Critical to-delivery requirements revolve around delivering a product successfully to a customer. When a customer makes an order, there are several expectations they might have around the delivery of it:
- They’ll receive the correct number or weight of products.
- You’ll deliver on the agreed date and time. Or, you’ll deliver within a standard time frame.
- You’ll package the product to suit the delivery method.
- They will receive prompt answers to any questions about the order.
- You’ll keep packing and shipping costs reasonable.
- They’ll receive the product in good order (undamaged).
If you fail to meet CTD requirements, you can essentially invalidate the entire sale. Your product might be high in quality. It might be competitively priced. But if you can’t deliver to customer requirements, at best, you’ll have an unhappy customer. At worst, their need for the product was time-critical, and they no longer want or need it.
Critical to Delivery Example
Imagine that you need to bake a cake for a birthday party. You order the cake tins, cake mix, and fondant you’ll need to create it. The supplier is supposed to deliver the materials two days before the birthday party, giving you time to bake the components of the cake and decorate it.
This is the timeline you need to follow:
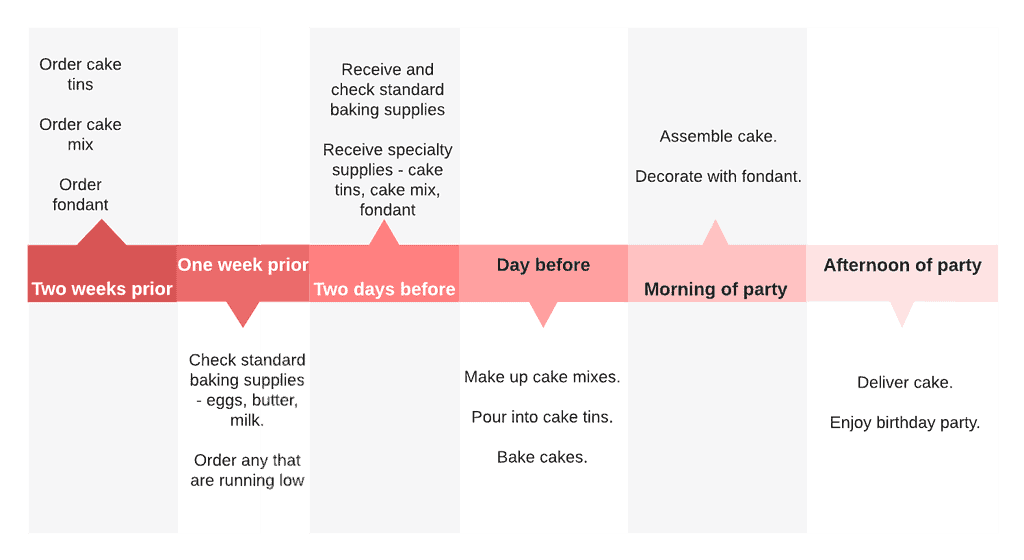
Your specialty supplier misses the deadline. You can’t find the materials locally. Instead, you have to go out and buy a ready-made cake.
The supplier delivers your materials two days later – the day after the party. You have exactly what you ordered. The tins, mix, and fondant are of the best quality. You paid a good price for them. They’re safe to use. However, you have no use for them now. The party is over, and you can’t go back in time to bake the cake for it. Your Critical to Delivery requirements weren’t met.
CTD and Just-in-Time Inventory
The rise of just-in-time inventory makes CTD requirements even more important. Popularized by Lean methodology, just-in-time inventory espouses keeping only the essentials available and just what is needed for what you’ll be working on. For example, a company that produces sheet metal might only stock enough raw steel to supply a week’s manufacture. Because it gets deliveries twice a week, it can easily keep up with demands. And this way, it’s not warehousing materials unnecessarily.
That’s the good side of just-in-time inventory. The flip side is that if Critical-to-Delivery requirements aren’t met, the company can be left without the materials it needs to continue production. We’ve seen examples of this exact situation in the recent COVID-19 pandemic. Disruptions to international trade, shipping, and local deliveries have all contributed to cause issues for many industries.
With many companies adopting Lean strategies, meeting your Critical to Delivery requirements is more important than ever.
How to Develop Critical to Delivery Requirements
We can use a few different methods to put together expectations around delivery:
- Industry standards: Many industries will already have best-practice delivery requirements.
- Service level agreements: Larger customers will often have SLAs that they expect vendors to adhere to.
- Competitor guarantees: What terms are your competitors currently offering? For example, an online store might offer free express postage or courier service.
- Customer canvasing: Talk to your customers and target market to find out what they expect.
You can then use a similar concept to a CTQ tree to assemble CTD requirements from these expectations. Often, you’ll only need two levels of ‘branches,’ though, as corporate customers will tend to have quite detailed expectations, eliminating the first, vaguer tier.
Turning expectations into requirements
Customer expectations come from the customer’s perspective. To turn them into CTD requirements, we need to flip them into the producer’s perspective. For example:
- Customer expectation: Product received within three business days of order.
CTD requirement: Product sent via express post service within one business day of order receipt and payment. - Customer expectation: Fragile products will be suitably wrapped to avoid breakage.
CTD requirement: Wrap fragile products in two layers of bubble wrap and ship in a cardboard box (not a satchel).
‘Go to the Gemba’
This Lean concept involves looking at how your staff actually have to work – not the ideal situation. CTD requirements, in particular, need a lot of realism. Before setting your requirements and processes in place, ensure they fit your staff’s environment. Go to the ‘Gemba’ – the place where the work happens. See how packaging and shipping processes are working for your staff.
It’s important to note that ‘go to the gemba’ and ‘micro-managing staff’ are two very different things. Your staff might well fear that you’ll be peering over their shoulders and finding fault. Make sure they realize, instead, that this is an opportunity for them to help you understand their working conditions.
Points to remember
When turning customer expectations into CTD requirements, make sure that they fit these criteria:
- Actionable: Staff can follow the requirements.
- Measurable: You can measure the results objectively.
- Clear: Staff understand exactly what is needed.
- Achievable: Staff can meet the requirements without undue pressure.
Example CTD Six Sigma Projects
Some examples of Six Sigma projects that address Critical to Delivery requirements are:
- Improving a process to decrease time wastage (faster production).
- Researching courier companies with the end goal of offering a same-day delivery service.
- Changing the packaging products used to decrease parcel breakages in transit.
When you’re ready, there are a few ways I can help:
First, join 30,000+ other Six Sigma professionals by subscribing to my email newsletter. A short read every Monday to start your work week off correctly. Always free.
—
If you’re looking to pass your Six Sigma Green Belt or Black Belt exams, I’d recommend starting with my affordable study guide:
1)→ 🟢Pass Your Six Sigma Green Belt
2)→ ⚫Pass Your Six Sigma Black Belt
You’ve spent so much effort learning Lean Six Sigma. Why leave passing your certification exam up to chance? This comprehensive study guide offers 1,000+ exam-like questions for Green Belts (2,000+ for Black Belts) with full answer walkthroughs, access to instructors, detailed study material, and more.