What is Evolutionary Operations Methodology (EVOP)
An Evolutionary Operation Methodology is a statistical method that is used to improve the process or product quality. We also refer to them as EVOP and Design of Experiment (DOE). This process was first developed by George Box in 1957.
The basic purpose of the evolutionary operations methodology (EVOP) is to improve a process through systematic changes in the operating conditions of a given set of factors. An experimental design is established and conducted through a series of phases and cycles. The effects are tested for statistical significance against an experimental error when such an error can be calculated.
When we find a factor to be significant, we reset the operating conditions for that factor. Then, we conduct the experiment again. This process continues until no further gain is achieved. Hence, the concept of evolution is established.
The basic two components of Evolutionary Operations:
- Variation
- Favorable variants selection
When Would You Use Evolutionary Operations Methodology (EVOP)?
Evolutionary Operation (EVOP) is the best DOE process for manufacturing-related operations. This process allows continuous improvement and entails small incremental changes in parameters. By the same token, we ensure that we generate little or no process scrap.
Application of EVOP is especially suitable when:
- The system had more number of product performance conditions.
- The process had 2 to 3 process variables.
- The performance of the process changes over time.
- Process calculations need to be minimized.
Static Operations and Evolutionary Operations
In a regular manufacturing environment, the plant runs as per defined operational conditions. In other words, executing the operations as per the “standard work.” As a matter of fact, the manufacturing facility always insists the operators perform the operation under predefined conditions. Likewise, this is called the Static operation method.
The static operation method improves productivity, but apart from productivity, monitoring of product physical properties is also equally important. These physical properties may exceed specification limits if we allow random deviations from the standard work.
With properly planned Evolutionary Operations, the regular production runs each of the variants and continually repeats the cycle. Since the cycle of variants follows a simple pattern, the persistent repetition of the process allows evidence concerning the yield and physical properties of the product.
Since a very small incremental change in process parameters, Evolutionary operation does not require any special concessions or resources. In this way, the regular production process generates the product and the information required for further improvement.
Evolutionary Operations process steps
- Define process performance characteristics that we need to improve.
- Identify process variables whose small changes will then lead to the process improvement and record their current condition.
- Plan the incremental changes steps (must be small steps; hence they will not impact the production) for each identified process variable.
- For each variable, mark the initial set of values as corners of the simplex. For two variables, it’s a triangle, and use a tetrahedron for three variables).
- Perform one run at the current condition and also perform two runs with small incremental changes of one or both of the process variables.
- Record the results and identify the least favorable result from the runs; in other words, identify the least favorable corner.
- Then, perform a new run from the least favorable corner (which is the reflection or mirror image of the least favorable run).
- Now identify the new least favorable condition, this run will replace the existing one and also leads to another new run, and this process will go on.
- The process starts at the initial operating condition and moves on till we achieve more favorable results.
Example of Evolutionary Operations Methodology (EVOP)
During the Improve phase of DMAIC Evolutionary Operations Methodology improves a process through systematic changes in the operating conditions of a given set of factors
Example:
“ABC Chocolate” production unit reported nearly 21.4% rejection which led to more rework, affecting the delivery schedules and also customer satisfaction level.
The team realized that the process would improve if the two important parameters air pressure of the machine (in psi) and also if they adjust the belt speed (RPM) settings.
- Identify process performance characteristics. For example, the reduction of scrap and the current rejection rate is 21.4%.
- Identify process variables whose small changes will lead to process improvement. I.e., Air pressure of the machine (in psi) and belt speed (RPM).
- The initial air pressure is 120 psi, and also belt speed is 40 rpm.
- Plan the incremental changes steps for each identified process variable – An increase in 10 psi as well as 5 RPM might lead to improving the process and reducing the rejection.
- For instance, the initial run is 120 psi and 40 rpm, and 2nd and 3rd runs are 130 psi, 45 rpm, and 140 psi, 50 rpm, respectively, and reported the rejection rate.
The corresponding results are:

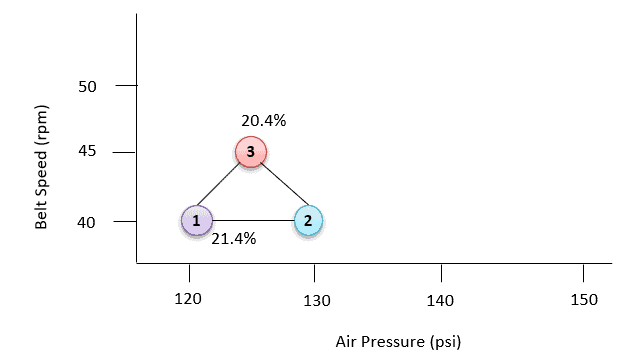
- Following the above picture and table, we can clearly see that run 1 is the least favorable. In other words, the highest rejection rate. So, initiate a new run reflection or mirror image of run 1, i.e. new run 4.

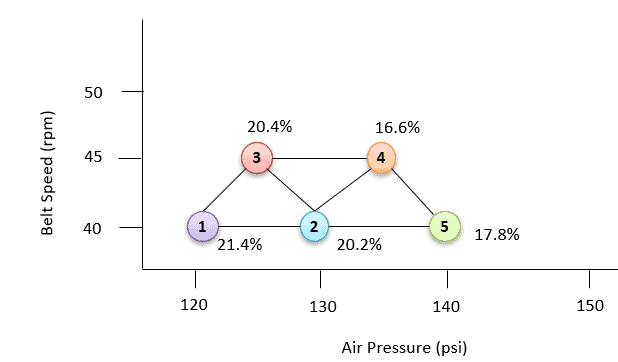
- Following the above picture and table, it is clear that run 3 is the least favorable. So, run 5 mirror image of run 3.
Procedure to calculate the new run value
New run value = (good value of process variable 1+ good value of process variable 2 – the value of least favorable process variable).
Example: Calculate the run 5 value (from 2,3,4)
- Run 5 Air pressure value = (value 4+value 2 -value 3)= (135+130-125) = 140
- Similarly, Run 5 Belt speed value = (value 4+value 2 -value 3) = (40+45-45) =40
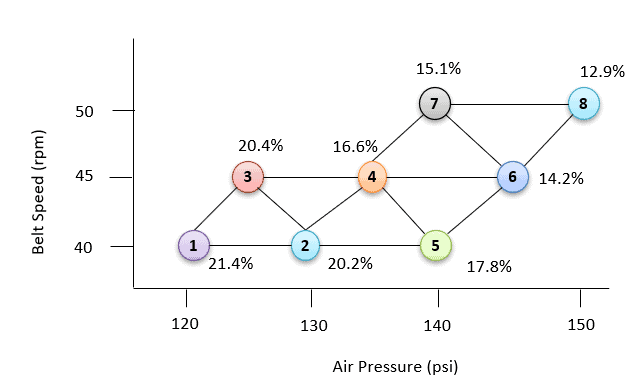
- Similarly, follow the process and run the experiment till the expected rejection rate is achieved.
Helpful Links:
http://asq.org/quality-progress/2015/01/statistics-roundtable/evop-an-underused-technology.html
Comments (2)
Hi!
In the example you give, you show the simplex method, which is not EvOp. EvOp uses full factorial designs with and without center points.
Just wanted to point that out, and it is important that the readers understand the difference
Cheers
Alejandro
Hi Alejandro,
Yes, It’s a Simplex design for EVOP. The types of designs which are commonly used with EVPO are 2 ^2 or 2^3 designs, sometimes supplemented with a center point. Of course, it sometimes becomes necessary to block the design.
EVOP can entail small incremental changes to that little or no process rejection is generated. Large sample sizes may be required to determine the appropriate direction of improvement. The method can be extended to more than two variables, using simple main effects experiment designs.