Lean metrics are the measures that can be used to control and monitor the manufacturing processes such that continuous quality can be facilitated by identifying opportunities for improvements and changes. Before we make an effort to reduce or mitigate waste and move towards lean management, we must know how to measure them.
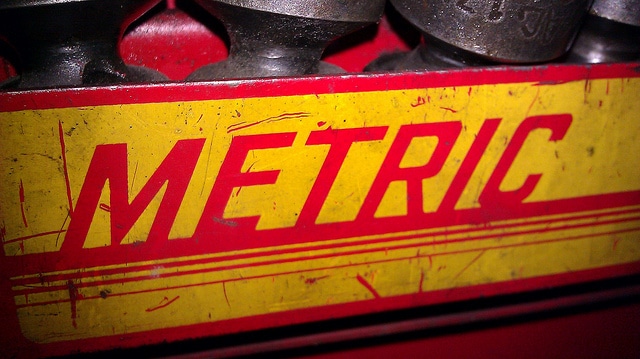
The lean metrics pinpoint and measure the magnitude of waste and the variables causing customer dissatisfaction. This augments the potential opportunities for improvement. Every business charter must incorporate some of these lean metrics per the project’s goal.
The objective of lean manufacturing is to minimize waste and enhance the speed of operations. By reducing waste, one is able to deliver efficient and effective products and services to customers. Enhancing the speed reduces the flow time to serve the customers.
Little’s Law
Little’s Law equates the flow time in terms of work-in-progress inventory in units and the average completion rate computed in units per time period.
The throughput rate is also known as the flow rate. It’s the same as the average completion rate. In the book publishing example in the next section, we use the throughput rate for the entire end-to-end publishing operation. The throughput rate calculates the rate at which the flow of units passes from a particular process in the manufacturing unit. The maximum throughput rate is the capacity of the process.
This Little’s law states:
L = λ * W
Where:
- L = the average number of items in a queuing system (works in progress).
- λ = the average number of items arriving at the system per unit of time (average completion rate, throughput rate, or flow rate).
- W = the average waiting time an item spends in a queuing system (flow time).
We can also write Little’s Law like this:
WIP = Flow Time * ACR
Where:
- WIP = work in progress inventory in units.
- ACR = Average completion rate in units per time period.
For instance- in a publishing house, the staff can print of about 100 books daily, while there are 500 books in various stages of the printing department. This is because there are five different processes that each book has to go through:
- Page Printing
- Cutting
- Binding
- Trimming
- Quality Assurance.
Each of these processes can handle 100 books/per day, and each process needs to occur on a separate day for a single book. For example, after binding, the glue needs to dry before the book can be trimmed.
Applying the Little’s law equation:
WIP = Flow Time * ACR 500 = Flow Time * 100 Flow Time = 500 / 100 Flow Time = 5 days
Hence, we can expect that any new order of under 100 books trusted to the Printing Department would take 5 days to be completed.
It should be noted that you can reduce flow time by reducing the number of items going through (to a point!) or increasing the average completion rate. For example, by improving processes or decreasing wait times between processes.
Example
Suppose the publishing house performed a Value Stream Mapping (VSM) event and identified the kaizens to improve the process. Let us say the team came up with process improvements like standard work creation, installation of advanced machinery, etc, to decrease the wait times between the process. Now the new processes can handle 142 books/day.
Applying the Little’s law equation:
WIP = Flow Time * ACR 500 = Flow Time * 142 Flow Time = 500 / 142 New Flow Time = ~3.5 days
Cycle time
Cycle time is the average time taken to complete a process per item. It is calculated as the reciprocal of the throughput rate. In other words:
Cycle Time = 1 / ACR
In the book publishing example, the throughput rate was 100. So:
Cycle Time = 1 / ACR Cycle Time = 1 / 100 Cycle Time = 0.01 days
Note that cycle time does not give you the amount of time it will actually take to manufacture an item. It gives you the average per item instead.
Touch Time
Touch time represents the total time individuals truly spent working on a unit or task. It does not include the waiting time, break time, email writing, etc. Whereas Cycle time is the amount of time taken to complete a specific task from start to finish.
Touch time should consider only actual activities, hence use time study to measure the touch time and avoid accounting for non-value-added activities. From the above example, use time study to capture the actual time the operator spent on page printing, cutting, binding, and trimming.
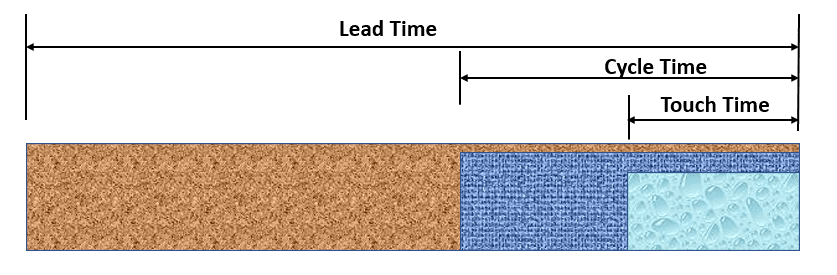
Flow Time
Little’s Law says:
WIP = Flow Time * ACR
Now, the average completion rate is the same as the throughput rate. And as we’ve seen, this is the inverse of cycle time. So we can substitute ACR with 1/cycle time. Thus,
WIP = Flow Time * 1/Cycle Time WIP = Flow Time / Cycle Time
Hence:
Flow Time = WIP * Cycle Time
Let us understand this using an example. In the example of the publishing house, the WIP is 500 books, and the cycle time is 0.01 days. So:
Flow Time = WIP * Cycle Time Flow Time = 500 * 0.01 Flow Time = 5
The flow time for this example is 5 days.
Flow time vs. cycle time
Flow time is the amount of time it takes a single unit to get through the whole manufacturing operation.
Cycle time is the average time it takes to get units through the whole manufacturing operation per unit.
Cycle time will typically be much lower than flow time. On the surface, this might seem ridiculous. Keep in mind, though, that you’re typically dealing with large volumes of items. Using the book example above, it might take 5 days to produce a book, period. Up to 100 books can be worked on at any stage. If you wanted to produce 100 books, it would take 5 days. However, if you wanted to produce a single book through that manufacturing operation, it would still take 5 days.
That’s why we differentiate between flow rate and cycle time: sometimes you need to know the minimum amount of time required to produce a single item (cycle time); sometimes you need to know how many items, in bulk, you can produce in a particular time period (flow time).
Work In Queue
The Work In Queue is the common lean metric in a production environment. In a manufacturing plant, the work in queue refers to the job didn’t complete or the process didn’t start yet. In other words, a job is made to wait before processing. If the work-in queue time increases, the work-in-process (WIP) inventory and lead time drastically increases.
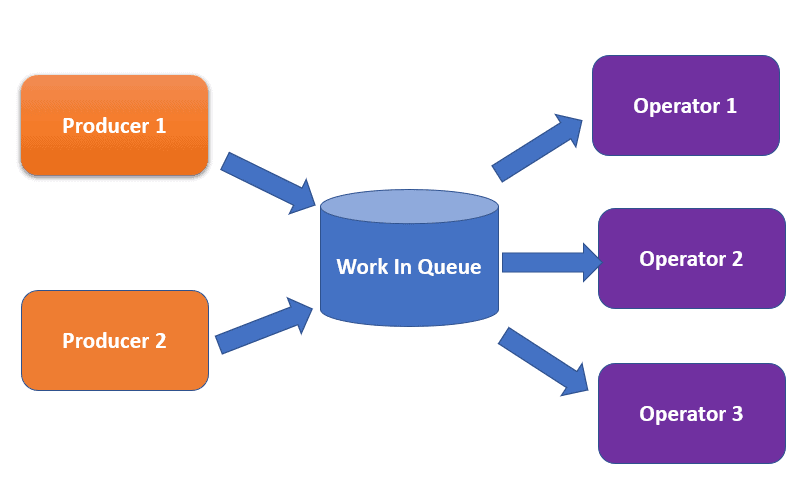
Total Lead Time
Lead time is the total time taken for the work to process from one point to another in the manufacturing process. It is calculated as the time between two points, known as starting point and end point. There can be many lead times in an organization: customer lead times, development lead times, etc. Calculate the total lead time by calculating the total time one unit of the product takes to travel between all the processes in a manufacturing process. It includes the sum of all the process lead times and the waiting times between different processes.
Total lead time = Sum of process lead times + sum of queue times
Lead time for an individual process is the same as flow time and as per Little’s Law principle. It can be calculated by dividing the number of items in the work process by the average unit completion rate per time period.
Process Cycle Efficiency
The process cycle efficiency helps to detect how much of the process is actually adding value to the entire process.
Process Cycle Efficiency = Value-added time / Lead time
For instance – In a publishing house, the lead time to produce books is 40 hours, and the value-added time for various processes such as printing – is 8 hours, Cutting- is 4 hours, and Binding – is 6 hours. What is the Process cycle efficiency?
Value added time = 8+4+6 = 18 hours Lead time = Value added time + Delays (Waiting time) = 40 hours Process Cycle Efficiency = Value-added time / Lead time =18/40 = 45%
The process cycle efficiency varies in the application, but a process is lean when the process cycle efficiency is above 25 percent.
Important Lean Metrics Videos
When you’re ready, there are a few ways I can help:
First, join 30,000+ other Six Sigma professionals by subscribing to my email newsletter. A short read every Monday to start your work week off correctly. Always free.
—
If you’re looking to pass your Six Sigma Green Belt or Black Belt exams, I’d recommend starting with my affordable study guide:
1)→ 🟢Pass Your Six Sigma Green Belt
2)→ ⚫Pass Your Six Sigma Black Belt
You’ve spent so much effort learning Lean Six Sigma. Why leave passing your certification exam up to chance? This comprehensive study guide offers 1,000+ exam-like questions for Green Belts (2,000+ for Black Belts) with full answer walkthroughs, access to instructors, detailed study material, and more.
Comments (4)
Under the paragraph of Little Law”For instance- in a publishing house, the staff can complete printing of about 100 books (daily)”
I think this adverb between bracket has to be added to be comprehended
Good catch, Ali. Thank you. Updated!
i think you need to swap the flow time and cycle time in the brackets…
“minimum amount of time required to produce a single item (flow time); sometimes you need to know how many items, in bulk, you can produce in a particular time period (cycle time)”
Thanks, Laki for the feedback, we have updated the article.
Thanks