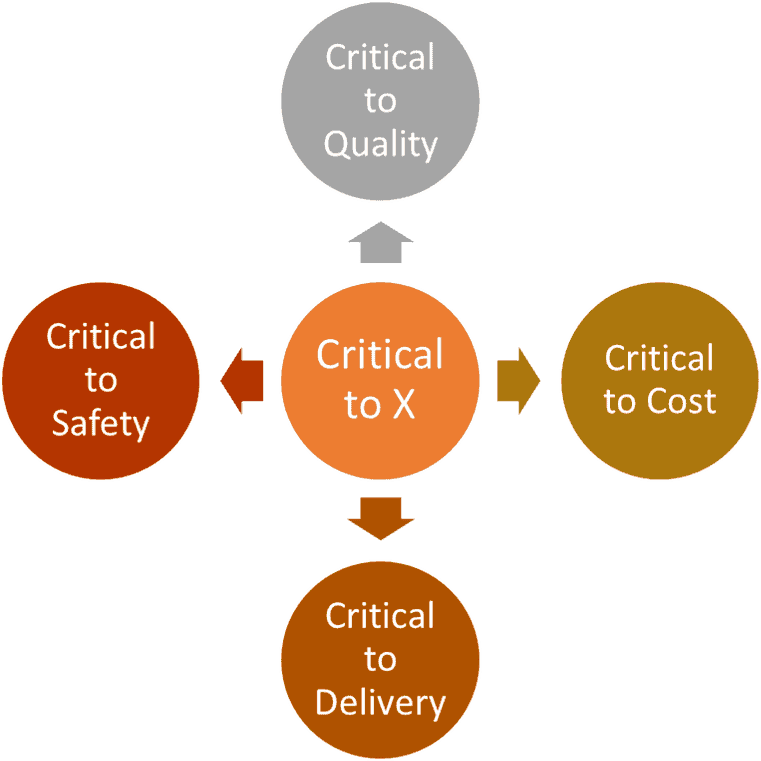
These vary in terminology depending on whose articles you read. Some include Critical to Process requirements or leave out Critical to Safety. You’ll also find that sometimes discussions of CTX requirements waver between focusing on the customer and focusing on the workplace. This is understandable but leads to losing customer orientation, which is crucial in these requirements.
There are four basic Critical to X (CTX) factors:
- CTQ: Critical to Quality
- CTC: Critical to Cost
- CTD: Critical to Delivery
- CTS: Critical to Safety
CTQ: Critical to Quality
Critical to Quality (CTQ) is like a compass for any organization seeking to achieve true customer satisfaction. It’s not just about meeting some generic standard; it’s all about the exact attributes of your product, process, or service that are absolutely essential for your customers. CTQs can include physical measurements such as weight, height, length, depth, etc.
Identifying CTQs involves listening intently to the customer requirements. What are their needs, preferences, and pain points? What aspects, if not addressed, would instantly turn them away? By gathering this crucial intel, you can translate those often unspoken desires into concrete, measurable CTQs.
CTQs are often determined through interactions with customers and stakeholders, considering their needs, preferences, and specifications. These critical characteristics are the factors that, if not met at the desired level, would result in dissatisfaction or a failure to meet the intended purpose.
CTC: Critical to Cost
Critical to Cost (CTC) encompasses the elements influencing how costs affect customers. While resembling one of the CTX, CTQs, customers distinguish CTCs to articulate their precise requirements. For example, the weight of a product: if a customer expects a product’s weight to fall within the range of 50 to 60 pounds, any deviation beyond these limits is perceived as negatively impacting their specified requirements.
Critical to Cost (CTC) pertains to the factors or components within a product, process, or service that substantially influences its overall cost. Recognizing what is critical to cost is imperative for businesses to oversee expenditures and allocate resources judiciously and proficiently. Concentrating on the elements that wield the greatest impact on costs empowers organizations to make well-informed decisions, leading to the optimization of both their processes and products.
Critical to Cost Example
For example, take a business that manufactures sheet metal. The following costs to its customers apply:
- The wholesale price for 0.5-inch thick hot-rolled, uncoated raw steel is $100-120/sheet.
- Delivery costs are $100 per 100 sheets.
- If the customer uses one of the company’s resellers, they’ll pay a 7-10% markup.
- Customers must perform sampling and inspections on each load to ensure quality control. The estimated cost–materials, labor, and time–for this QC is $100 per 100 sheets.
- Because it provides wholesale products only, and most customers are in the same country, there are minimal taxes and duties.
- Most of its customers use only one or two resellers for their sheet metal, so the cost of procurement is not high.
CTD: Critical to Delivery
Critical to delivery (CTD) are the requirements stated by customers, specifically concerning product or service delivery. Customers often identify and articulate CTD requirements to ensure that the delivery meets their expectations and organization needs. Organizations can prioritize and optimize their processes to meet customer expectations, minimize delays, and enhance overall satisfaction by identifying and understanding what is critical to delivery.
A few examples of Six Sigma projects that address one of the CTX: Critical to Delivery requirements are:
- Improving a process to decrease time wastage (faster production).
- Researching courier companies with the end goal of offering a same-day delivery service.
- Changing the packaging products used to decrease parcel breakages in transit.
CTS: Critical to Safety.
Critical to Safety, or CTS, refers to the elements that, if not executed accurately or if they falter, have the potential to result in substantial injury, loss of life, or environmental harm. This applies to everything from products and processes to systems and even human actions. In other words, Critical to Safety requirements are based on the safety concerns of customers. These might include industry safety standards and workplace health and safety (OH&S) rules.
Examples of Critical to Safety Requirements
We can use the customer drivers mentioned above to create example CTS requirements:
- Make all toy parts from fabric, no hard plastics.
- Minimum machine bench height of 4′.
- You can package multiple order items in the same box if the combined weight of items, box, and padding does not exceed 30 pounds.
Critical to X (CTX) and Six Sigma
Six Sigma projects can aim to improve any of the Critical to X (CTX) requirements. For example, a project might improve a process and decrease the end cost of a product by 10%. Hence, it would meet a Critical-to-Cost requirement. Or, it might focus on finding a new supplier for a key material, decreasing production costs. As a result, it could also decrease the end product’s price, again meeting a CTC requirement.
Keep in mind that these are customer-centric requirements. That means you need to be able to show a clear benefit to the customer. This includes any project that is supposed to address CTX.
Other helpful Critical to X (CTX) Links
When you’re ready, there are a few ways I can help:
First, join 30,000+ other Six Sigma professionals by subscribing to my email newsletter. A short read every Monday to start your work week off correctly. Always free.
—
If you’re looking to pass your Six Sigma Green Belt or Black Belt exams, I’d recommend starting with my affordable study guide:
1)→ 🟢Pass Your Six Sigma Green Belt
2)→ ⚫Pass Your Six Sigma Black Belt
You’ve spent so much effort learning Lean Six Sigma. Why leave passing your certification exam up to chance? This comprehensive study guide offers 1,000+ exam-like questions for Green Belts (2,000+ for Black Belts) with full answer walkthroughs, access to instructors, detailed study material, and more.
Comments (4)
Do u have CSSBB quesition bank for practicing purpose.
Hi Praful,
Actually, yes, I do have a question bank that I am getting ready to release. Make sure that you are on the email list (see sign up on the right side of the website) so that you are the first to know once it goes live.
In the meantime, I have links to several other free CSSBB question banks here.
Let me know how else I can help.
I completely agree with the author’s argument that CTX is a crucial factor in determining the success of a project. As a project manager myself, I have seen firsthand how a lack of clear goals and priorities can lead to confusion and waste of resources. I appreciate the author’s insight into this topic and look forward to seeing more of their work in the future.
Thanks for the kind words.