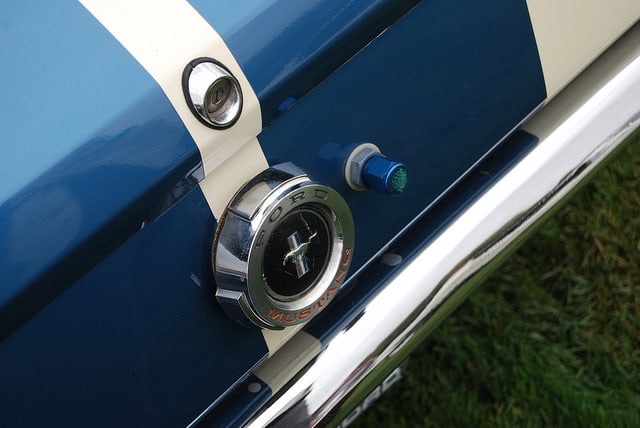
Poka-Yoke Error-proofing is the act of making errors impossible through great design. Defining requirements or ensuring continuous flow are good things but are not entirely part of error-proofing.
A great example for anyone driving in the US is gas pump nozzles’ different shapes and sizes. I can remember one bleary-eyed road trip in college where I was half awake when I tried to fill my 1986 Buick Regal with diesel instead of regular! Fortunately for me, poka-yoke has been used in the design of the gas nozzles; diesel gas is a triangle shape and thus impossible to fit in the cylindrical gas receiver my car had! That was great error-proofing.
History of Poka-Yoke Error-proofing
Coined in the 1960s in Japan, Poka Yoke means “Fool-Proofing” and is a tool used to avoid inadvertent errors. The tool ensures that proper conditions are in place for every step of the process such that there is no room for defects while operating. In other cases, it detects and fixes the defects as early as possible.
Poka-Yoke is a vital tool in lean manufacturing since it helps the people and processes work the first time correctly. It helps to phase out defects during the process and in the products by improving quality and reliability. It is worth noting that it does reduce both machine and human errors in the work processes and products.
When to use Poka-Yoke Error-proofing?
The ideal time to use the technique of Poke-Yoke is when a process or product is likely to have an error or something may go wrong. You can easily introduce the Poke-Yoke technique in both the manufacturing and service industries. Poke-Yoke captures errors like poor process operations, improperly adjusted machines, or incorrectly used tools (setup errors).
Secondly, it flags missing parts on the production line (missing parts errors), incorrectly used parts (improper parts error), processes or products that fall below quality standards (operations errors), and unadjusted machines and parts (measurement errors). Consequently, this last example includes improper dimensions of the supplies or parts used.
How to use Poka-Yoke Error-proofing?
There are several steps that one can follow to use Poke-Yoke in their work operations:
Step 1: The process or operation that needs fixing should be identified using a Pareto chart and analysis.
Step 2: Assess and understand the defects in the process that may lead to failure. Keep in mind the 5-whys during this stage.
Step 3: Decide the strategy to be used for effective Poka-Yoke. Some of the options include
- Shut-out strategy: this is a strategy that prevents the error from being committed
- Attention strategy: which brings attention to the defect when it is being committed
- Comprehensive approach: which is a combination of options
Step 4: First, determine the appropriate strategy needed for the situation. This can be done using a contact, constant number, or sequencing method. A contact is any physical trait that can catch an error. Constant number finds errors in cases where the trigger behind the error is the absence of a certain number of actions. Finally, a sequencing method uses a checklist to tally the completion of steps in the process without error.
Step 5: Run a trial test to ensure the chosen method is appropriate and effective.
Step 6: Once ensured that the method chosen is good, train the operators for the same, review the performance, and measure the success to verify the Poka-Yoke strategy.
Poke Yoke Videos
ASQ Six Sigma Black Belt Certification Poka-yoke Questions:
Question: A company has bought a system that prevents orders with incorrect information from being sent to production schedules. This is an example of which of the following lean tools? (Taken from ASQ sample Black Belt exam.)
(A) Standard work
(B) Kanban
(C) Poka-yoke
(D) Visual factory
Answer:
ASQ Six Sigma Green Belt Certification Poka-yoke Questions:
Which of the following is an example of mistake-proofing?
(A) Using an X Bar – R chart to prevent errors
(B) Using 100% inspection to detect and contain defects
(C) Using color coding as an error signal
(D) Having the team that created the errors repair them
Answer:
Comments (3)
Would I include the Lean Notes under the Control section in DMAIC?
Thank you,
Sarah
I mean improve phase?
Hi Sarah,
If you mean for the course, I have Lean spread through out as well as in it’s own section.
If you mean in practical application, yes, you could apply many lean techniques (like Poka Yoke) in the improve phase. However you would likely also use other Lean techniques in multiple areas. For example, Value Stream Mapping, calculating Takt time could both happen in the Measure Phase and then again in the Control Phase.
Does that help?