The Theory of Constraints is system-based philosophy that states that the constraint determines the performance of the systems. In other words, It is a methodology for identifying the most important limiting factor (i.e., constraints) that stands in the way of achieving a goal. Then the teams will work to decrease its influence until it is no longer the limiting factor.
Examples of organizational constraints: Machines, people, policies, information, material, etc.
The Theory of Constraints is based on a system developed by Goldratt in the year 1984. His book, The Goal, describes a process of ongoing continuous improvement.
3 Basic Measures are more indicative of the systems than Machine Efficiency, equipment utilization, downtime, or balanced plants.
- Throughput
- Inventory
- Operational Expenses
Overview of the Theory of Constraint
The premise of the theory of constraints is that organizations can measure and control variations based on three factors: throughput, operational expense, and inventory. According to the Theory of Constraints, the goal of a company is to make money.
Most constraints are NOT physical. They are the result of company practices.
Thus, you should focus your energy on lowering operating expenses, inventory, and investment while increasing throughput. This mindset should be applied to the entire operation to identify and expand the critical constraint.
Define the goals of the company along with metrics for critical measures.
Some Key Pieces
- Bottlenecks: watch these and try to eliminate them. Beware of additional lost productivity due to NIGO or poor quality.
- Balanced Plants: Not always a good thing. Don’t balance capacity with demand; balance the flow of the product with demand. Make the flow through the bottleneck equal to market demand.
- Throughput
- Inventory
- Operating Expenses
- Results
- Goals
- Assumptions
- ROI
- Cash flow
- Lead times
- Reduction of batch sizes
- Cost accounting
- Fear of Change
- Resistance
- Net Profit
Focus areas of the Theory of Constraints
- Identify the System Constraint: This is the first step. Team to identify the part of a structure that creates its weakest link.
- Exploit the Constraint: Goldratt, in his book, says to get as much out of the identified constraint component as possible without experiencing negative changes.
- Subordinate everything else: In this step, adjust the non-constraint components to a setting allowing the constraint to function at the greatest possible efficiency.
- Elevate the Constraint: Elevating the constraint refers to taking whatever action is necessary to remove the constraint. In other words, this can be done by investing more resources such as materials, machines, operators, etc.
- Finally, lock in the gains and monitor the new constraints.
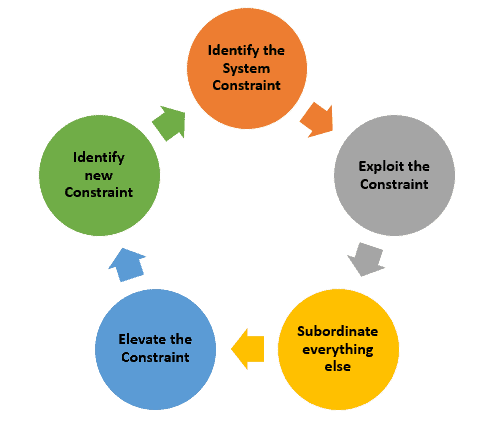
Lean and Theory of Constraints
The Theory of Constraints views all processes as a chain of events that operates in a particular order. Remember, a chain is only as strong as its weakest link. Well, a 5-step process is only as productive as its slowest step.
It does not matter if steps A and B can output 15,000 products daily because step C can only output 10,000. In addition, even if steps D and E can handle more than 10,000 a day, that’s still all they get handed off from C. So, step C is a constraint on the chain or system.
The Theory of Constraints views the extra 5,000 products a day produced by steps A & B as waste because the cost of both producing and storing the extra parts is waste. Any extra machinery or people in A & B or D & E are waste. A common problem with Lean Six Sigma is project selection, often improving the efficiency of steps A or D because they find “low-hanging fruit.” These improvements are pointless because the system can still only function as well as step C, so the cost of those projects is also waste.
How Lean, the Theory of Constraints, and Six Sigma work together
The Theory of Constraints helps you find the constraints, Lean (and ToC) helps you improve them, and Six Sigma helps you remove any errors. Additionally, ToC introduces buffers to protect your constraint, so even if a machine in step B goes down, you still have a little buffer of parts for step C to work on until it’s back up (remember the whole process can only work as fast as step C, so if you don’t keep it busy then steps D & E will run out of things to do and stop). Buffers and ToC have a ton of other advantages, and I highly recommend you look them up further.
Thinking Processes in the Theory of Constraints
In the service and operation industry, it is difficult to visualize the constraints in the workflow. Six Sigma teams to explore methodologies to achieve organization goals.
Thinking Processes help to identify the root cause of a problem by reviewing the symptoms systematically. These root causes are called undesirable effects (UDEs). Organizations get the picture of the situation by arranging these responses in a tree diagram.
The Thinking Processes following three questions of the Theory of Constraints:
What needs to be changed?
- Current Reality Tree: The current reality tree shows the current state. In other words, things need to be improved. First, you collect the UDEs of the problem and then arrange for them to be tracked back in order to find the root cause of the problem.
What should it be changed to?
- Future Reality Tree: A future reality tree shows the future state. It shows the current reality tree, along with new ideas called injections. These injections create desirable effects.
- Negative Branch Reservations: When you work on your future reality tree, often few may be concerned about the injections’ consequences.
- Evaporating Cloud Tree: This is one of the important trees. It helps discover all the conditions that need to be in place for injection success. This is the preliminary step while creating the future reality tree. This helps to overcome issues in implementing injections.
How to change it?
- Strategy Tree and Tactics Tree: Strategy Tree and Tactics Tree shows the implementation plan for the future state. In other words, it helps to diagram the outcome of an improvement. Six Sigma teams identify the problems and explore the options to overcome obstacles.
Drum Buffer Rope
Drum buffer rope is a Theory of Constraint solution for scheduling and managing operations with constraints. In other words, it is the method of coordinating production while focusing on reducing inventory and WIP.
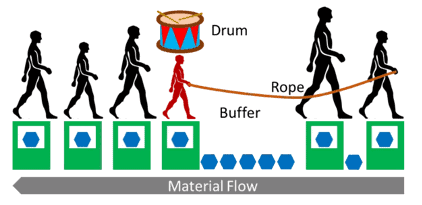
- Drum: Pace of the process or sets the production pace
- Buffer: It is the level of inventory needed to maintain consistent production
- Rope: Method to limit upstream production. In other words, a signal is generated from the buffer to release the material.
The drum buffer rope method works well, especially in manufacturing with various product models, process times, and flow. It provides the highest organizational efficiency because it controls production and maintains the inventory and WIP very low.
Example:
Let’s assume we have four processes in a manufacturing shop. Mixing, machining, assembly, and shipment to the end customer. Each of the processes has different capacities, as indicated below.
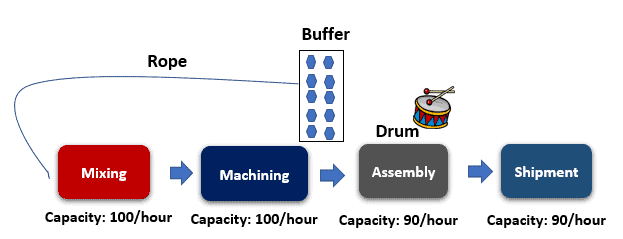
The above diagram shows that the assembly process is the bottleneck; it had only 90 pieces per hour. We can ship 90 pieces to the shipment area with ten pieces in inventory. Since the assembly is the constraint, it is the drum.
The buffer is the ten extra pieces that have completed the machining process, and we need to maintain a certain level of inventory before the assembly process. Suppose the mixing or machining process produces fewer pieces than their capacity. The inventory may go down before the assembly stage. As soon as the inventory decreases, the rope mechanism triggers the front to release more pieces.
Benefits of Theory of Constraints
- The primary goal of many companies is to improve profits. It provides a powerful set of tools for achieving organizational goals.
- Optimizing the constraints enables more products to be delivered.
- It enables faster product flow and thus reduces lead times.
- Optimizing the constraints will lead to less WIP or inventory.
- It improves the communication process within the organization.
Theory of Constraints Videos
Theory of Constraints Reading List
Great introduction to the Theory of Constraints.
Six Sigma Black Belt Certification Theory of Constraints Questions:
Question: Which of the following statements is true about the theory of constraints? Taken from (ASQ sample Black Belt exam.)
(A) It views a system in terms of discrete processes.
(B) Most constraints are physical.
(C) Most constraints are the result of policies.
(D) It focuses on continuous improvement.
Answer:
C: Most constraints are not physical (eliminating b) and are a result of policies (c). A is false and D is too generic.
Comments (2)
Hi Ted,
In the Drum, Buffer and Rope model, it says for the Rope it means “the Method to limit upstream production. In other words, a signal is generated from the buffer to release the material.”
Does that mean whenever the Buffer become less, then Material (Ending Product) the back up Inventory will release apart from the production process?
Thanks,
Wilson
The rope is how we control the release of new work. The idea is that if the constraint sets the pace, the drum beat, for the entire operation, then we should only release work at the rate that the constraint can consume it. Rope buffers drum. If we release work faster than the constraint can consume it, then WIP piles up.
The best example is, in a hospital waiting room. If the time the doctor takes to see each patient is the Drum, then the Buffer can be the receptionist scheduling appointments so there are always two or three patients in the waiting room. The Rope is the nurse calling in each patient once the doctor is ready to see them.
Thanks