Push-pull, also known as the lean inventory strategy, is remarkably effective in enhancing the efficiency and accuracy of the production process. In other words, push-pull demands a more accurate sales forecast and adjusts inventory levels based on the actual sale of goods.
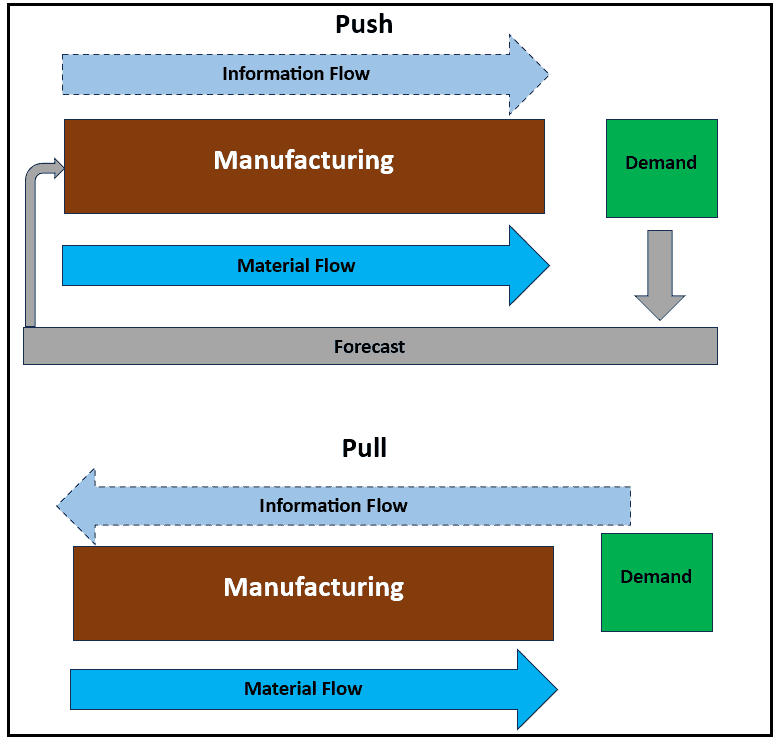
Push Systems
A manufacturing system in which production is based on a projected production plan and where information flows from management to the market in the same direction in which the materials flow. In other words, organizations produce goods based on market demand. It is also called make-to-stock manufacturing.
Push system is mostly used where the demand fluctuation is minimal. This is how many traditional production and project management environments have worked. This is effectively the opposite of how a pull system works.
Based on historical data, a push system initiates production by forecasting future demand and pushing goods or products through the supply chain. This method considers demand forecasts that trigger manufacturing while overseeing the delivery of finished products to distributors or retailers. Subsequently, these retailers sell the products to end customers.
A good example of a push system in the automobile industry is when manufacturers forecast demand for various spare parts based on historical data and produce them in bulk to achieve economies of scale.
Principles of Push System
- Production planning: Plan the production based on customer demand instead of waiting for customer orders
- Forecasting: Forecasting based on historical data to predict future customer demand
- Inventory: Efficient inventory management for meeting expected demand and reducing the risk of stockouts
- Timelines: Implementation for products with high lead times
- Risk Management: Risk management through market trend analysis and adjusting or planning the production
- Production distribution: Distribution alignment with various supply chain partners such as retailers or distributors
Pull Systems
A pull system is a lean manufacturing strategy used to reduce waste in the production process. A correctly managed pull system can eliminate multiple kinds of waste.
A pull system is set up to respond directly to internal or external customer demand. The purpose of implementing a pull system is to build products based on actual demand and not on forecasts. Just because you have spare capacity at any given point in the system does not mean you should produce more. Ultimately, this leads to excess inventory, which is just another form of waste.
Increased customer satisfaction occurs in a pull system as it manufactures products specifically to fulfill customer requests. With products made in small quantities, quality issues are identified faster compared to the push system. Additionally, this system maintains lower inventory levels as products are not produced until they are needed.
For example, the production process of the delicious hot beverage begins only when a customer orders. So, the customer generates a signal when they purchase a cup of coffee, effectively pulling materials through the coffee-making system, thus called a pull system.
Kanban is the most well-known approach for implementing a pull system. The Kanban card system provides a sign or signal by the next step in the process or downstream operation.
The pull system, also known as a Just-In-Time (JIT) system, delivers finished goods, materials, or work-in-progress when needed instead of merely accumulating inventory.
Principles of Pull System
- Production planning: Plan production once triggered by actual customer demand.
- Just-in-Time (JIT): Emphasis on Just-in-Time (JIT) to reduce excess inventory and waste
- Customer changes: Flexibility to adapt to changing customer needs and market conditions.
- Flexibility: Small batch production for efficiency and flexibility
- Production process: Implementation of a Kanban system for production control
- Timelines: Implementation for products with shorter lead times
Push Vs Pull
Push and pull systems represent two different approaches in supply chain management. In a push system, forecasts and historical data drive production, pushing goods through the supply chain based on anticipated demand. This proactive approach allows for efficient large-scale production but may lead to overstocking and increased storage costs.
On the other hand, In a pull system, actual customer demand triggers production, and the supply chain pulls goods as needed. This reactive approach reduces the risk of overproduction and minimizes inventory costs but requires a more dynamic and responsive production process.
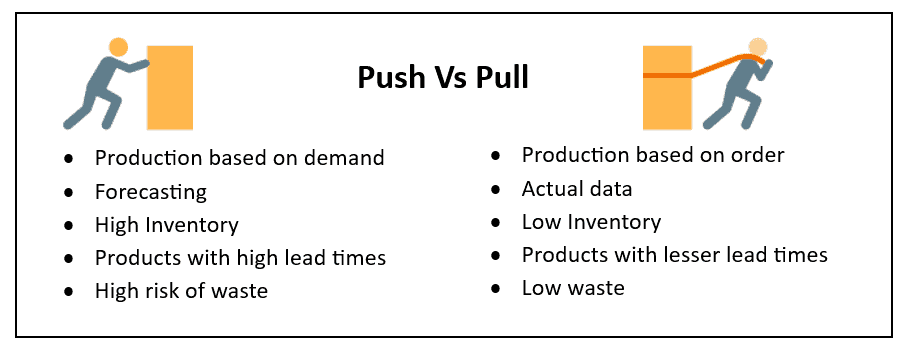
Choosing between the Push and Pull system
Choosing between a push and pull system depends on various factors, and understanding the characteristics and requirements of each system is crucial.
Organizations can use the push system if demand is stable, economies of scale are significant, and efficient large-scale production is feasible. This is especially suitable when lead times are long and maintaining inventory levels is not a concern. It is also called make-to-stock manufacturing.
On the other hand, a pull system is preferable in case of variable demand. It emphasizes actual customer orders, minimizes inventory holding costs, and facilitates customization or made-to-order production. Short lead times and a reduced risk of overproduction are additional advantages of a pull system.
What is a Push-Pull System?
A push-pull system is a hybrid approach in supply chain management, integrating both push and pull systems elements to be the most adaptable and balanced solution for their supply chain needs. Push and pull systems may work well together by bringing benefits from both systems. In the push-pull system, organizations use forecasting as a base to determine the quantity of goods in inventory while simultaneously using customer orders to trigger further production.
The push-pull system aims to leverage the efficiency and cost-effectiveness of push systems for certain aspects while maintaining the flexibility and responsiveness of pull systems to actual customer demand.
How Push-Pull System works
In a push-pull system, the process typically begins with a push approach and transitions to a pull strategy as products move through the supply chain.
Initially, the push system involves forecasting demand and producing goods based on these predictions. By relying on historical data and market trends, manufacturers proactively push a predetermined quantity of products into the supply chain.
The transition to a pull system occurs as products move along the supply chain. This shift is prompted by actual customer demand. Instead of continuing to push products through the chain, the system becomes more responsive, triggering production based on real-time orders and consumption data.
Benefits of using the Push-Pull system
The push-pull system helps businesses create a hybrid system that leverages the strengths of both approaches.
- The push-pull hybrid system combines the cost efficiency of bulk production in push with meeting actual demand in pull.
- It allows a more adaptive response to expected and unexpected customer demand changes.
- Integrating pull elements helps reduce lead times, improving product delivery.
- Balancing the advantages of push and pull, it achieves an optimized inventory management strategy.
- Improves overall customer satisfaction by meeting real-time customer needs.
- Combining both systems helps avoid overproduction and reduces excess inventory.
- Improves overall operational efficiency by integrating push and pull elements, streamlining the production process.
Example of Push-Pull System
Explain how the TV manufacturing industry establishes a push-pull system within a comprehensive supply chain strategy.
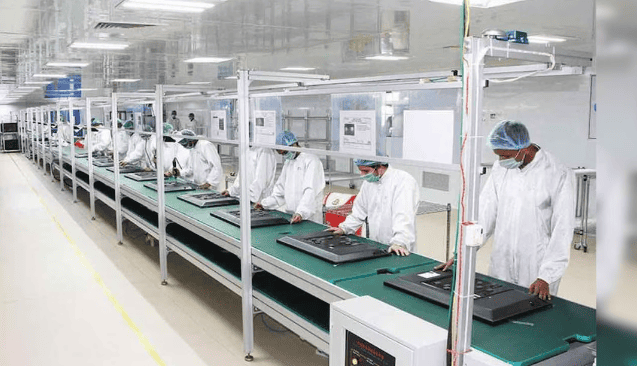
The push component starts in the manufacturing stage by leveraging historical data and market trends to forecast demand for different TV models. To achieve cost efficiencies, manufacturers produce TVs in bulk quantities and distribute them across regional warehouses or to retailers.
The pull component comes into play as the TVs reach the retail level. Retailers closely monitor consumer behavior and purchasing patterns and adjust their orders to align with customer demand. As certain TV models gain popularity, retailers place more orders and plan the additional production to meet actual market demand.
This push-pull integration in TV manufacturing provides a dual advantage. The push strategy ensures efficient, large-scale production, while the pull strategy allows for adaptability to changing consumer preferences.
Push-Pull System Videos
When you’re ready, there are a few ways I can help:
First, join 30,000+ other Six Sigma professionals by subscribing to my email newsletter. A short read every Monday to start your work week off correctly. Always free.
—
If you’re looking to pass your Six Sigma Green Belt or Black Belt exams, I’d recommend starting with my affordable study guide:
1)→ 🟢Pass Your Six Sigma Green Belt
2)→ ⚫Pass Your Six Sigma Black Belt
You’ve spent so much effort learning Lean Six Sigma. Why leave passing your certification exam up to chance? This comprehensive study guide offers 1,000+ exam-like questions for Green Belts (2,000+ for Black Belts) with full answer walkthroughs, access to instructors, detailed study material, and more.
Comments (2)
Excellent summary of a pull system, thank you
Very welcome, Dave. Thank you for the warm comments!